In this article
Why online monitoring has a new fan
Keeping a close eye on your assets is essential to optimum efficiency, cost-effective maintenance, and avoidance of catastrophic failure. But what if the asset is 30m up in the air? Then you don’t need a ladder, you need a platform: the ERIKS Smart Asset Management platform.
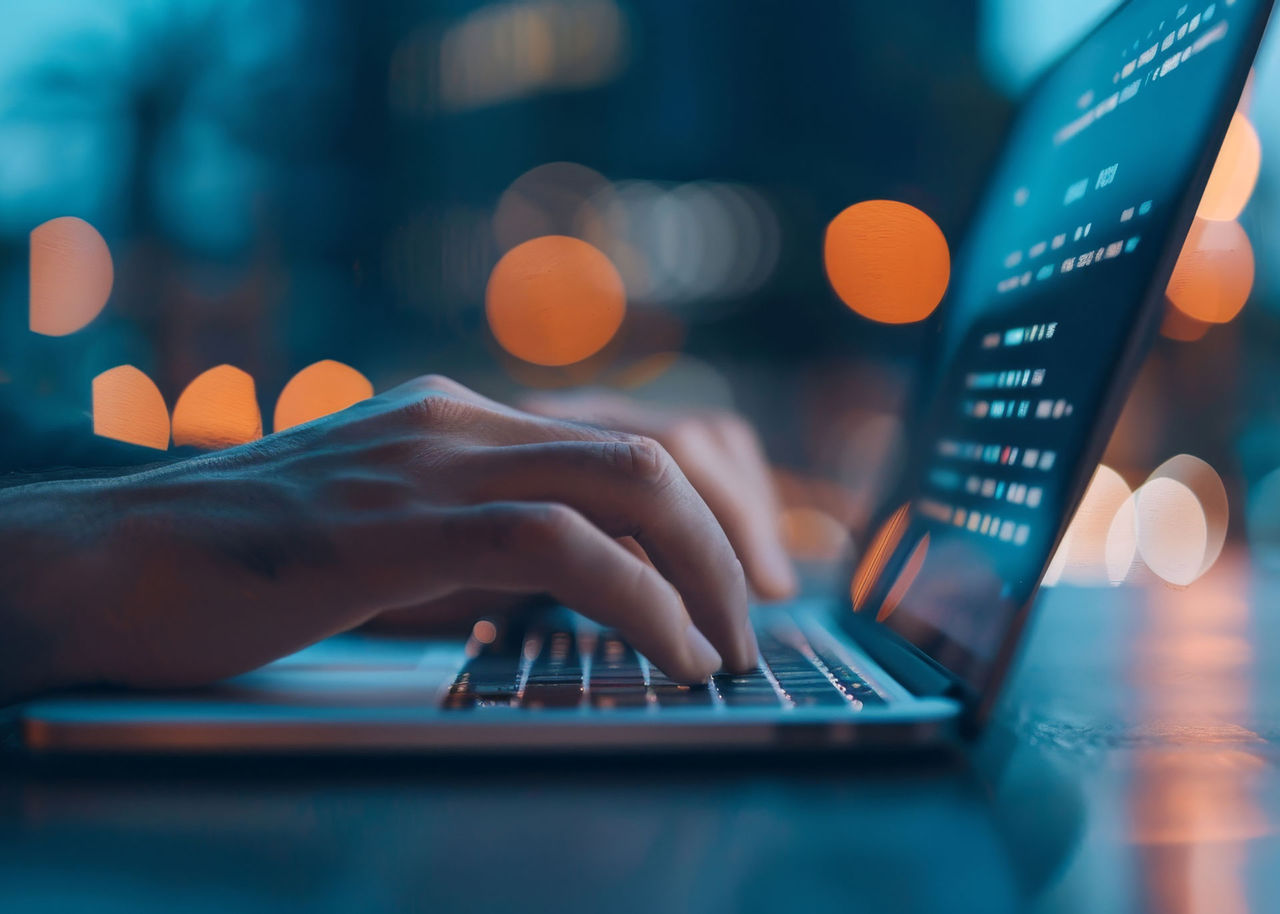
A customer had been relying on portable monitors for intermittent monitoring of a fan motor, which is vertically mounted 30m up a chimney. The motor powers an extractor fan, which removes polluting fibreglass fragments from waste gases before they are dispersed via a chimney. If the motor fails and the fan stops working, the pollutants have the potential to contaminate a nearby beauty spot and major waterway.
The motor non-drive end bearing had already failed three times in the previous 18 months, due to undetected deterioration. And there was always the risk of an issue arising in-between monitoring visits.
ERIKS Smart Asset Management platform (SAM) made maintaining the asset a much more down-to-earth task.
Completely baffled
The main indicator of a problem with the fan and motor was excessive noise. This had reached such a level that the customer was considering baffling the fan with an acoustic cabinet. Clearly this was treating the symptom rather than the cause.
ERIKS had a better solution. By using wire-free sensors connected to the ERIKS SAM platform, the customer could continually monitor the motor without requiring access.
When the customer agreed to a trial installation, the sensors were expertly positioned by ERIKS’ engineers to collect a one-second burst of data every two minutes, across three different axes. Using the platform to analyse the data not only provided early warning of potential failure, but also revealed the source of the problem.
Accelerated solution
Analysis of the data collected by the sensor showed that while the motor’s acceleration was increasing significantly over time, the fan’s velocity was not. This suggested an issue with the bearings, which on-site technicians diagnosed as inner and outer race faults.
The repair would involve removing the motor, which required a crane to be hired-in. Replacing the motor immediately would reduce the crane hire costs, but the customer lacked a spare.
Having identified insulated bearings as a potential solution to the recurring failures, ERIKS approached the motor manufacturer for a suitably insulated replacement motor. However there was no suitable motor available from stock, and the manufacturer quoted a hugely extended delivery lead time for making the changes required.
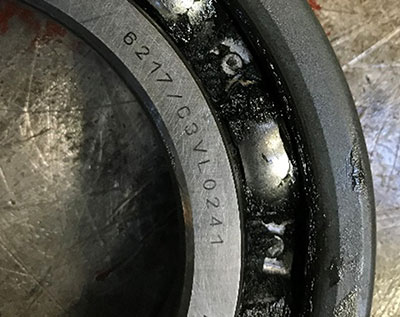
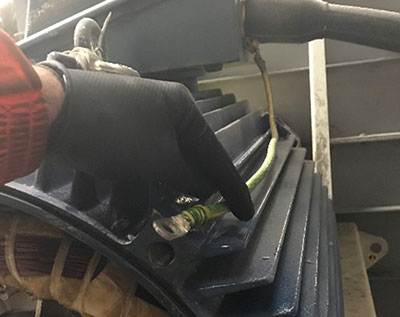
Improve, investigate, innovate
ERIKS’ response was to supply the motor direct, with all the necessary changes: insulating the bearings, adding shorting rings and future-proofing by making it ‘inverter ready.’ Even with the extra work, it was still delivered faster than the original manufacturer could offer.
This allowed the failing motor to be lifted out and replaced with the updated version, which shortened the crane hire period and reduced the cost. The failing motor and bearings were then forensically examined back at the ERIKS workshop.
The inspection showed that bearing failure was imminent. Evidence of electrical fluting also proved that simply swapping-out the old motor with a like-for-like replacement would have left the root cause unresolved.
However, with the data from the SAM platform highlighting the potential issue, the modifications made to the replacement motor were effective at eliminating the problem.
With new bearings installed, and the same modifications made as on the replacement, the updated asset was returned to the customer as a spare.
Fail to plan, plan to fail
Research has shown that unplanned maintenance – often performed under time pressure – is a six times greater safety risk than planned maintenance. And obviously, the unplanned downtime also negatively affects productivity.
By installing sensors for ongoing monitoring, and using the SAM platform for analysis, the customer has greatly reduced the risk of failure. In addition, diagnosing the cause of the excessive noise saved the £45,000 cost of an acoustic cabinet. As a further enhancement, solar-powered sensors have now been installed, to reduce energy costs and shrink the customer’s carbon footprint.
Which all proves that the ERIKS SAM platform is something you can build on, for more sustainable production.
For more information on Smart Asset Management, contact your local ERIKS Service Centre, who will be happy to discuss your options.
#ERIKS #LetsMakeIndustryWorkBetter #ConditionMonitoring #SmartAssetManagement