In this article
Make washdowns less of a drain on your finances
Frequent wash-downs are a common feature in many aggressive industrial environments. A necessary evil, if you like. Necessary because they remove whatever contamination is present. Evil because they also strip away lubrication from bearings. So how do you make them less of a drain on your finances?
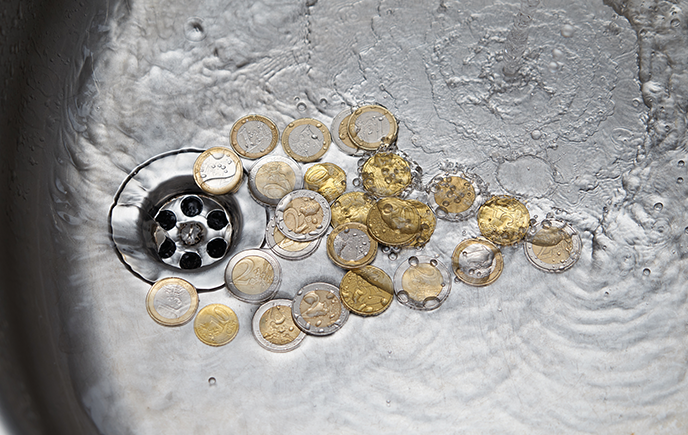
One solution is to completely encapsulate the bearings in standard grease. The more there is in the first place, the longer it will take to wash away. Even so, it will need relubricating eventually – and in the meantime large quantities of grease will have been washed away: potentially to contaminate the environment.
Alternatively, instead of relubricating you could change your lubricant completely. But not after every wash-down.
Simply change it once, from a lubricant that can't resist frequent or caustic wash-downs, to one that's water-, oxidation- and high temperature-resistant. In other words, change it to a PFPE grease like one from the ROCOL range.
PFPEs stay in place during wash-downs
Perfluoropolyethers – or PFPEs for short – are highly inert. When they’re used as the basis for a grease, the resulting lubricant is resistant to all the things that cause other types of lubricants to fail. (When the situation is reversed and it’s the conventional greases that are too aggressive for a delicate environment, then the inertness of PFPEs means they’re ideal here too.)
PFPEs also stay in place during wash-downs. Which means less relubrication, less lubricant consumption, and less potential environmental contamination. There’s another advantage PFPE greases have over conventional lubricants.
Lubricate a bearing with conventional grease and you’ll need to fill around a third of the bearing for effective lubrication. With a PFPE grease, you’ll only need to fill around a fifth. So not only do you use less lubricant, but there’s also less to wash away into the environment.
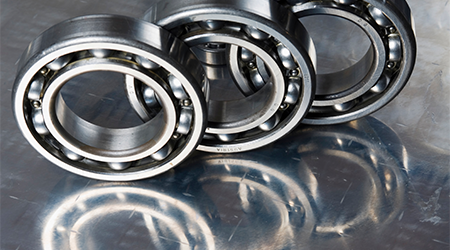
Just a smear of PFPE grease is enough
With some PFPE greases, even just a smear of lubricant around the inner and outer bearing race is enough. If you are used to applying grease in much larger quantities this is a big change, but a big saving too. And if the only lubrication method possible for your application is via a grease nipple, a ROCOL PFPE grease is perfectly suitable for that too.
As you’ve probably guessed, there’s a premium to pay for choosing a PFPE grease. But there’s a price to pay for not using it.
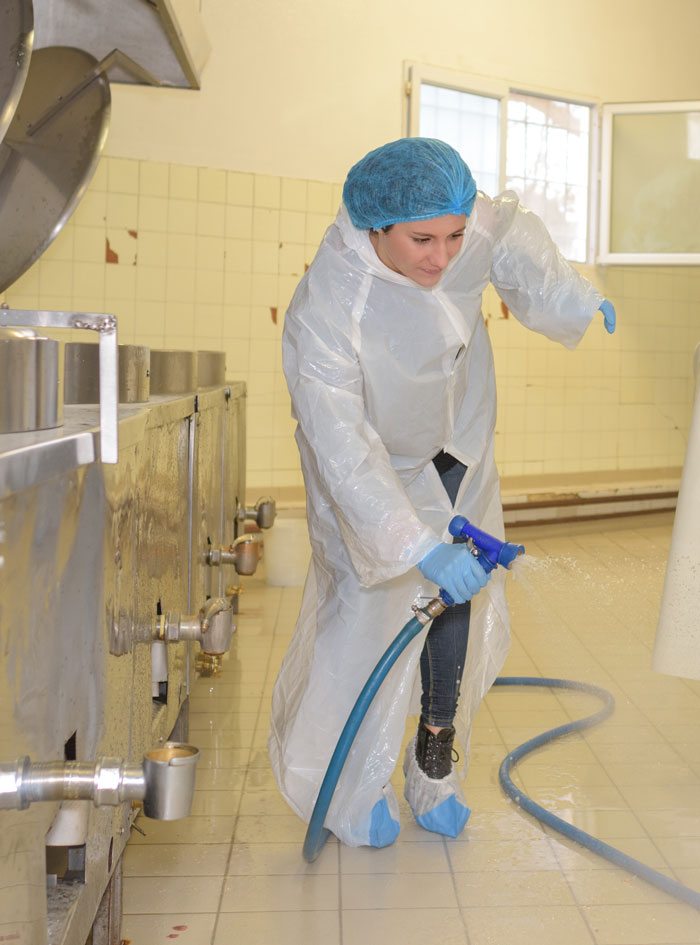
When wash-downs or a water-based environment drive out grease, or very high operating temperatures melt grease away, relubrication is essential and frequent.
But they can only happen when you are aware of the problem. If loss of lubricant isn’t spotted in time, bearing failure can occur before relubrication can take place.
With PFPE lubricants, on the other hand, the grease stays in place, the bearing wears normally over its normal service life, and maintenance can be planned.
Since bearings are often in critical components, and often hard to access, a bearing failure can lead to a lengthy shutdown for repair or replacement. Which means loss of production on top of the costs of resolving the bearing issue.
Reduce lubrication failure and improve performance
Since bearings are often in critical components, and often hard to access, a bearing failure can lead to a lengthy shutdown for repair or replacement. Which means loss of production on top of the costs of resolving the bearing issue.
This kind of application failure is one of the biggest costs for a manufacturer. One of the leading causes is the failure of a bearing. And 70% of bearing failures are due to lubrication errors – most of them related to over-lubrication. So a lubricant that can be sparingly applied, with predictable performance, starts to make even more financial sense.
Lower lubricant consumption. No critical failures. No lengthy unplanned shutdowns. Fewer repair costs. Less lost production. And less money down the drain.
Case Study: The bitter taste of fried bearings
A major manufacturer’s fryer application contains 15 bearings, which were lubricated with standard bearing grease. Bearing failures were occurring every three weeks.
- Cost of each bearing: £82.56
- Replacement: up to two hours each bearing
- Total cost of bearing replacement: £63,158.40 p.a.
ROCOL recommended SAPPHIRE® Endure PFPE grease and – because the high-performance characteristics of the grease made it possible – proposed a change to a more cost-effective bearing. The solution resulted in:
- Cost of each bearing reduced to: £16.12
- Labour reduced from 34hr to 12hr p.a.
- Increased OOE due to improved machine efficiency
- Cost savings for bearings alone: approx. £20,367 p.a.
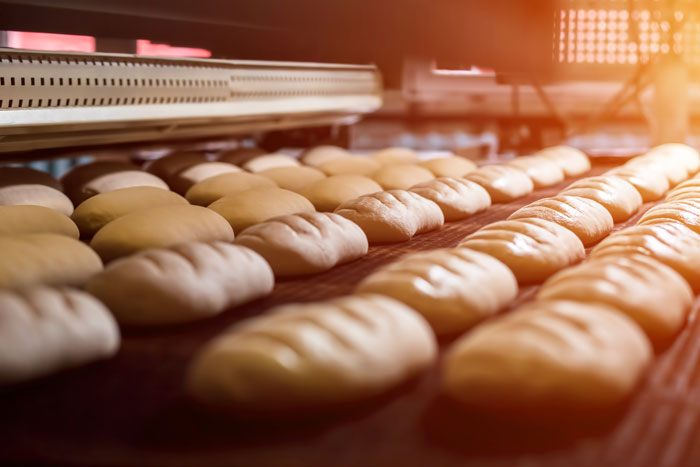
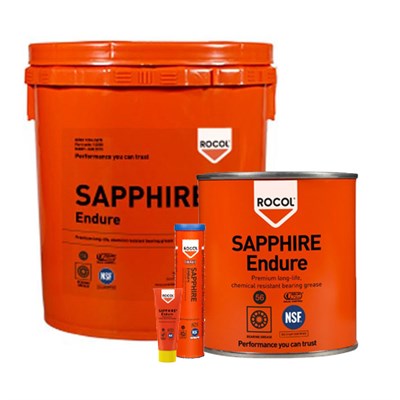
For more information on Bearing & Lubrication solutions and to get in touch with one of our ERIKS Bearings Specialists or Lubrication Engineers, please contact your local ERIKS Service Centre, who will be happy to discuss your options.
#ROCOL #PFPE #Lubrication #BearingGrease #Bakery #FoodandBeverage #LetsMakeIndustryWorkBetter #Productivity