In this article
Keeping the Air (and Energy) Flowing: Fan optimisation for EfW efficiency and uptime
In Energy from Waste (EfW) facilities, few assets are as operationally critical yet often overlooked as the fan systems. Whether supplying combustion air, managing flue gases, or maintaining essential process ventilation, fans are integral to stable and compliant plant performance. Operating continuously in high-temperature, dust-laden environments - often difficult to access fan systems are among the most heavily used components on site.
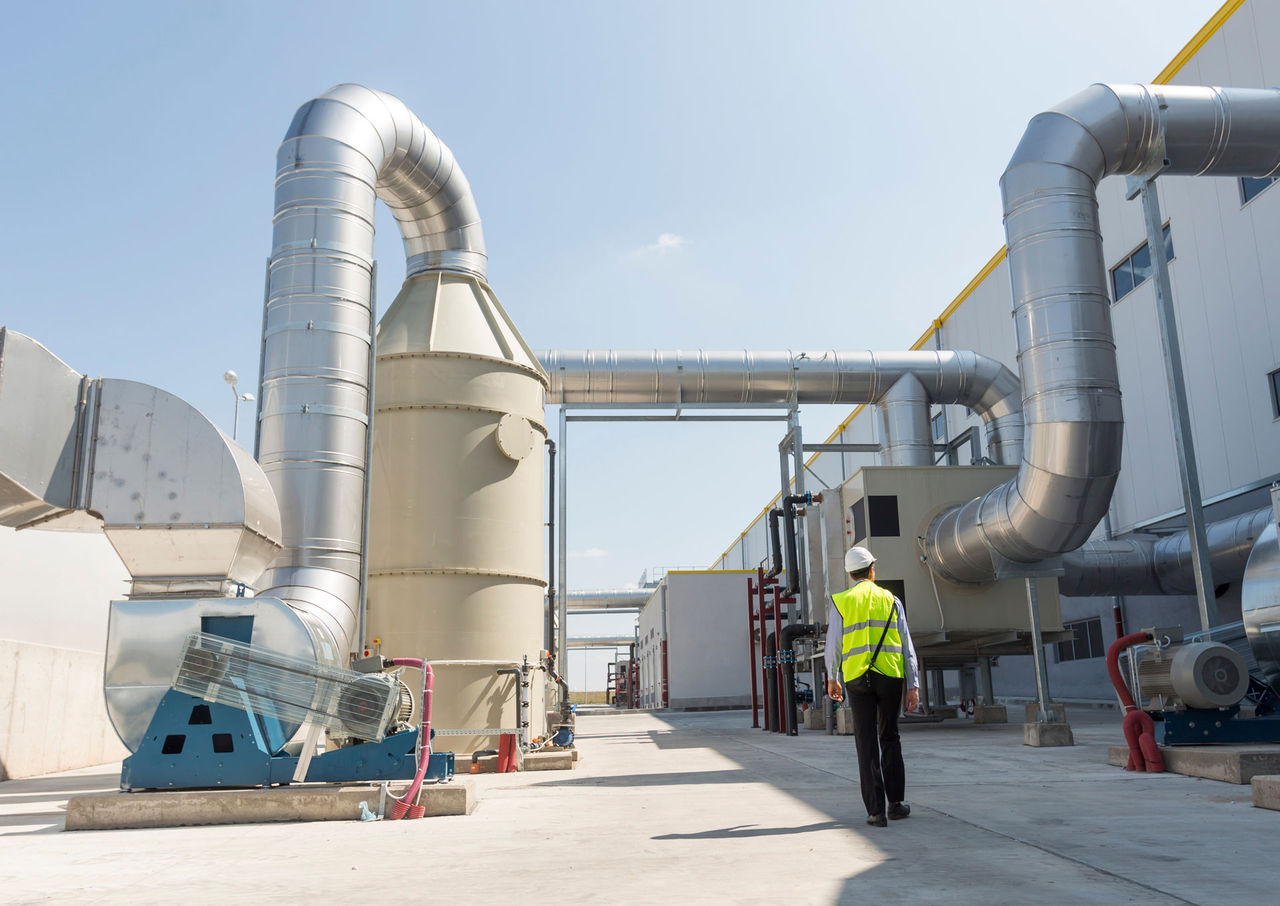
The usual suspects
Imbalance or misalignment can lead to excessive vibration, which over time significantly reduces the life and ultimately results in the failure of bearings and associated equipment. Harsh environments and particulate contamination accelerate bearing degradation, while improper or inconsistent lubrication compounds the issue. In many EfW environments, maintenance access is limited, meaning issues can develop undetected until they become production-limiting faults.
Motor reliability is another concern, especially in areas where ambient temperatures and environmental loads push equipment beyond its design parameters. And if fans are belt-driven, misalignment or excessive tension can lead to premature belt wear, reducing efficiency and increasing energy usage.
Smarter maintenance for a more reliable future
Keeping your assets running smoothly – and avoiding unexpected downtime – starts with being proactive. One of the best ways to do that is by ensuring your maintenance strategy leads towards predictive and preventative maintenance.
At ERIKS, we’re helping Energy from Waste (EfW) sites look ahead by shifting away from reactive maintenance and towards smarter, condition-based strategies. By using real-time data, we can spot issues before they become problems, meaning fewer surprises and more control.
Working alongside SKF, we recommend introducing monitoring systems whether it be a simple IMx-1 wireless, battery-operated sensors to monitor less critical assets in real-time, or for more critical applications the IMx-8, a wired solution which will allow for full high end remote diagnostics. These sensors track key indicators like vibration and temperature, flagging up early signs of wear, imbalance or developing faults.
Armed with this insight, maintenance teams can plan ahead with confidence, avoiding unplanned shutdowns and extending the time between overhauls.
The right lubricant and the right time
A well-planned and executed lubrication strategy does more than just extend the life of your fan systems – it also plays a crucial role in site safety and efficiency.
Manual lubrication in difficult-to-reach areas often requires planned shutdowns or working at height, increasing both downtime and risk. And even then, it can be inconsistent. That’s why we support the use of SKF TLDD automatic lubricators, which deliver precise and reliable lubrication at set intervals – no manual intervention required.
By removing the guesswork, these systems help prevent both under- and over-lubrication, two of the biggest causes of premature bearing failure. When combined with the right bearing selection – like SKF CARB toroidal bearings, which allow axial displacement, or SKF Explorer self-aligning roller bearings, which handle contamination and misalignment – you get longer bearing life, safer operations, and far less maintenance disruption overall.
For particularly challenging or restricted access areas, SKF Cooper Split Roller Bearings offer the ideal solution. Their split-to-the-shaft design means they can be installed or replaced quickly and safely, without needing to dismantle surrounding equipment – saving time, reducing risk, and getting your operations up and running faster.
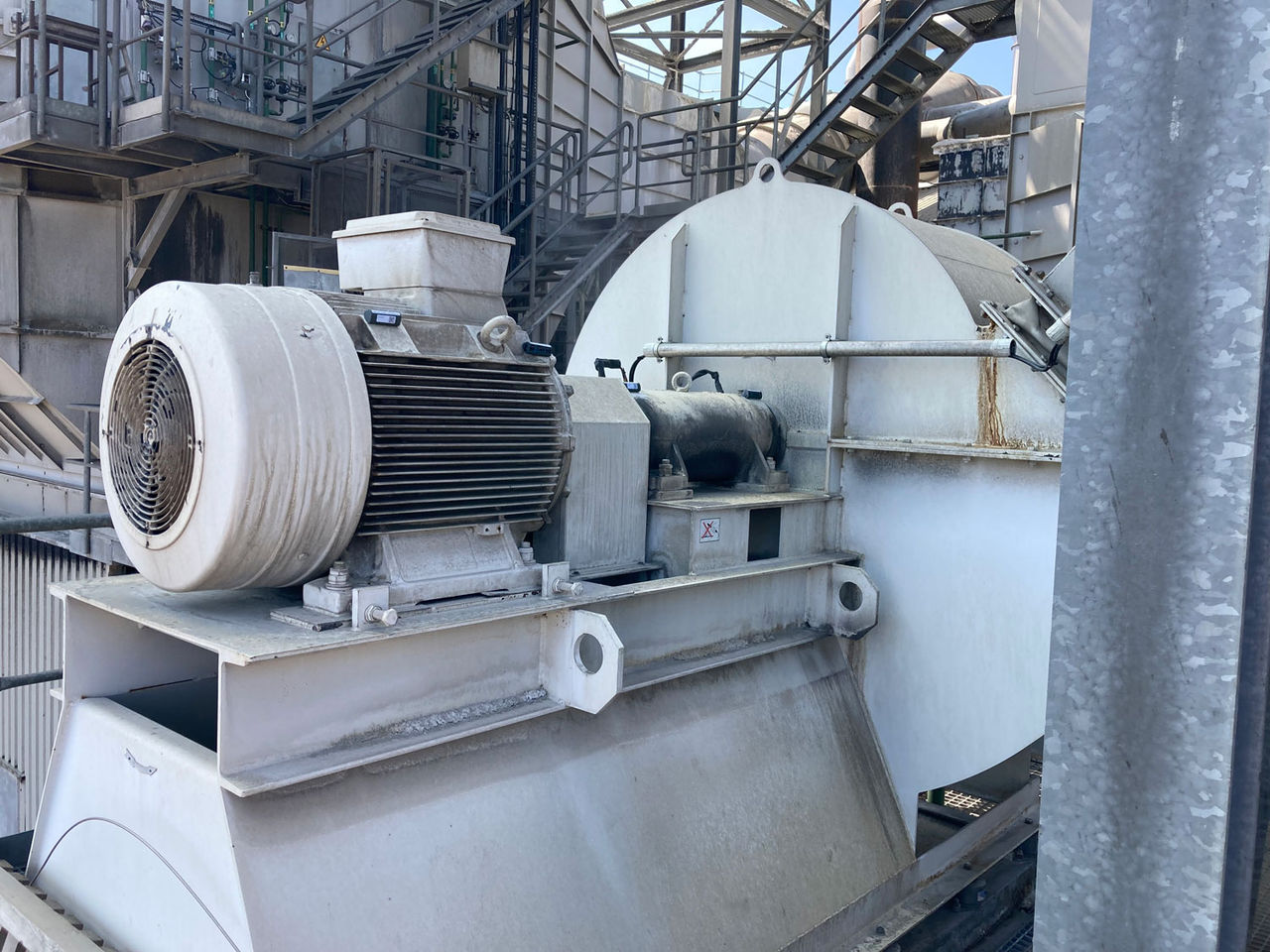
Breathe new life into fan systems
In many cases, the fan systems in operation were specified years ago under different compliance standards. As energy prices continue to rise and legislation tightens, we help customers assess the real-world performance and cost-effectiveness of their current assets.
Replacing ageing IE2 or IE3 motors with high-efficiency WEG IE4 or IE5 alternatives can lead to significant energy savings, particularly when paired with Fenner® variable speed drives that allow fine-tuned control aligned to actual process demand. Unlike fixed-speed motors, this solution enables smoother ramp-up, reduced mechanical stress, and energy use that directly reflects the operational needs.
Beyond motors and drives, our engineering support extends across the full drive system. Where belt drives are used, we recommend upgrading to Fenner® Torque Drive PLUS belts, which deliver higher torque capacity and near-perfect efficiency, eliminating the slip losses common with conventional belts. Accurate pulley alignment and tensioning is also essential to prolong belt and bearing life, and we support this through precision installation tools and service support.
Tailored support driving long-term reliability
While equipment specification and upgrades form the foundation, the key to long-term reliability lies in structured maintenance practices.
Rather than relying on fixed intervals, our support is tailored to real asset condition and operating context. For some sites, this may mean implementing a tiered reliability approach, starting with basic vibration alerts, such as those mentioned above from SKF, to scaling up to full integration with our Smart Asset Management (SAM) platform for advanced trend analysis and failure prediction.
Where failures do occur, we offer on-site fan balancing, shaft inspection and repair, and full overhaul services including full removal, overhaul and installation, all delivered by our specialist electro-mechanical teams across the UK & Ireland.
Ultimately, fan systems in EfW plants should be viewed not as consumables but as critical, high-value assets that directly influence throughput, safety and environmental compliance. With the right engineering focus, performance data, and support, it's possible to significantly extend the operational life of fan systems while reducing total lifecycle costs.
At ERIKS, our approach is built on practical experience, cross-industry insight and a deep understanding of rotating equipment. We collaborate with your site engineers to actively understand your day to day pain points to provide proven solutions to improve equipment reliability, streamline maintenance activities, and ensure every fan system continues to deliver safely and efficiently day after day.
For more information on Renewables, or get in touch with your local ERIKS Service Centre who will be happy to discuss your options.
#ERIKS #LetsMakeIndustryWorkBetter #Renewables #EnergyFromWaste #EfW #Engineering #Reliability #SKF #WEG #Fenner
ERIKS in the Renewables Industry
The transition to renewable energy is accelerating, and ERIKS is at the forefront, delivering technical expertise, engineering support, and innovative solutions to build a greener, more efficient world.
Total Fan Solutions

With expert advice, the latest technology, and the most effective maintenance regime, we can help you increase the efficiency, reduce the energy use and minimise the costs involved in operating many of your assets, therefore eliminating:
- Premature failure
- Excessive noise
- Excessive vibration
- High temperature
- Poor access
- Unreliable maintenance