In this article
Keeping the river on stream - Condition Monitoring benefits the Steel Industry
Of all the things you can think of that might bring steel production to a halt, lack of water probably wouldn’t be the first. But without sufficient water, steelmaking would have to stop. That’s why a major UK steel producer relies on numerous pumps to extract river water and fill reservoirs feeding its production sites. And why pump condition monitoring is so essential to keeping the business’s head above water.
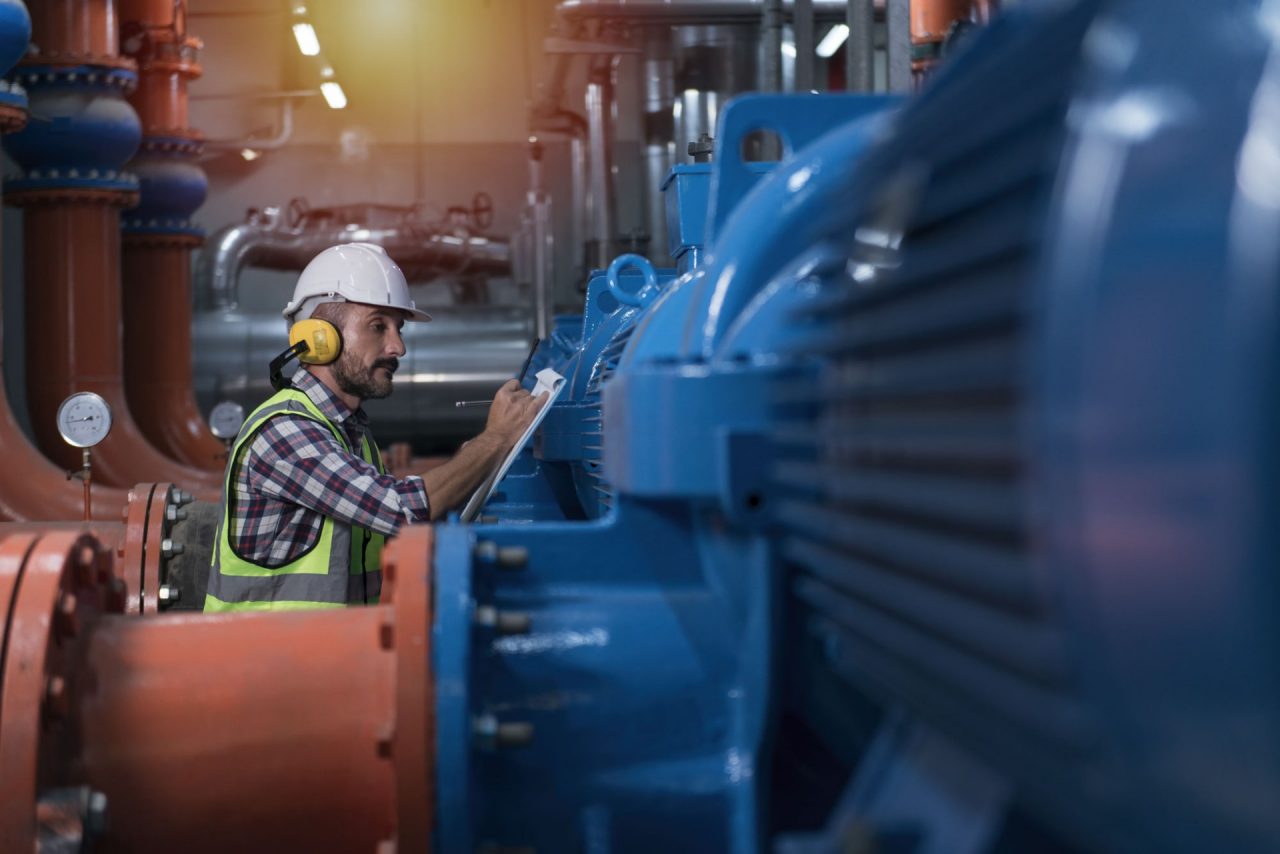
One of the major steel production sites extracts its process water supplies from a tidal river. Water can only be extracted at high tide, which varies in duration from two to six hours depending on the phase of the moon. The water is pumped from the river into storage reservoirs, then drawn down in variable quantities and at varying times to meet the demands of production.
Given the varying duration of the extraction window, and the unpredictable water usage, it’s essential the pumps are ready to run at any time, to pump as much water as possible. For this reason the pumping site is equipped with three tidal pumps among the other post reservoir pumps. Normally two are operating and one is on standby, but at key times all three may need to be running. So an effective condition monitoring and predictive maintenance regime is essential.
To assess the benefits of this kind of regime, the customer made an initial purchase for the monitoring of 12 pumps, supported by ERIKS Smart Asset Management.
Fire prevention or fire engine?
Condition monitoring of these particular pumps has complications.
Firstly, there are only small windows of runtime for generation of vibration data. Secondly, those runtime windows can be at any time, so an engineer won’t always be on hand to carry out monitoring. (In fact the customer had been managing to monitor only a third of the operational running times.) And thirdly, by the time sufficient data has been collected and interpreted, it may be too late and pump failure could be imminent or have already occurred.
So would you rather have information to help you prevent a fire, or be promised a fire engine will arrive quickly once the fire’s burning? Would you rather be warned you’re at risk of a heart attack, or be told you’re having one?
That’s the difference between traditional and ERIKS’ condition monitoring. ERIKS’ solution makes monitoring more effective, and data more timely and usable.
Sensing trouble
The pumping station was chosen for a trial of wire-free vibration sensors. Mounted on the station’s pumps, the sensors gather vibration data periodically – usually every two minutes. This provides comparative data from when the pumps are operating and when they are not, making it possible to identify any induced vibration issues.
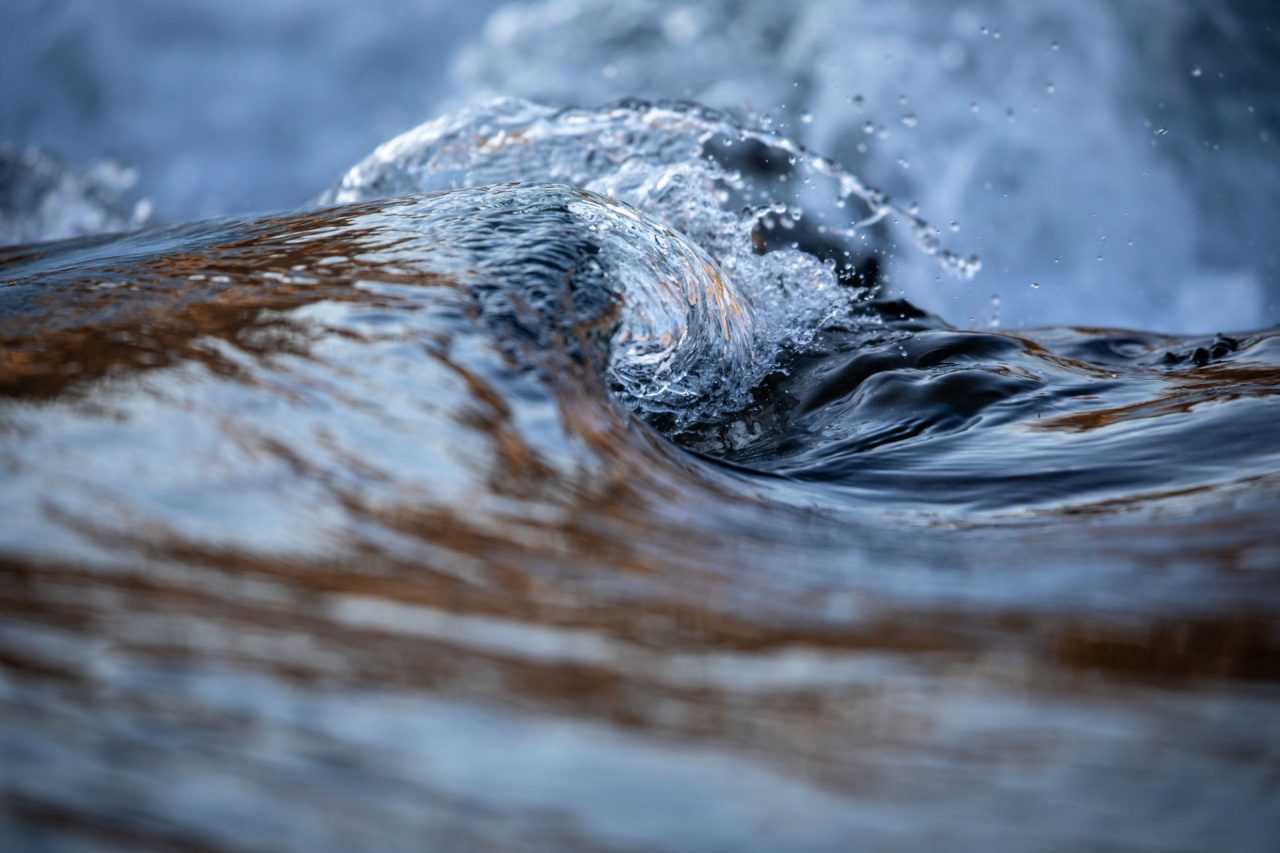
The results were almost immediate – and dramatic.
Both ERIKS’ monitoring and the customers’ own engineers identified a problem with an
in-service pump. So before it could fail completely, it was swapped-out for a recently repaired replacement.
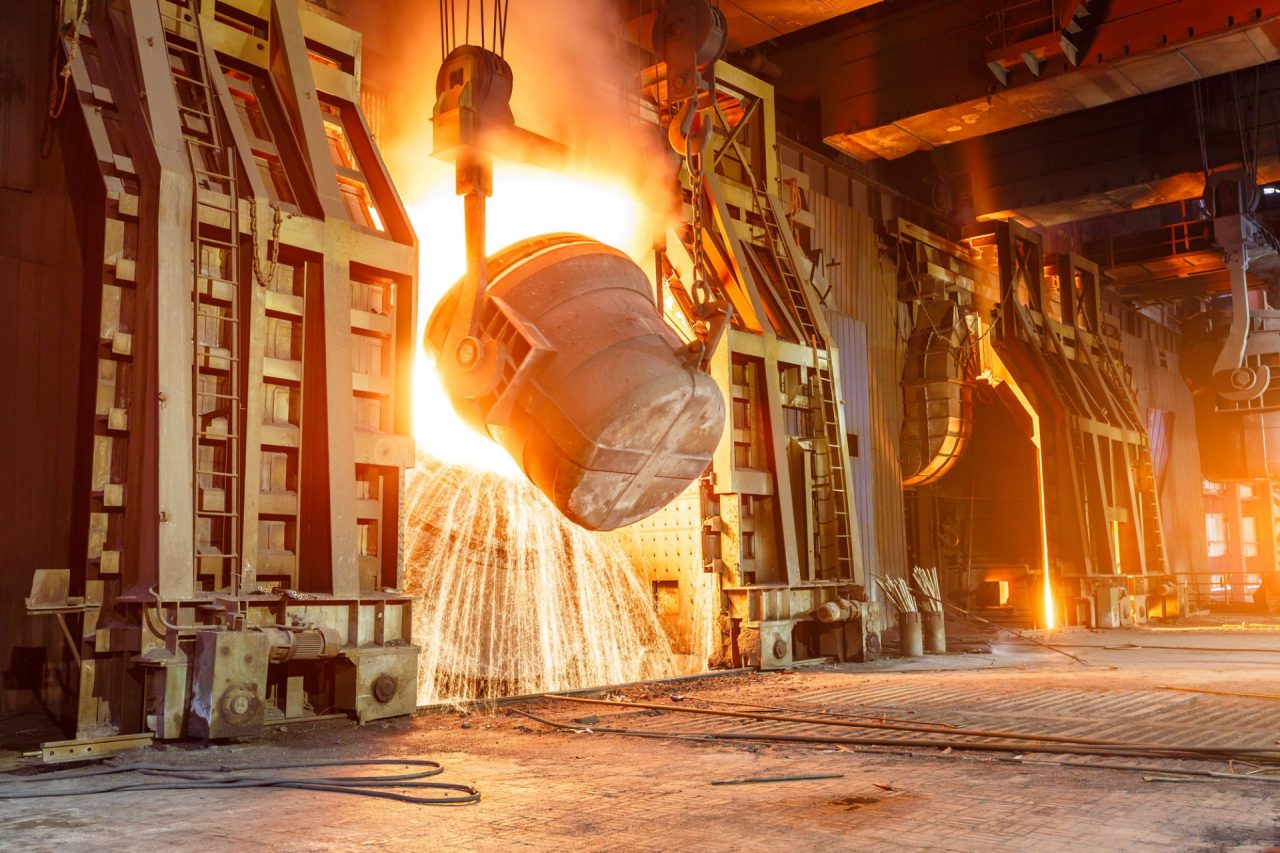
Data v. Information
It’s not only wire-free sensors and opportunistic monitoring – during the smallest runtime widows – which make the ERIKS condition monitoring solution so effective.
It’s also the way the data generated is used.
Traditional condition monitoring swamps users with too much data, which by its nature can only be taken infrequently – meaning it can often be delivered too late. It’s the ‘you’re having a heart attack’ scenario. ERIKS’ condition monitoring, on the other hand, identifies and monitors key failure-mode variables. These provide less dense data, but more useful, data, which can be taken more often and delivered with greater timeliness.
This is only possible because of ERIKS’ comprehensive reliability services, combining decades of repair and monitoring experience. ERIKS know what trends, variables and deviations lead to failures. And ERIKS Digital build this know-how into the algorithms powering the ERIKS Smart Asset Management dashboard, and driving the alert notifications.
So ERIKS condition monitoring doesn’t just give you data. It gives you information you can act on.
Now the steel producer is rolling-out more systems to more pumping stations, and considering them for monitoring ancillary equipment for the main turbines at their production facilities.
Starting from just a handful of water pumps, the success of ERIKS’ online condition monitoring and Smart Asset Management has really opened the floodgates.
Get in touch
If you want to talk to one of our Condition Montoring Team members, contact your local ERIKS Service Centre, who will be happy to discuss your options. In the meantime, have a look at your Online Vibration Monitoring updated info...
#ERIKS #LetsMakeIndustryWorkBetter #Engineering #ConditionMonitoring