In this article
Remember, remember, the 5th of November?
One ERIKS customer will remember Bonfire Night 2022 for a very long time. Because that’s when ERIKS helped prevent six weeks' production, for this leading cement manufacturer, from disappearing faster than a misfiring rocket in the rain.
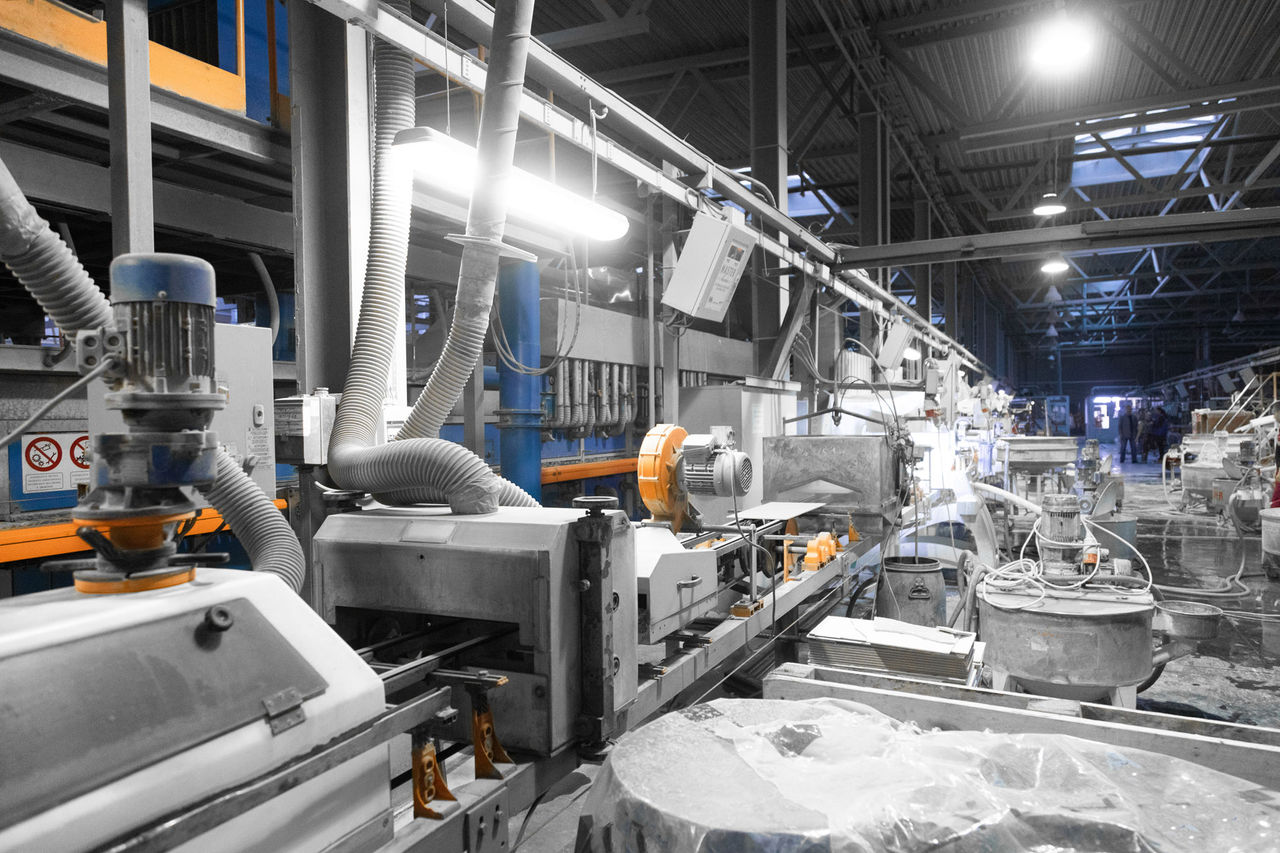
It was 8.20 in the morning on 31st October when ERIKS received an urgent call from the customer, raising the alarm about an issue with their raw mill motor. The raw mill turns quarried and crushed rock into meal, used to produce clinker for the manufacture of cement. Without the mill, there’s no meal. Without the meal there’s no clinker. And without the clinker, there’s no cement production.
ERIKS’ engineers mobilised immediately and were on site the same morning.
Initial investigations revealed damage to the motor’s brush gear assembly. A Baker Surge Test was performed fortunately there was no additional damage to the rotor main winding. The next step was to remove the brush gear to allow inspection of the full slip rings. It took only a quick look to reveal they were heavily contaminated with carbon and the Slipring contactor surface was heavily burnt and pitted.
If the slip rings couldn’t be salvaged, the repair would take an estimated eight weeks to supply new . With only two weeks’ worth of raw material stockpiled, the customer would lose six weeks of production.
Even if the rings could be salvaged and a successful repair completed, it had to be finished before the existing supply of clinker ran out, or production would have to be halted. Obviously it was essential to do everything possible to salvage the rings and complete the repair in record time.
Straightaway the engineers began to clean and repair the rings in situ. The work carried on next morning but, after testing the motor in the afternoon, the engineers decided more detailed investigation was required.
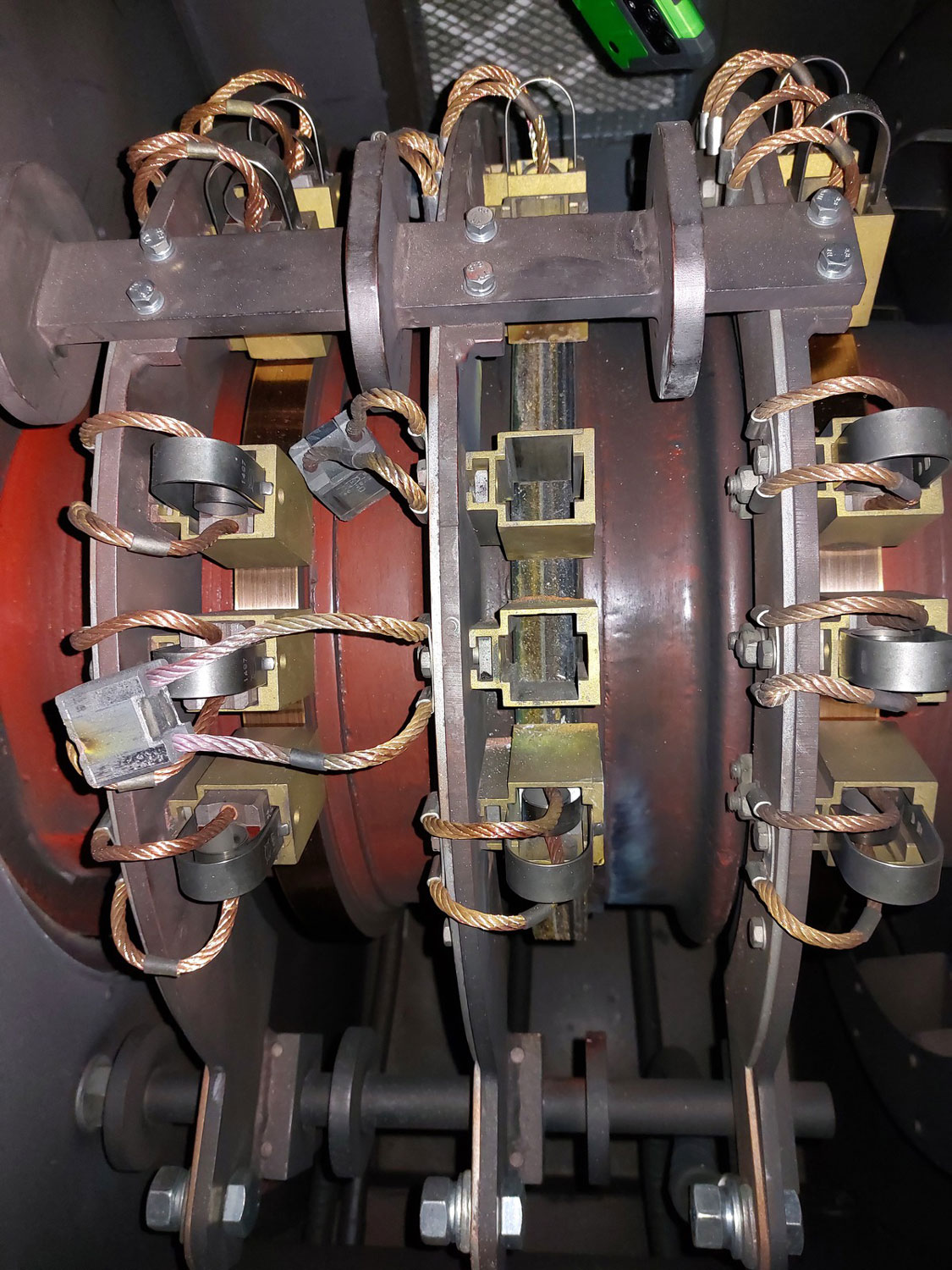
This would require off site repair in the Chesterfield workshop.
Round-the-clock repair
Moving things along as quickly as possible meant moving the motor to the ERIKS Chesterfield workshop, to enable optimum safety and 24/7 working.
While the on-site engineers prepared the motor for removal, an ERIKS vehicle made its way to the customer’s facility ready to collect. At the same time, arrangements were made to make more personnel available to work through the night at the Chesterfield workshop.
As soon as the motor was unloaded in Chesterfield, engineers set to work day and night on 2nd and 3rd November. Applying ERIKS’ experience and know-how, the slip rings were repaired in double-quick time, and the motor rebuilt. On 4th November a successful test run was carried out, and on 5th November the asset was loaded back onto the transport and delivered back to the customer’s site.
ERIKS’ engineers were on-hand once again to help with the installation of the repaired asset. By the time Bonfire Night was all over, the motor was back in place and the raw mill was ready to start operating once again.
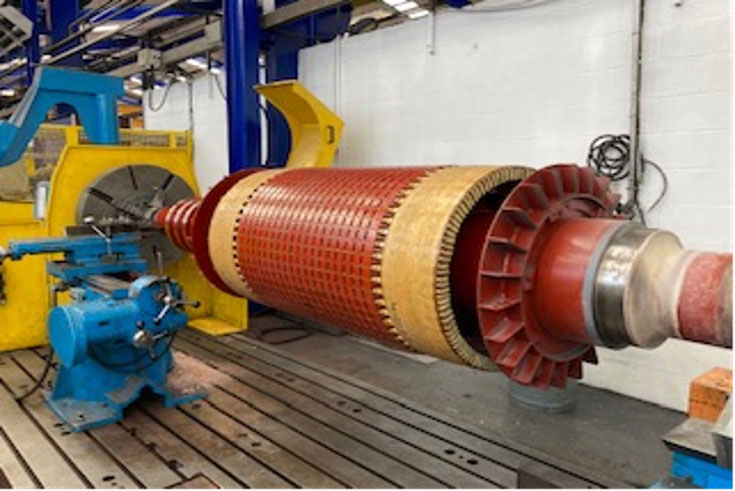
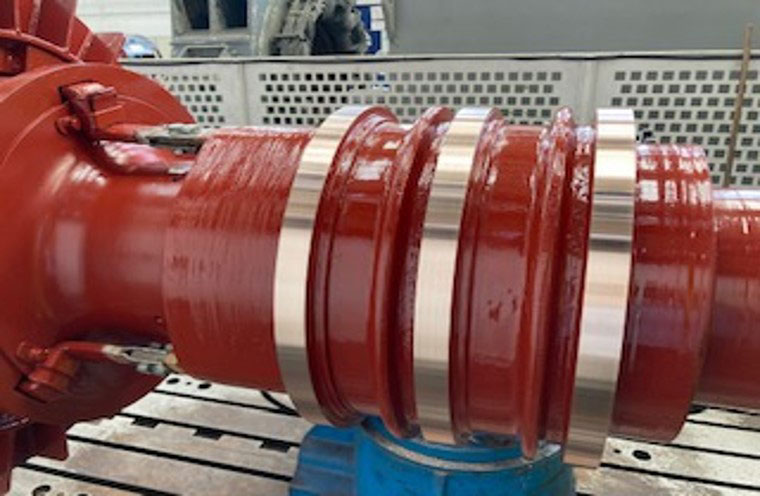
Time well spent
24/7 working enabled ERIKS to have the customer’s motor repaired and their raw mill back on stream three days sooner than expected. This saved 8,000 tonnes of production, worth a total of £560,000.
The slip ring repair and motor rebuild took 343 hours. This includes engineers’ hours on-site at the customer’s facility, the extra engineers on night shift at ERIKS’ Chesterfield workshop, and the re-installation of the motor once the work was completed.
Yet despite the huge extra demand on ERIKS’ resources, no other customers were affected. Once the motor left the workshop, ERIKS’ engineers continued to work overtime and extra night shifts to ensure all other jobs remained on schedule – because all ERIKS’ customers are equally important.
Going faster, going further
Delivering a quick and efficient repair was not the end of the job.
To help the customer avoid similar issues in the future, ERIKS have recommended new slip rings, and are preparing a quotation. A specialist is also making a visit to the customer’s site to review the brush gear maintenance schedule and propose potential improvements and training.
After all, no-one would want poor maintenance to mean all ERIKS’ hard work around Bonfire Night goes up in smoke.
For more information on Engineering solutions and to get in touch with one of our Engineering Specialists please contact your local ERIKS Service Centre, who will be happy to discuss your options.
#ERIKS #LetsMakeIndustryWorkBetter #Engineering #Repair #SlipRings #Cement #Chesterfield