In this article
Engineering Trust: The Making of an SKF Maintenance Partner
When ERIKS was appointed as the first SKF Maintenance Partner in the UK and Ireland, it marked more than just the awarding of a fancy title. It confirmed ERIKS as a maintenance provider trusted by SKF to deliver high standards of service, product knowledge and operational excellence on its behalf.
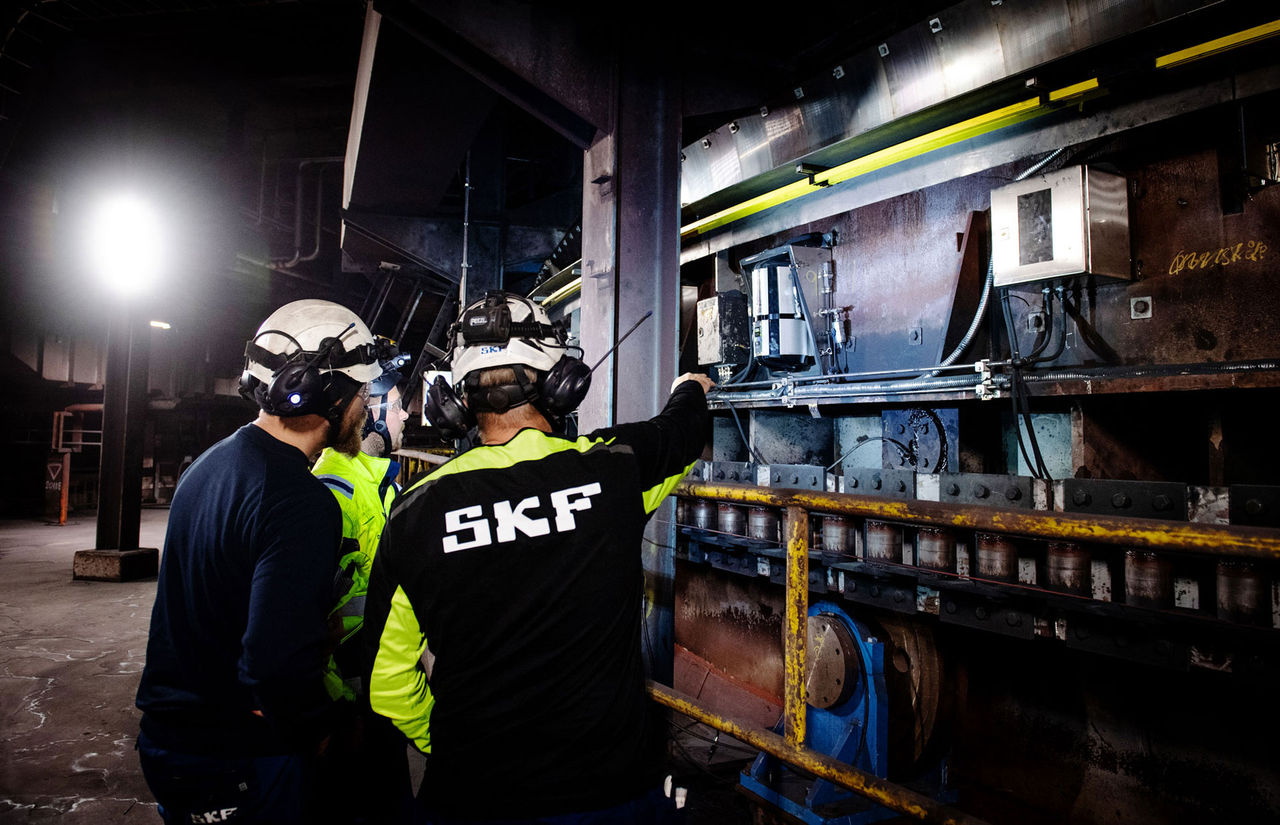
This status places ERIKS at the highest level of SKF’s distribution and partnership structure. It recognises ERIKS not just as a distributor, but as a technical partner able to support customers on the journey to maintenance maturity. Earning that level of trust required more than meeting a checklist. It demanded years of preparation, investment and alignment.
More than a supplier relationship
The SKF Maintenance Partner programme was co-developed with ERIKS in the UK. Initially created to strengthen collaboration and deliver a more unified message to industry, the model has since been adopted by SKF across Europe, the Middle East and Africa.
From the outset, the goal was to define something meaningful. The criteria had to be rigorous. The status had to be earned. And the outcome had to bring measurable value to the customer.
SKF based the programme on real-world capability, drawing from the services and standards already established within ERIKS. The result is a model that gives manufacturers confidence in the people they deal with, the repairs they receive and the long-term reliability of their equipment.
What it takes to become a Maintenance Partner
To achieve SKF Maintenance Partner status, ERIKS had to demonstrate way more than just strong commercial performance. The assessment focused on technical competence, service delivery, infrastructure, training systems and a clear commitment to continuous improvement.
The criteria include:
- Recognition as an authorised SKF distributor
- Full support for SKF’s core offering, including bearings, lubrication, maintenance and condition monitoring
- A national repair workshop network, certified to SKF audit standards
- Application engineering teams providing expert advice in the field
- Embedded training aligned with the SKF Maintenance Partner Academy
- Proven use of genuine SKF components in all relevant repairs and services
- Precision tools and measuring practices in line with SKF tolerances
Each ERIKS repair site was audited against these standards. In several cases, ERIKS supported the development of the audit process itself. This included site visits, documentation checks and evidence-based validation of working practices.
A culture of learning, built in
The Maintenance Partner model is not a badge. It is a commitment to ongoing development and technical depth, supported through the SKF Maintenance Partner Academy.
This structured programme provides training in mechanical services, condition monitoring, predictive maintenance and industry-specific applications. At ERIKS, these modules are embedded into internal systems so that staff across the UK and Ireland have consistent access to learning and can apply it directly to customer challenges.
Training begins with core product knowledge and advances through complex diagnostics and asset health assessments. Technicians and engineers are taught how to recognise failure modes, spot early warning signs and implement proactive solutions. These are not theoretical skills. They are used daily in site visits, repairs and customer consultations.
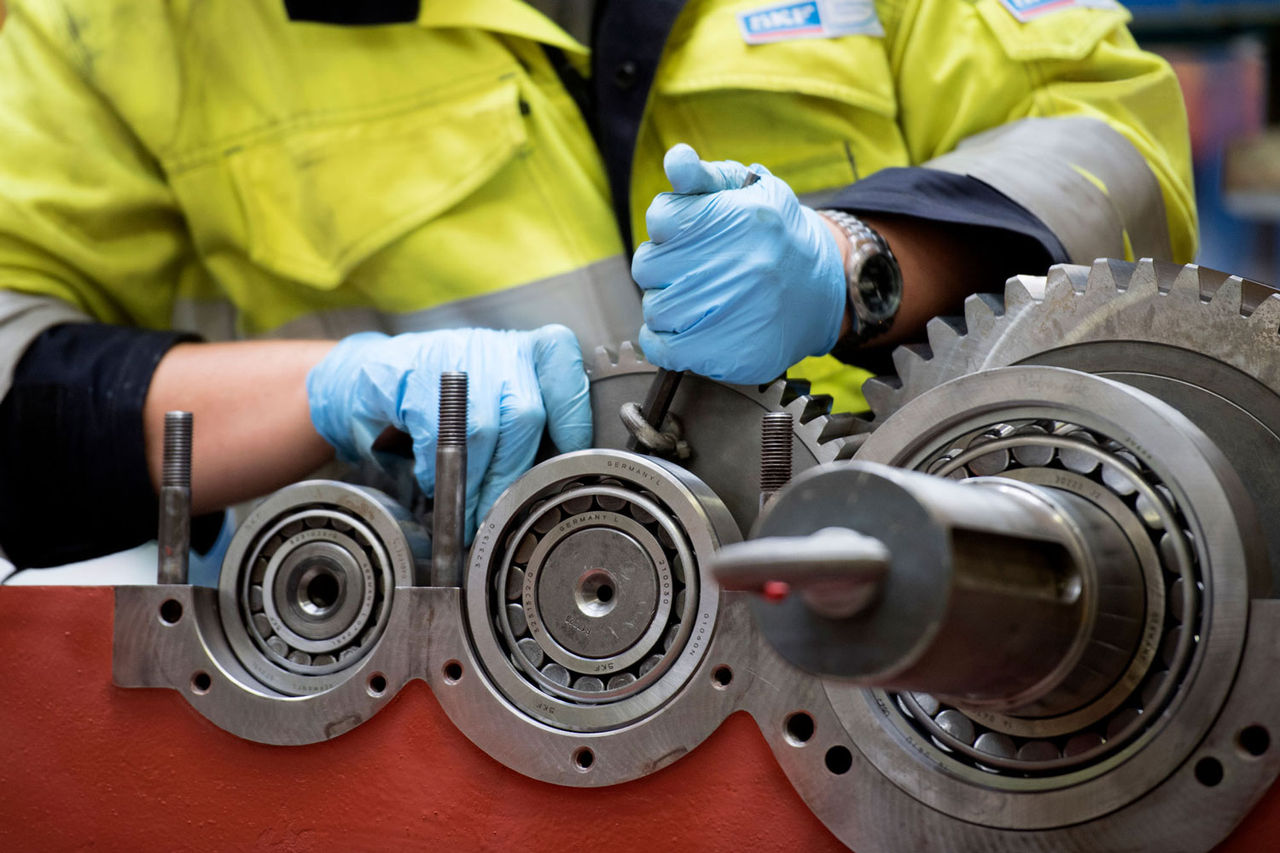
Delivering confidence through consistency
A key objective of the SKF Maintenance Partner model is to reduce variation in maintenance standards across customer sites. By aligning methods, components and tools, the aim is to deliver consistent, high-quality service regardless of location.
This consistency relies on shared expectations. ERIKS follows SKF procedures not just in repairs, but in areas such as measurement, traceability and training. Customers benefit from knowing that whether they speak to a service centre in Aberdeen or an engineer in Bristol, they can expect the same level of care, expertise and insight.
Why this matters to manufacturers
Industrial businesses today face complex pressures. Skilled labour shortages, rising operating costs and the drive to extend asset life all add strain to maintenance teams. In this context, the value of a fully qualified, fully aligned support partner becomes even more apparent.
Working with ERIKS as an SKF Maintenance Partner gives manufacturers direct access to:
- Repairs completed using genuine SKF components
- Faster access to technical support and product advice
- Engineering teams with up-to-date SKF training
- Workshops that meet independently audited standards
- Insights that help reduce downtime and improve reliability over time
This approach can also support broader maintenance strategy, helping customers move from reactive to predictive maintenance and align their activity with sustainability and efficiency goals.
A platform for future collaboration
The SKF Maintenance Partner programme continues to evolve. ERIKS is working closely with SKF to expand service capability, deepen customer insight and explore new joint initiatives that extend value beyond component supply.
This includes extending condition monitoring services, providing more advanced diagnostics and integrating support across digital platforms. It also opens opportunities for co-developed maintenance plans and improvement programmes tailored to specific industries.
For ERIKS, becoming the first SKF Maintenance Partner in the UK and Ireland reflects the investment made over many years in skills, infrastructure and standards. It also sets a platform for continued growth, shared development and deeper customer partnerships.
It confirms a shared belief that industrial maintenance should be smart, consistent and based on trusted relationships.
And it means that when customers see ERIKS sporting the SKF Maintenance Partner mark, they know exactly what it stands for.
For more information about SKF & ERIKS Partnership, contact your local ERIKS Service Centre, who will be happy to discuss your options.
#SKF #ERIKS #LetsMakeIndustryWorkBetter #MaintenancePartner