In this article
Scream if you wanna go more reliably!
There aren’t many customer locations that leave ERIKS’ engineers with their hearts in their mouths. But when there were repeated breakdowns at Europe’s first fully-looping roller coaster, they needed a good head for heights as well as their usual engineering know-how.
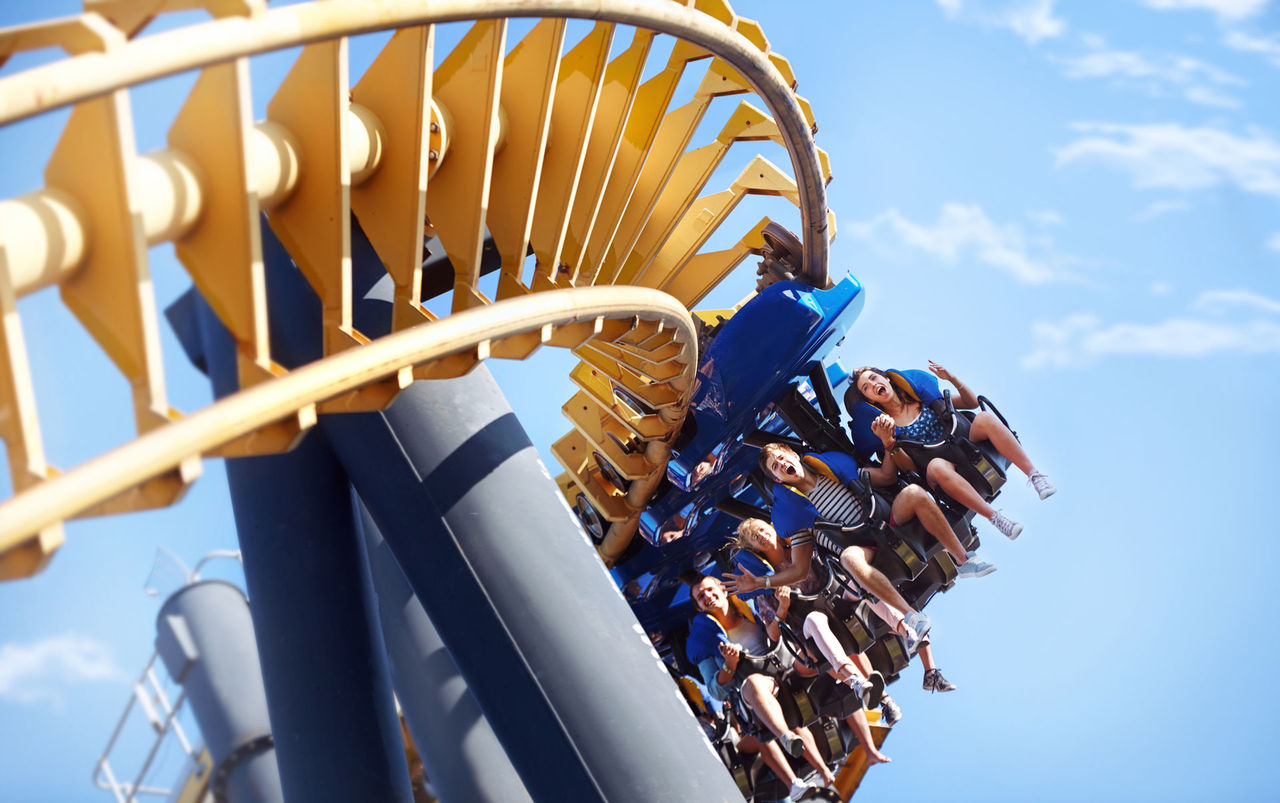
There are only three Arrow Development fully-looping shuttle roller coasters in existence. One is in Oklahoma, one in Colorado, and one at perhaps the UK’s most famous amusement park. Even though it’s still making visitors scream and shout, its operation hasn’t always been a smooth ride.
That’s partly due to the motor, manufactured to US – rather than European – standards. It was built with a 200V armature rather than the 400-460V which is common in the UK.
Temperature changes throughout the day often caused the motor to trip-out, and an earlier rewind to bring it up to European specification created an imbalance when switching from one motor to another – leading to more trip-outs and breakdowns.
The motor had been removed and repaired numerous times, but breakdowns were still frequent. The customer finally decided it was time to take action.
Safety first
The customer’s first instinct was to replace the ride entirely. After all, at over 40 years old, it was showing its age through constant breakdowns. But the ride occupies a prominent position in the centre of the park, on a very small footprint. The logistics of dismantling it and building a replacement in the same position were challenging.
So the question was: could ERIKS suggest a solution that would still provide the thrills – without the scary costs and complications?
Fortunately ERIKS had a maintenance upgrade proposal to make the existing ride more reliable, and to do it more cost-effectively, and in a shorter time-frame. The proposal involved new re-specified motors, repurposed drive equipment, and electrical modifications to ensure the electrics worked seamlessly with the new motors.
Of course all these proposed changes had to be reviewed and approved by the customer’s safety consultants. Not only did they have to check that the acceleration G-forces would remain within the specified tolerances, but also that the mechanical strength of the new components met the required safety standards.
With the proposal approved by the safety experts, the customer gave ERIKS just one week – during an annual closure – to carry out the upgrade. Unfortunately that one week was in November, and at times the temperature at the top of the ride dropped as low as -6°C. So for the ERIKS engineers working at height, what was already a white-knuckle ride became a blue-fingered test of their endurance.
Along for the ride
The old and unreliable (Stab-Shunt wound) motors were lifted out and lowered to the ground by crane. Then three new 100kW shunt-wound DC motors (two for duty and one for spare) were lifted into position on newly manufactured and installed motor mounting bed plates.
After consulting with the customer and safety consultant, the existing AB Powerflex DC drive was repurposed. Its supply voltage was increased to 400V AC and its internal configuration changed to compensate for the new motors and tacho generators. Its output was increased from 200V to 400V, and an additional thermal monitoring relay was installed for additional protection. The new configuration also eliminated the step-down transformer required by the old system.
Commissioning of the AB Powerflex DC drive was then carried out to achieve the desired launch cycle, acceleration times and G force limits agreed with the safety consultants.
Once the rollercoaster was ready for operation, the customer’s safety consultants carried out a further three days of safety testing. This included running the ride with sandbags in the seats to test the G-force. But that wasn’t enough to satisfy ERIKS’ lead engineer that the upgrade was a job well done.
A few weeks later he went back to the amusement park, this time with his children, and tried out the rollercoaster himself. Now that’s real dedication.
In the loop
The roller coaster upgraded by ERIKS was first opened in 1979, at a cost of £1,000,000.
As Europe’s first fully looping roller coaster – known as a ‘launched loop’ model – it consists of two raised sections of track, with a vertical loop in the centre. Customers climb a series of stairs to reach the loading station, from where the train is launched. It then travels into the loop and up onto the second platform, where it repeats the process in reverse.
The ride reaches 17m (56ft) at its highest point, with a drop of 14m (47ft). The overall length is 194m (635ft) and the top speed achieved is 45mph with a G-force of 4.
For more on how we can help with Engineering, Repair and Replace, please contact your local ERIKS Service Centre, who will be happy to discuss your options.
#ERIKS #LetsMakeIndustryWorkBetter #Reliability #Motors #Engineering