In this article
Closing the Skills Gap with Confidence
Manufacturers and industrial sites are under pressure. Ageing assets, leaner teams and tighter budgets mean maintenance departments are being asked to do deliver increased up-time with with less resource year-on-year. That is where ERIKS and SKF are making a difference. As SKF’s first Maintenance Partner in the UK and Ireland, ERIKS provides access to the tools, techniques and technical expertise that manufacturers struggle to maintain in-house.
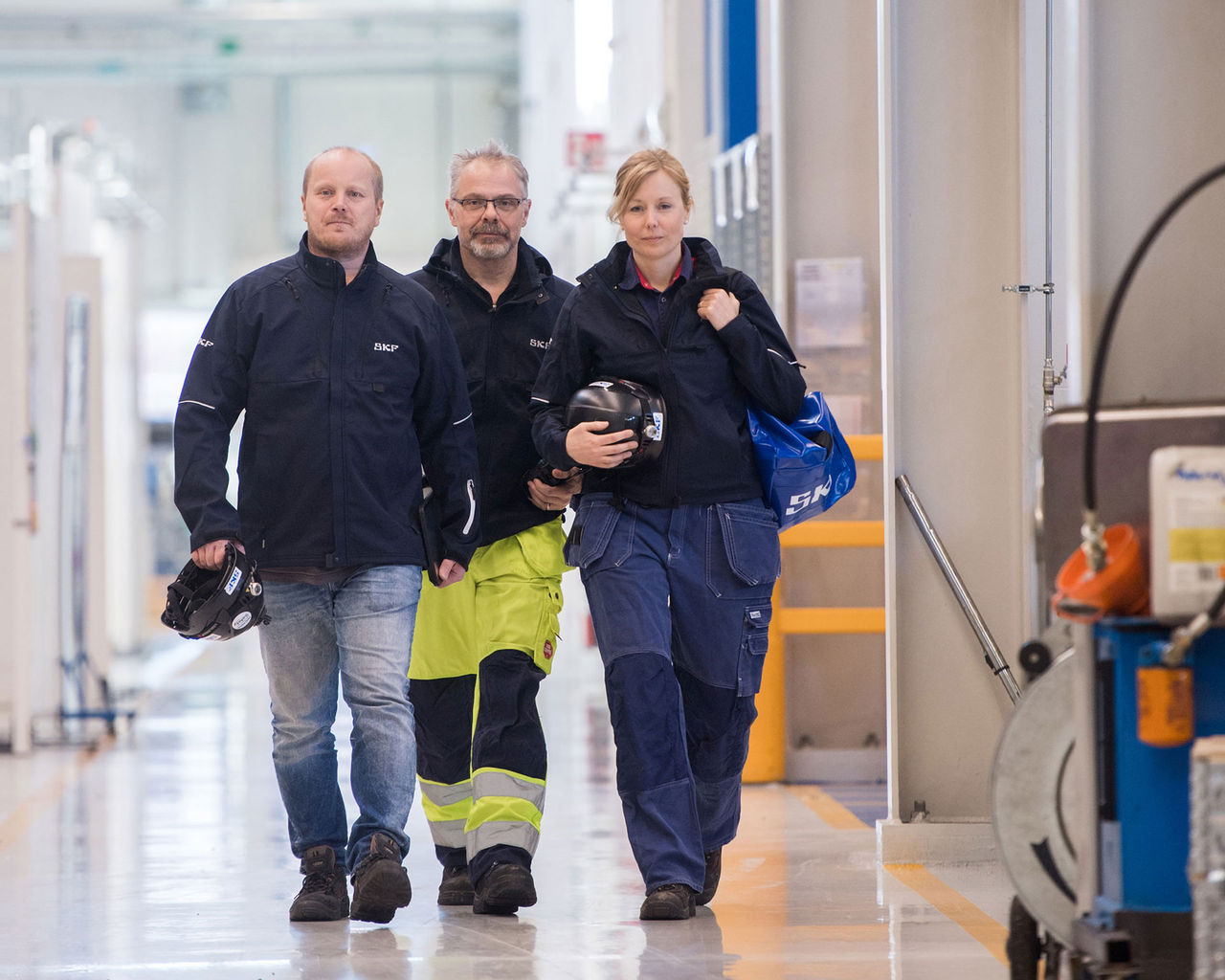
The skills gap is real. Many companies are facing shortages of experienced maintenance engineers, and the knowledge required now covers a broader range than ever before. Working with ERIKS and SKF is not just a way to fill that gap, but to future-proof your approach to maintenance, with services that are standardised, certified and scalable and engineers that are experienced.
Getting it right the first time
When a fault is flagged by condition monitoring or a repair is due, there is often a scramble to find the right skills and tools to act on it. With ERIKS and SKF, those resources are ready to go. From basic alignment and bearing installation to full removal, repair and recommissioning, the joint offer is built on doing things properly.
Tasks like bearing fitting or seal replacement might be simple, but in practice, they require precision. Bearings need to be mounted with the correct preload, seals must be installed without damage, and tools must be used in line with SKF best practice. That is where ERIKS’ maintenance engineers excel. They have been trained using SKF tools and methods, and their work is backed by a maintenance partner certification process that covers everything from job execution to final sign-off.
It is a level of assurance that cannot always be guaranteed with general contractors or non-specialised providers.
More than repair
ERIKS and SKF work together to support customers with a wide range of mechanical and diagnostic services. These include:
- Alignment, mounting and dismounting of rotating equipment
- Asset inspections based on condition, damage and conformance
- Root cause analysis to determine why equipment failed
- On-site measurement and calibration using SKF standards
Whether supporting a new project installation or responding to a sudden breakdown at an existing site, ERIKS can draw on SKF’s best practice, product knowledge and global network.
And because ERIKS engineers are part of the SKF-approved network, customers can be confident that repairs and interventions will follow consistent standards.
Bearing remanufacturing: a sustainable option
One of the lesser-known services offered through ERIKS and SKF is bearing remanufacture. When large, expensive bearings wear down or fail, the typical response is to replace them. But if the bearing still has enough usable material, SKF can fully remanufacture it to its original specification, complete with testing and a full warranty.
This process starts with an inspection, supported by ERIKS, to assess the bearing’s condition. If suitable, it is sent to SKF’s specialist facility in Austria, where it is disassembled, cleaned, tested and re-machined as needed. This can include crack detection, regrinding and component replacement. The result is a bearing that performs like new, often at 60 to 70 percent of the cost.
Crucially, this approach also supports circular economy thinking. By reusing raw materials and reducing the need for new steel, it offers both environmental and logistical benefits. In many cases, remanufactured bearings are also available more quickly than new ones, helping to reduce downtime and build in supply chain resilience.
Instrument calibration and confidence in data
Accurate data starts with accurate tools. ERIKS supports the calibration of SKF condition monitoring equipment such as Microlog devices. This ensures that vibration, temperature and other readings are reliable, allowing operations teams to act on real-time insights with confidence.
While not a headline-making service, calibration is essential to maintaining the integrity of any predictive maintenance programme. With ERIKS managing this process, customers can be sure that their condition monitoring investment continues to deliver value over time.
Backed by experience, built for the future
The strength of the ERIKS and SKF partnership lies in its depth. Beyond the skills of individual engineers, there is an entire infrastructure in place. This includes:
- Engineers trained to SKF standards
- Access to SKF’s global application and product specialists
- Use of approved tools, processes and diagnostic techniques
- A fast track to SKF factory support where required
In effect, working with ERIKS gives manufacturers a direct line into the full SKF ecosystem. Whether solving persistent reliability issues, planning equipment upgrades, or simply getting
more life from ageing assets, the combination of ERIKS’ field presence and SKF’s engineering excellence offers a practical route forward.
A smarter way to close the gap
Ultimately, this partnership is about delivering results. Maintenance standards rise. Unplanned downtime falls. And manufacturers gain the reassurance that critical work is being handled by people who know what good looks like.
At a time when skills are in short supply and the demands on plant teams continue to grow, ERIKS and SKF are offering more than a service. They are offering certainty.
For more information about SKF & ERIKS Partnership, contact your local ERIKS Service Centre, who will be happy to discuss your options.
#SKF #ERIKS #LetsMakeIndustryWorkBetter #MaintenancePartner #SkillsGap #Engineering