In this article
At your servos’ service
Maintaining and repairing your servo motors is a specialist service, demanding extensive technical expertise. Simply knowing the mechanics of motors won’t cut it. It’s not enough just to understand electrics. And even experience in electronics doesn’t go far enough. So where can you find the help you need?
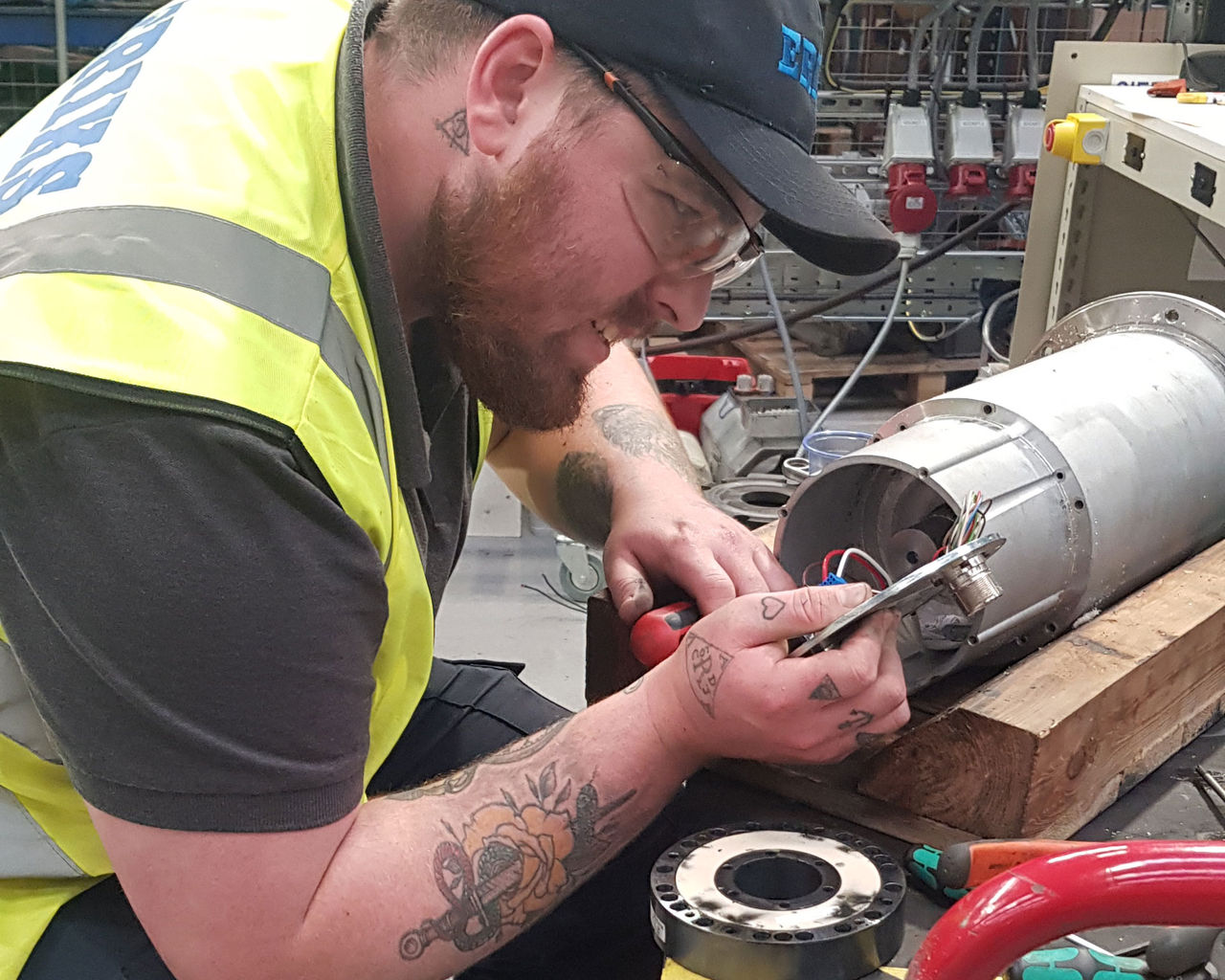
For the very specialist task of taking care of servo motors, Resolver servo motors, spindle motors, encoders, Hall effect sensors and tachometers, you need a very specialist skill set. One that combines all three of the disciplines above. Plus specialist equipment. Plus a dedication to fast turnround, to get these essential assets back up-and-running quickly. All of which you can find, at your service for your servos, at ERIKS Haydock.
No room for error
One thing which makes servo motors so challenging to repair is the precise positioning and control of their applications.
A servo motor comprises a magnet rotor, a stator and a feedback device, with an electric signal controlling the precise amount of movement required. To maintain the motor’s performance after repair or maintenance, it’s essential that the feedback device is restored to its exact original position.
In fact, re-installing and correctly repositioning the feedback device element is as essential a part of the job as any initial repair.
Even so, there are striking differences when you compare an OEM’s methods with ERIKS’ approach.
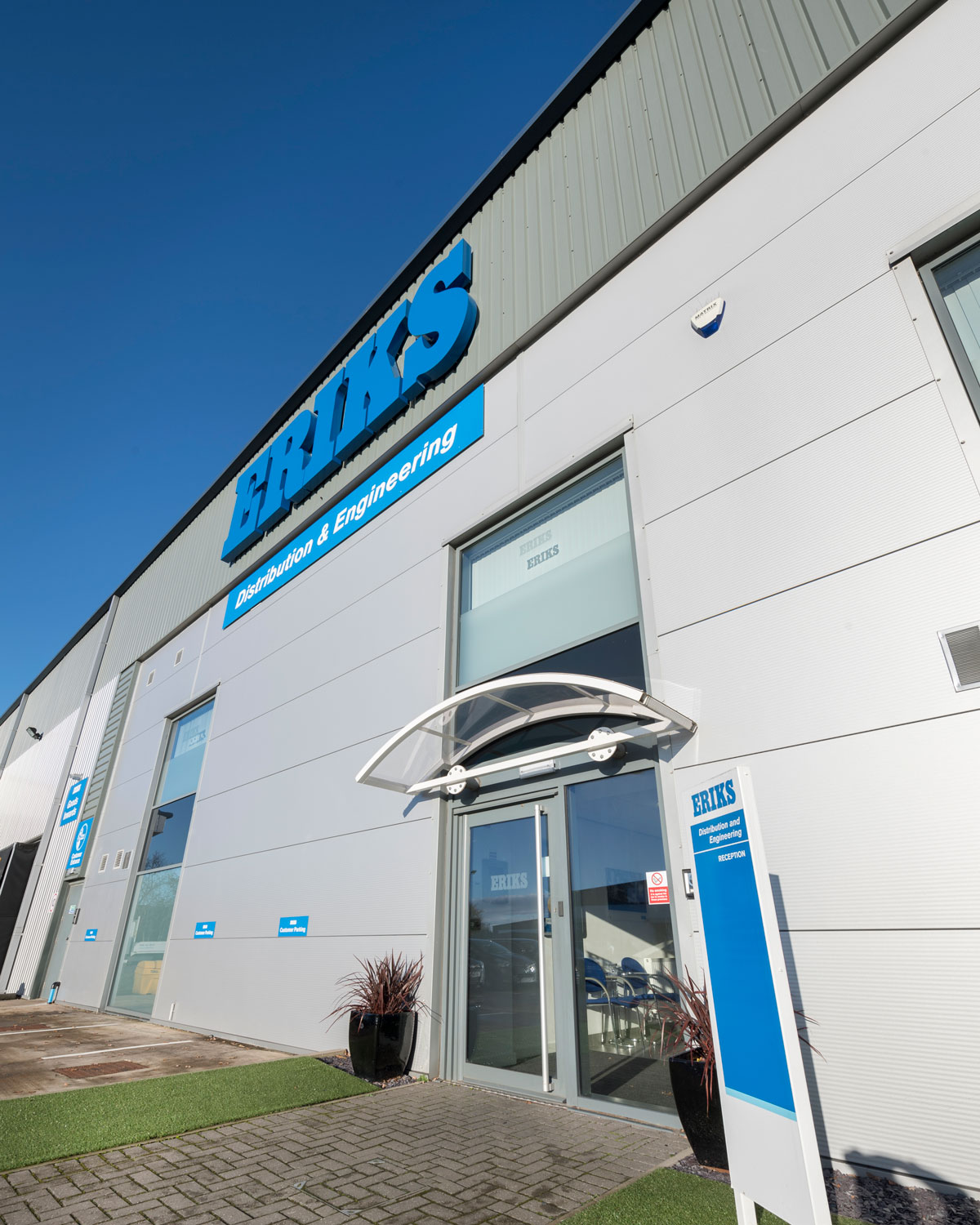
Flexible as standard
Sometimes customers find it hard to believe many OEMs work to a standard timetable for repairs. ERIKS, by contrast, works to the customer’s requirements. And the only thing that’s standard is the comprehensive servo overhaul that’s all part of the service.
Send a failed servo motor to an OEM, and it will be 10-14 days before you even receive a repair quote. But send it to ERIKS, and the motor will be stripped, inspected and a comprehensive repair report delivered in 7 days at most – often sooner. In fact, in an emergency, the report can be produced in a day.
And flexibility extends to the solutions, too. ERIKS’ renowned repair/replace impartiality means you’ll always get the right advice for you: whether your servo motor needs a simple test, a complex repair, or a complete overhaul.
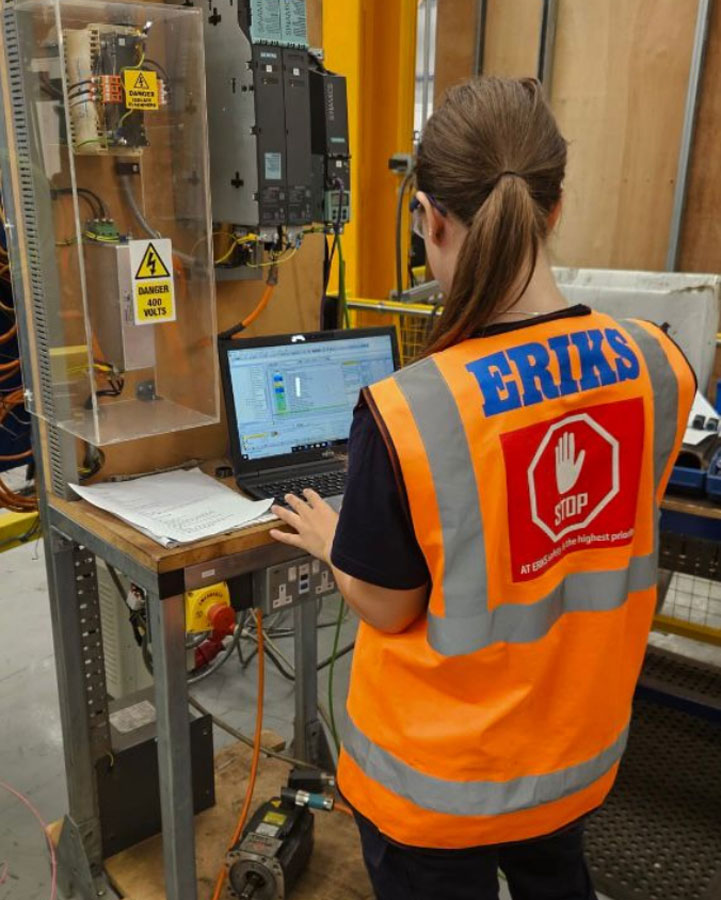
Working hard – because you do
One reason ERIKS’ speed of service is so much faster is that, unlike an OEM, ERIKS’s specialist servo repair centre operates 24/7, with an anytime call-out option to anywhere in the UK.
It’s a service which has proved itself time and time again.
For example, when a manufacturer’s popcorn-making machine failed on a Friday night, the OEM had gone home for the weekend. So ERIKS Haydock servo centre collected the failed servo motor, repaired and returned it, all by Saturday evening.
Another customer contacted their local ERIKS Technical Service Centre at Kings Lynn, with a report of a failed servo motor. The Service Centre arranged collection and delivery to ERIKS Haydock, while the customer installed their spare motor. When this also failed, it was delivered to Haydock by 10pm Thursday and was back at the customer’s site, repaired and fully-functioning, by 6am Friday.
Meanwhile the first failed servo motor, originally presumed ready to scrap, was refurbished by ERIKS and returned to the customer as a spare.
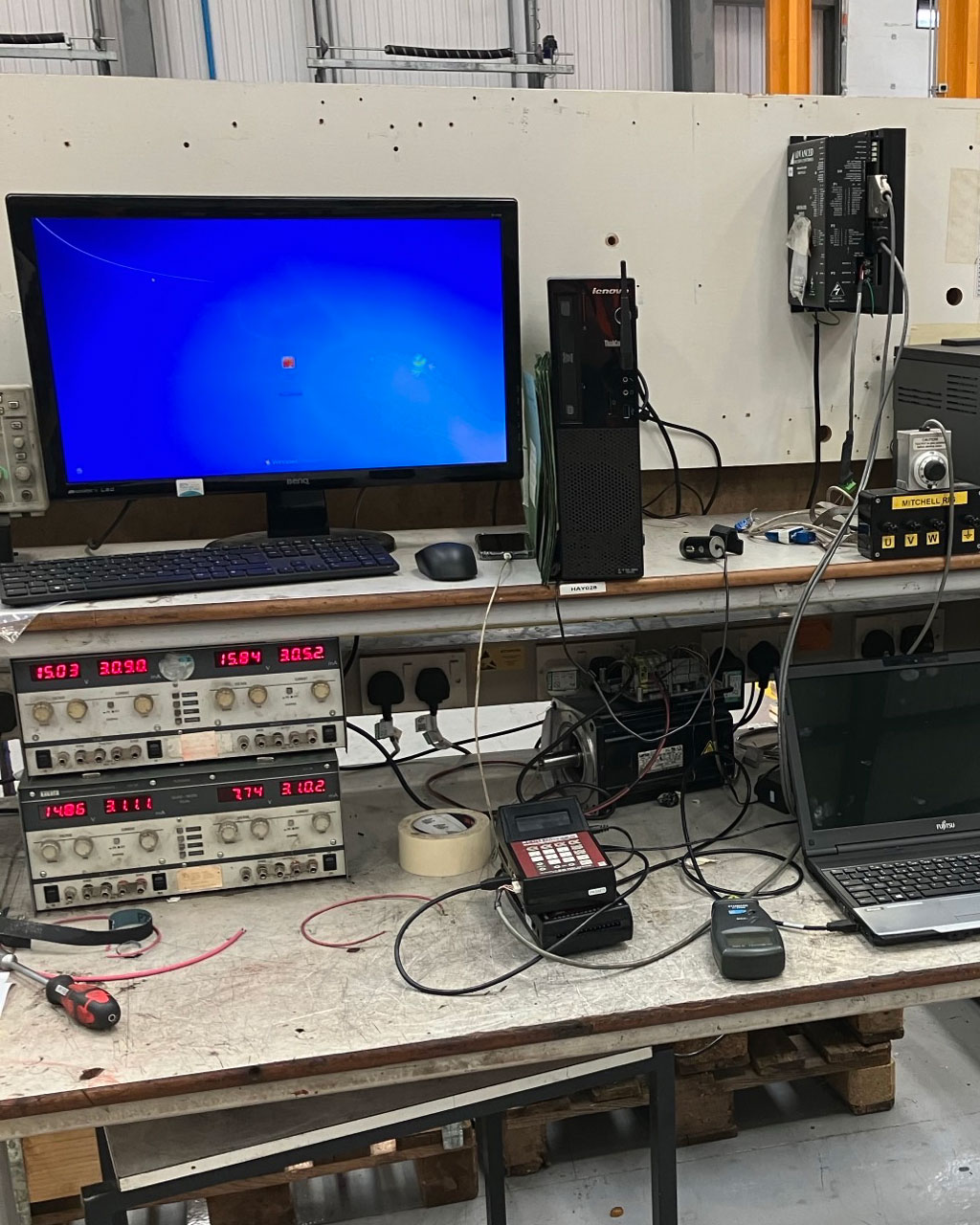
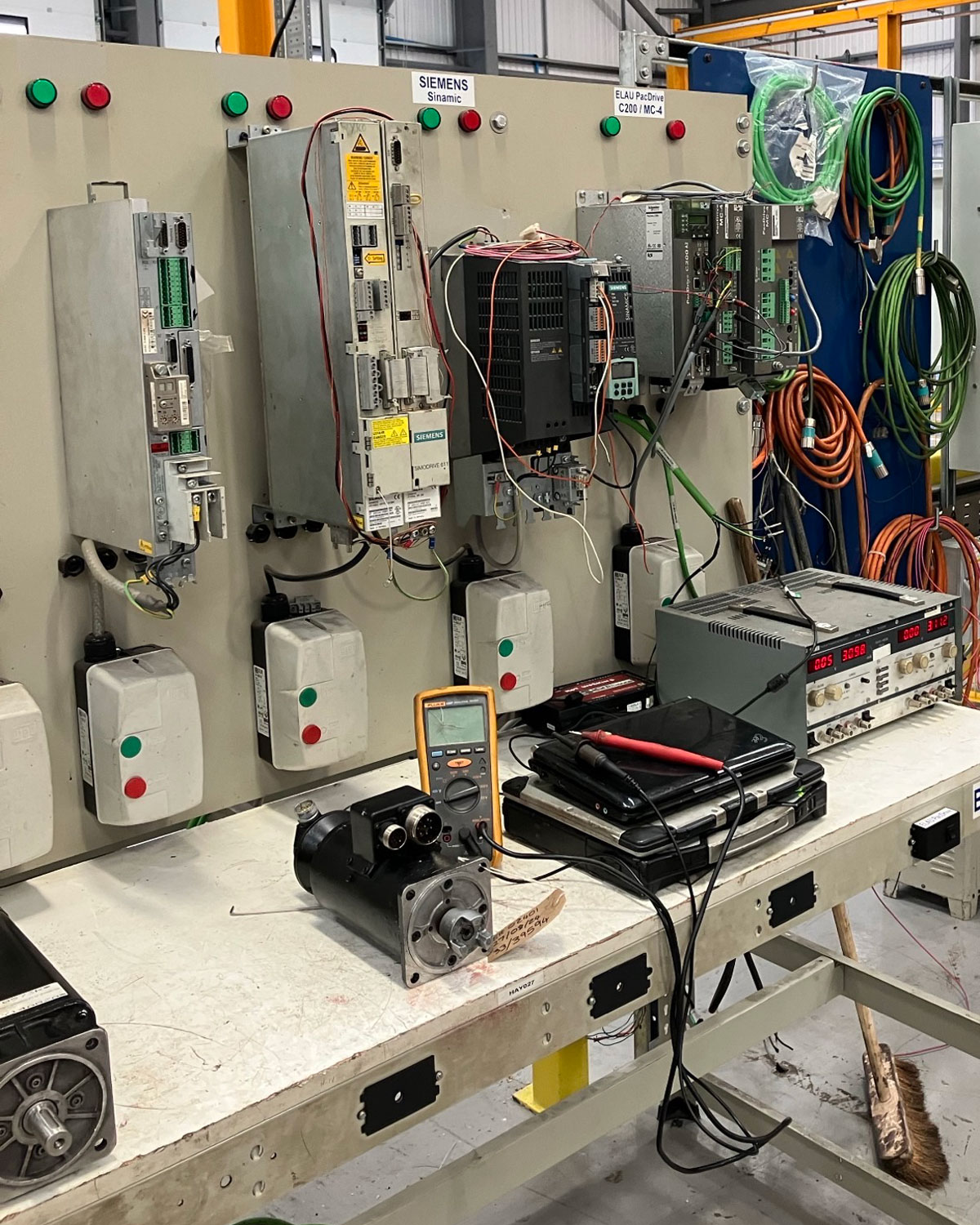
When know-how really counts
A major manufacturer ordered two servo motors from the OEM for a crane application – one for duty and one for spare.
When the first one failed on installation, they sent the spare to ERIKS Haydock, to test before swapping out the other. No fault was discovered, but when this spare was installed, is also failed to function.
This time, instead of the problem coming to ERIKS, ERIKS went to the problem: making an urgent visit to the customer. Using their servo motor know-how on-site, the ERIKS engineers quickly diagnosed the problem. The OEM had set the servo motor feedback to their factory standard, and not to the customer’s highly-specific requirements.
Once the issue was identified, ERIKS’ engineers had the new motor operating perfectly in less than two hours.
That’s not just any servo service. That’s ERIKS specialist servo service.
For more information or to get in touch with one of our Engineering Specialists please contact your local ERIKS Service Centre, who will be happy to discuss your options.
#ERIKS #LetsMakeIndustryWorkBetter #ServoMotor #Engineering #Haydock