In this article
Electric motors and the reliability journey
The term ‘circular economy’ refers to a system based on the reuse and regeneration of materials or products to operate in an environmentally friendly way. ERIKS approach to electric motors echoes the tenants of the circular economy but we view it as ‘the reliability journey’. In this article we’ll look at how, by adopting this circular journey, businesses can become more efficient in how they handle their electric motors.
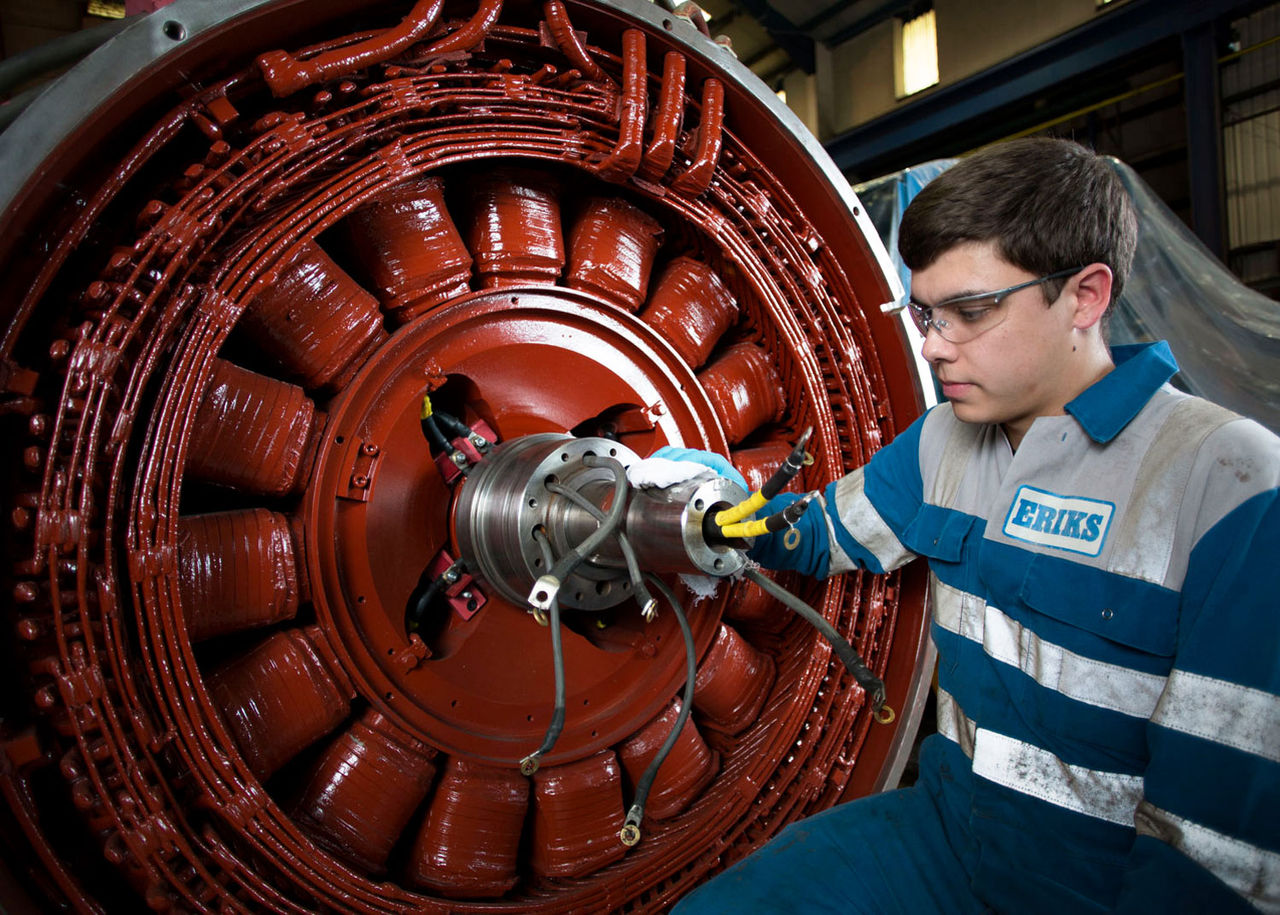
Stage 1: condition monitoring
The first step in the journey is condition monitoring. ERIKS’ Reliability Platform leverages sensors that collect data on vibration, temperature and other critical parameters in real time.
This data is automatically analysed using artificial intelligence and displayed on the ERIKS Smart Asset Management (SAM) platform. SAM trends the data, analysing current and historical condition and maintenance history and advises on the course of action.
Stage 2: assessment
The next step on the journey is the assessment phase. ERIKS Engineering Services has a growing team of more than 250 people and carries out over 7,000 individual motor repairs every year and can provide an independent assessment of a motor and advise whether to repair, replace or even upgrade it.
ERIKS has 13 motor repair locations around the UK and while all can handle AC and DC motors some of the sites do have their specialisms. The Chesterfield site is where the large motors (up to 11kV and 30 tonnes) are repaired and Haydock houses a specialist servo motor repair facility.
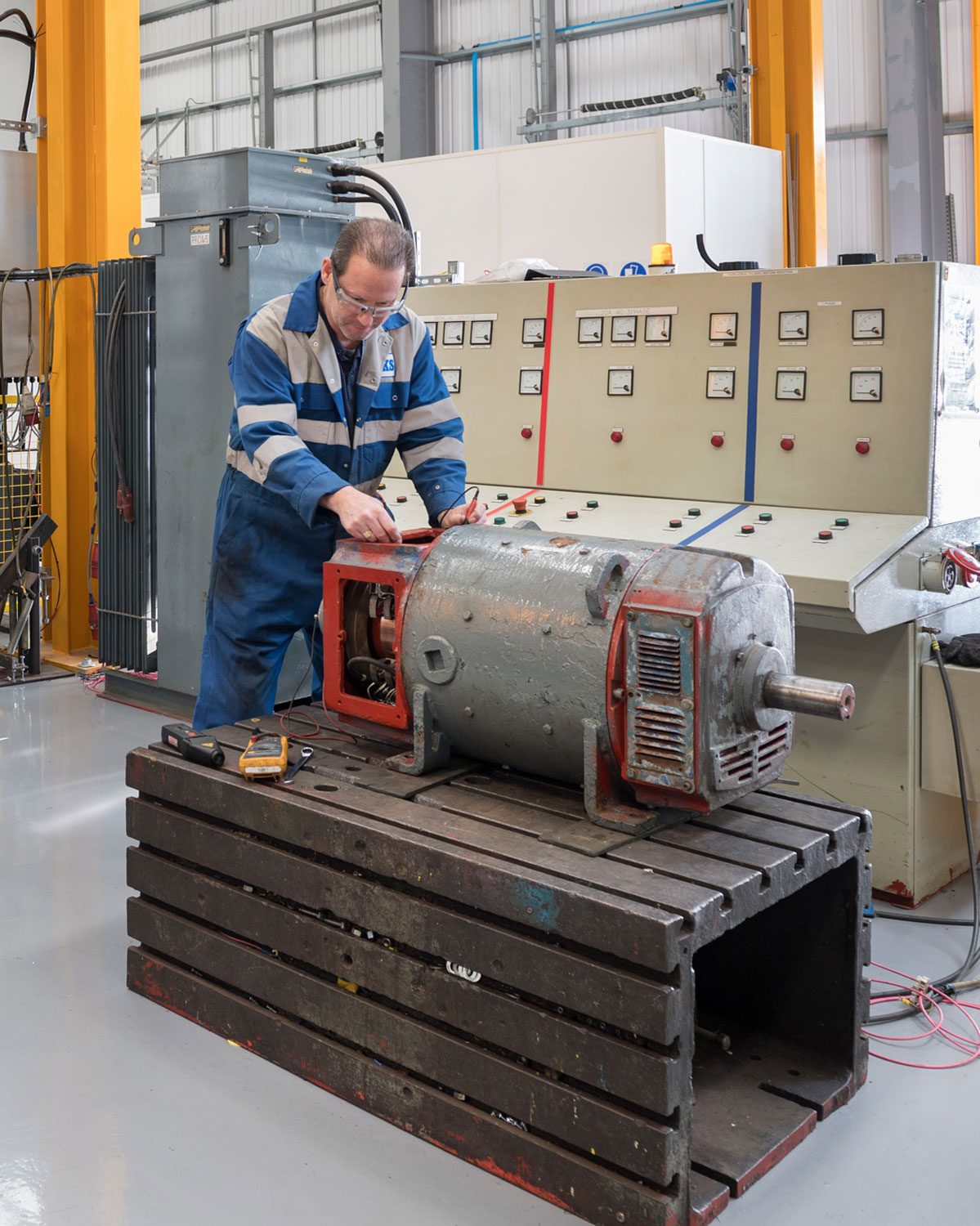
Stage 3: repair
Following the assessment and the motor’s arrival at an ERIKS workshop, the next phase in the reliability journey is the repair itself. An advantage for customers is the consistency of repair that ERIKS delivers across its network. First, ERIKS can handle the entire motor repair in-house (whereas many competitors will need to outsource certain aspects).
This in-house approach means the quality of repair is easier to manage and lead times are reduced. Similarly, ERIKS is one of the few manufacturers in the UK of commutators and slip rings for DC motors and in fact most other motor repairers outsource this type of work to ERIKS.
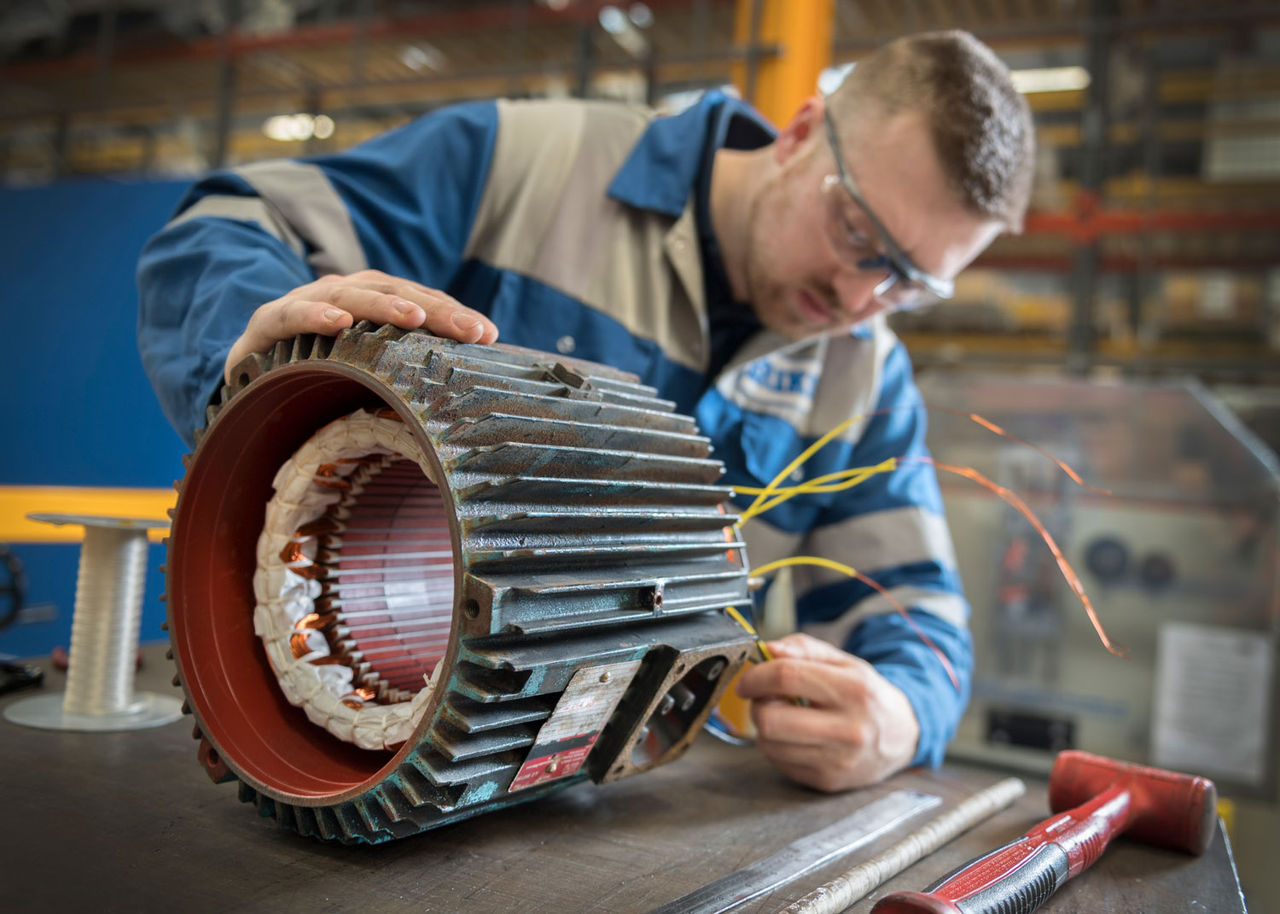
Stage 4: testing
Testing is a crucial part of the reliability journey and ERIKS tests every repair at predefined stages in the process. In many instances, for bigger units, customers can witness the testing as part of their quality procedures.
As well as dynamic balancing, the testing that ERIKS can offer includes partial discharge; Tan delta; insulation resistance; polarisation index; surge testing and IMCA broken rotor bar detection.
Stage 5: continual improvement
For larger customers all aspects of the electric motor reliability journey can be handled through an ongoing framework agreement.
Aside from improved pricing, achieved through economies of scale, this framework approach also offers customers a reduction in the number of vendors that need to be engaged and the elimination of any warranty issues that ‘multiple handling’ can create.
More importantly a Service Level Agreement (SLA) can ensure that the customer has the support they need, which may include 24/7 emergency response.
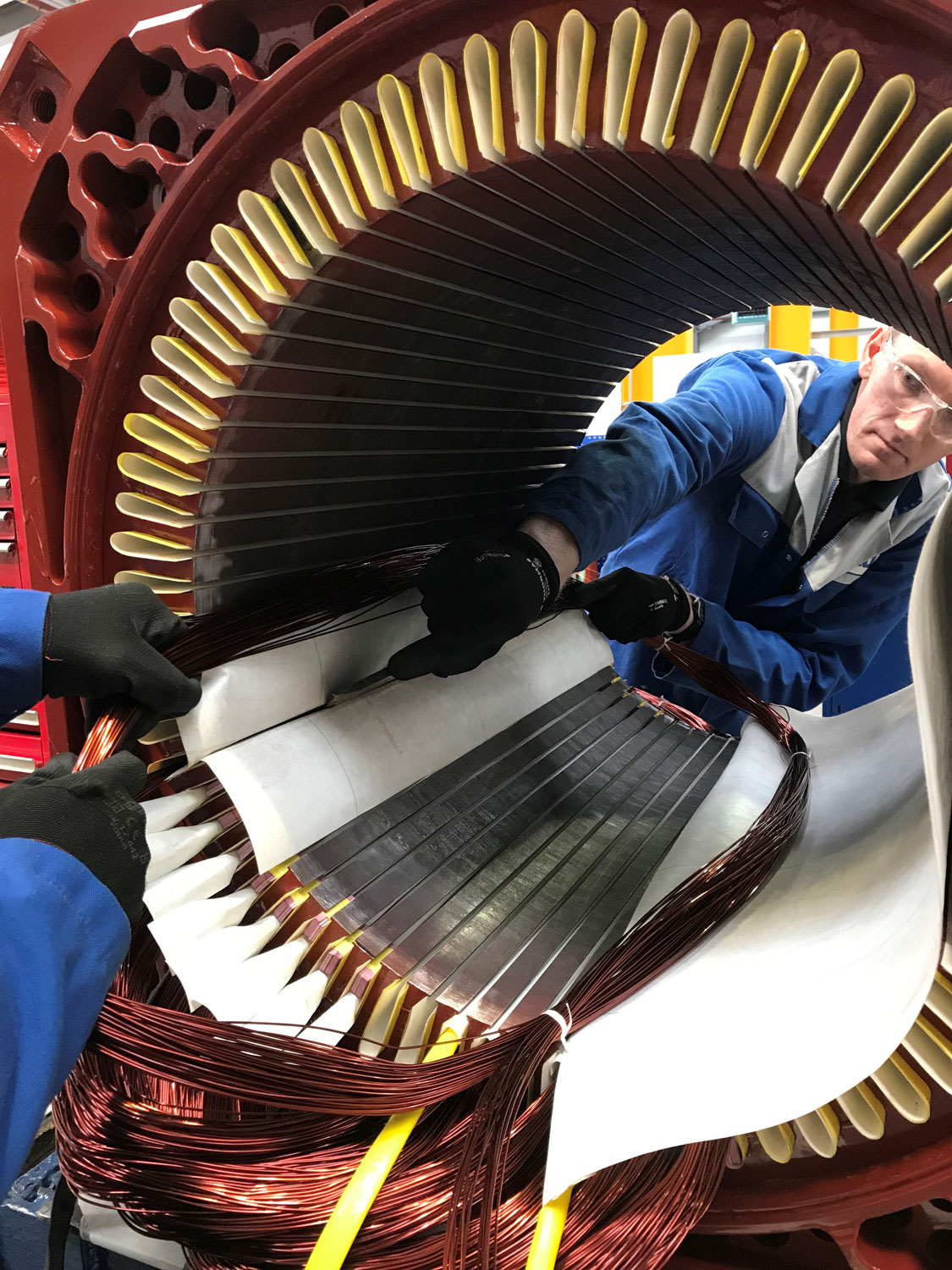
Stage 6: the completed journey
And so, we arrive back at where we started our reliability journey. From the benefits of the various points of the journey, at a minimum, we will be in a place where the motor is repaired and returned in ‘as new’ condition and if you engage with ERIKS as a partner we can optimise the performance and availability of your system.
There is no one size fits all solution but to start your journey towards reliability please contact ERIKS.
For more information on Engineering solutions and to get in touch with one of our Engineering Specialists please contact your local ERIKS Service Centre, who will be happy to discuss your options.
#ERIKS #LetsMakeIndustryWorkBetter #Engineering #Reliability #Repair #ElectricMotors