In this article
Getting Torpoint Ferry back on track
Just imagine. Public safety at risk, severe commuter delays, and a media frenzy all hit at once. Now throw in a global pandemic. You can understand why many thought they were fighting the impossible. But as the Great Nelson Mandela once said: “It always seems impossible until it gets done.”
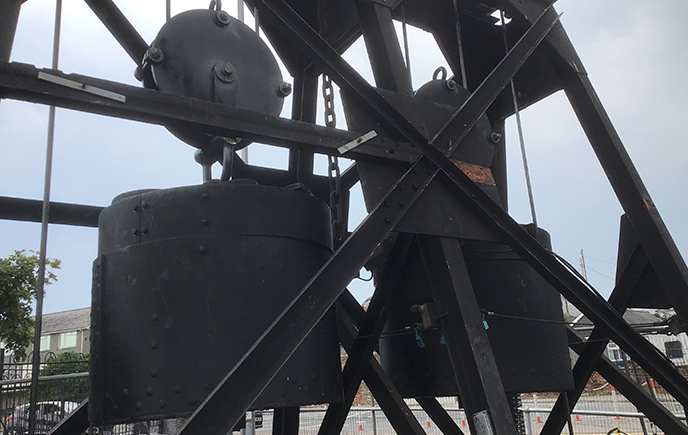
Having previously completed a guide chain tray sheave project at Torpoint Ferry Terminal, ERIKS Power Transmission Product Business Unit were invited back to investigate critical failures on the gantry sheaves at the port which were causing severe disruption to service.
Just so you get a feel for the scale and importance of the project, the Torpoint Ferry is the largest chain ferry service in the world, and the UK’s busiest inland waterway crossing, catering for the demands of 8,000 vehicles and 1,500 pedestrians every day, operating 24/7/365 regardless of conditions.
With service already reduced with one ship out of commission due to a scheduled 14-week overhaul, the potential for a second ferry down was increased, worrying terminal staff and the local community. Understandable considering maximum capacity was only three ferries. Pressure from the media was heating up, two-hour delays were being touted, and serious impacts to commuters in the pipeline, if a resolution wasn’t found, and quickly.
The pandemic hit
Investigation complete. Plan devised. Great start. From scratch, ERIKS Engineering Projects Team were to design, configure, manufacture, and supply the correct components to enable the tricky rebuild of the gantry sheaves at either end of the port.
But problems hit early that were out of ERIKS’ control. Cue the impacts of COVID-19 and the restrictions imposed by the then first lockdown.
Understanding how critical this repair was, work quickly commenced in sourcing the required parts to begin the rebuild. Confidence wasn’t at its peak given the current situation, with the Ferry Manager stressing that this was “Impossible in lockdown.”
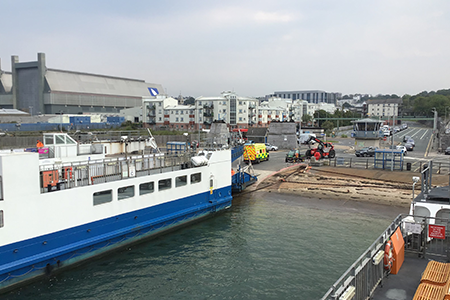
Luckily for the customer and users of Torpoint, the ERIKS engineering team didn’t share this lack of confidence, knowing the strengths of our supply network and the know-how of our in-house technical experts.
Off-the-shelf not an option
With the proposal agreed in March, the parts were now on order and the engineering work got underway. There were currently no drawings available, and due to the bespoke nature of the design, unfortunately an ‘off-the-shelf’ was solution wasn’t an option. So, the first task for ERIKS was to redesign the blueprints and with very little to go on.
Utilising the limited samples, with no formal load calculations or FEA (Finite Element Analysis) analysis available, together with consultation with Tamar Crossing engineer’s, CAD design drawings were prepared and signed-off.
From drawings to reality
Designed decades ago, for operation with chains, the newly approved blueprints were to convert the sheaves back to the required rope format, while remaining fit for purpose with the current installation.
Following collection and delivery to our Plymouth Service Centre, strip-down and inspection were completed, then measurements taken and recorded.
The ERIKS team then began the bespoke engineering, with the full scope of the project including: 12-off sheaves assemblies in total were manufactured from high-quality steel, hardened, and tempered in the sheave throat.
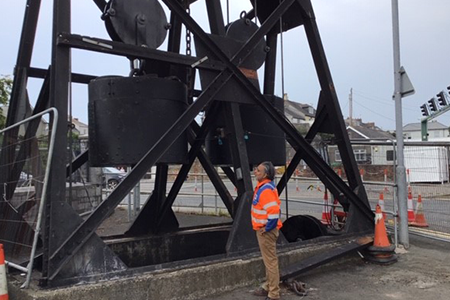
Which comprised of several components i.e. bronze bushes, pivot plates and arms and high tensile shafts. In addition to these components heavy lifting capacity Bow and Dee shackles were designed and manufactured.
The scope of the project also required mobile machining to be done on site due to number of permanently fixed components which formed part of the new sheave assemblies. This was organised, planned, and completed with specialist mobile machinery with the required Health and Safety measures in place due to working in a confined space.
Once all engineering worked had been completed, the new sheaves and pulleys were re-installed and to the joys of the Torpoint Ferry management team, and the locals of course, service was returned to full working capacity.
Looks like Nelson was right after all
From enquiry to back-in-service took approximately five months, which considering the initial fears that the terminal would have been out of commission for up to 12 months is quite remarkable, given the scale of the project combined with the many COVID-19 implications.
So, just like Nelson said: “It always seems impossible, until it gets done.”
For more information on Engineering, Repair and Replace solutions please contact your local ERIKS Service Centre, who will be happy to discuss your options.
#ERIKS #LetsMakeIndustryWorkBetter #BespokeEngineering #Manufacturing #Supply #COVID19