In this article
Topping-up Lubrication
Lubrication literally oils the wheels of productivity. But with the right expertise behind it, it can do far more – as ERIKS and Moove Lubricants proved for a leading manufacturer of plasterboard and other building products.
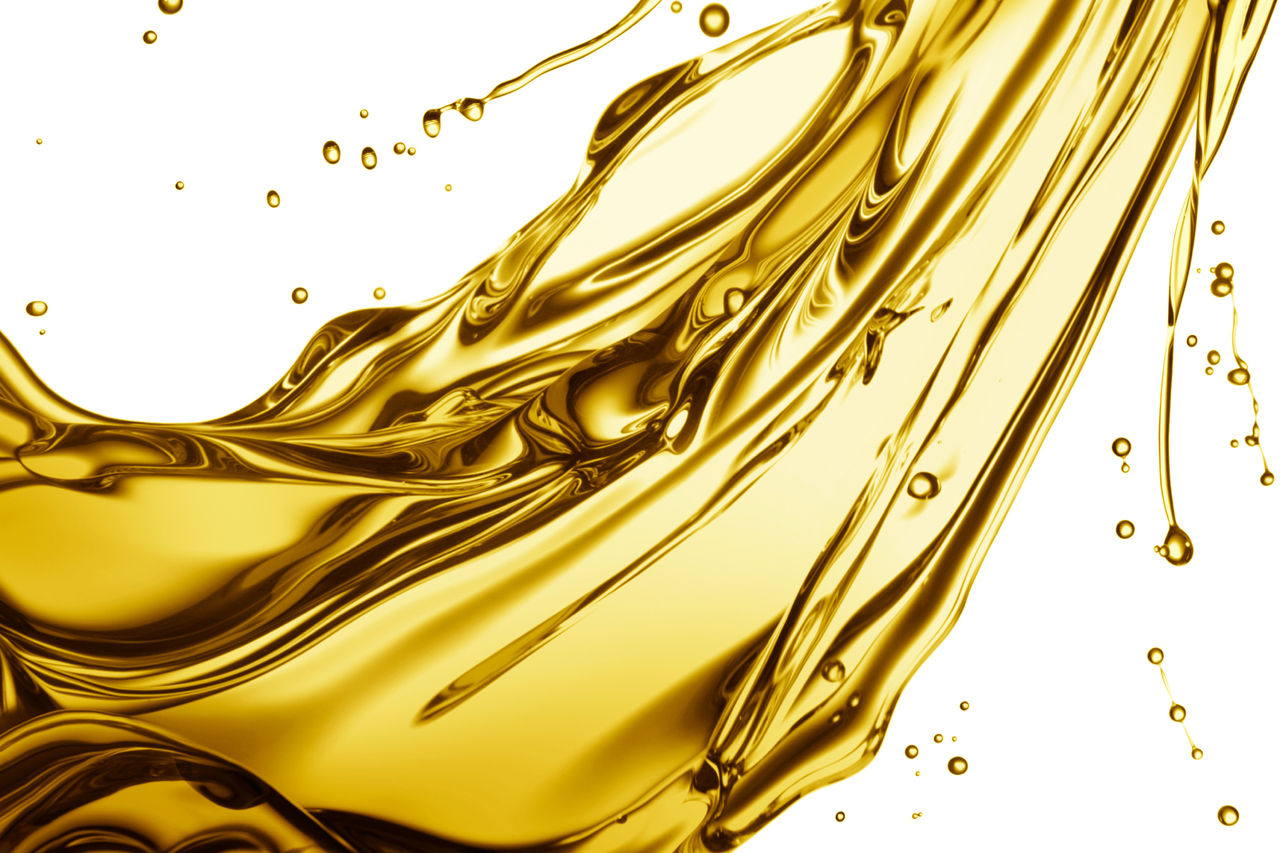
The customer had just replaced two motors due to lubrication-related failures – at a combined cost of £13,000. That was all the encouragement they needed to talk to ERIKS about reassessing their lubrication products and practices.
So ERIKS called in the experts, and Moove made the next move.
Oil can-do
The right lubricants in the right place at the right time not only help to reduce friction. When Moove assessed the customer’s production facility, they identified potential benefits in productivity, safety, energy efficiency, environmental care, and carbon emissions. And it all began with a Site Baseline Survey carried out by Moove’s lubricant specialists.
This initial survey is essentially an expert’s-eye view of a customer’s plant. Moove’s experts conduct a walk-around, talk to relevant personnel, gather information on, for example unplanned downtime incidents, and make an initial identification of possible lubricant-related improvements.
It’s a taster of the unique Moove Engineering Benefit Proposal, compiled after a full site survey, which looks closely at a huge range of possible improvements, and identifies the most cost-effective, which will deliver the greatest benefits to the customer.
Depending on the size of the customer’s site, and the number of assets present, this full site survey can take between a few days, to a few weeks.
Naturally it will consider whether the right lubricants are being used for the right assets. Whether there are upgrades available to enhance performance or increase reliability. It will include thermal imaging, to identify if assets are running too hot. There may also be a recommendation for further in-depth inspections, such as root cause failure analysis, and borescopic inspections.
And Moove’s experts will even take a close look at the oil stores, to assess if lubricants are being stored and handled correctly.
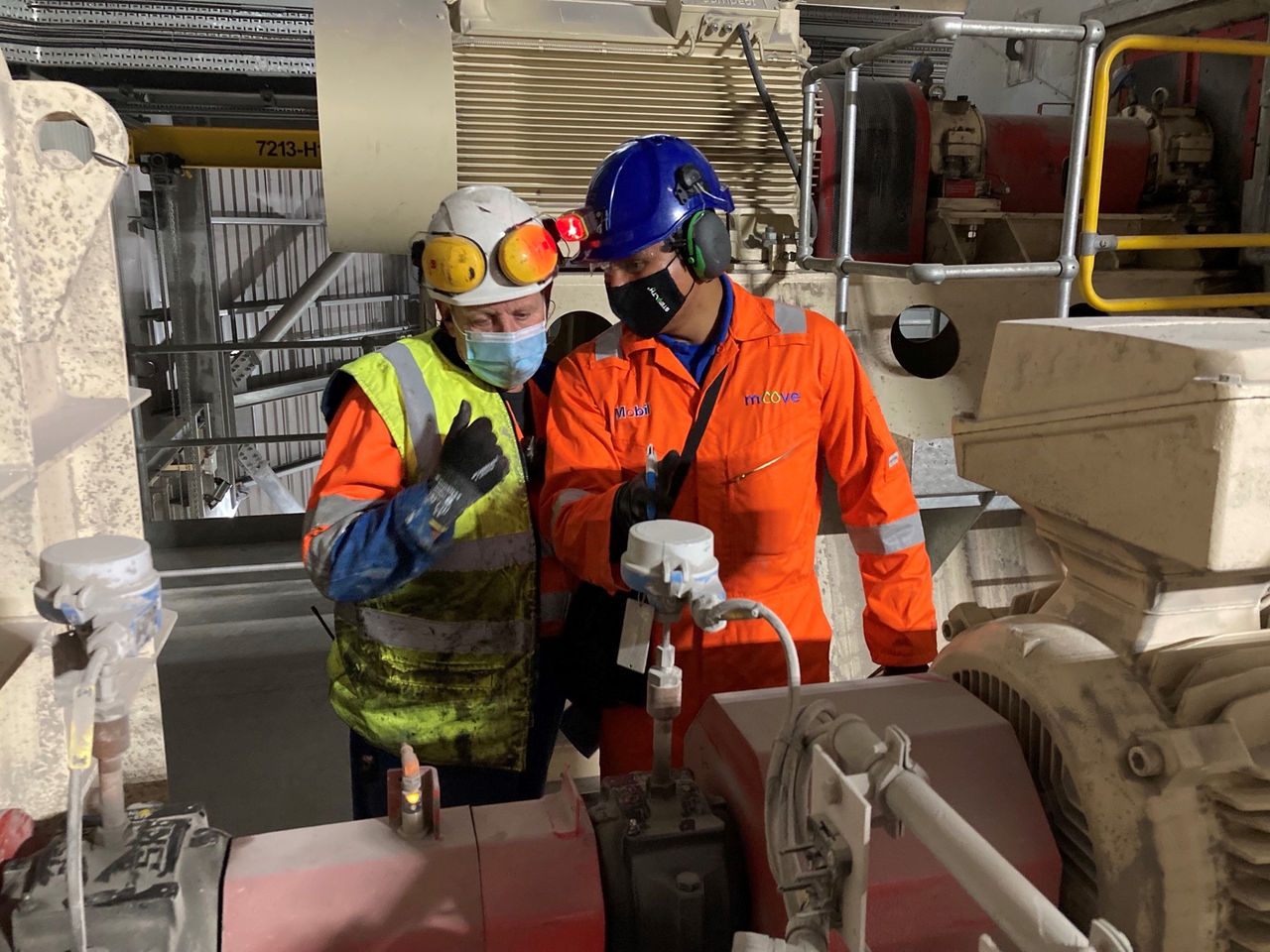
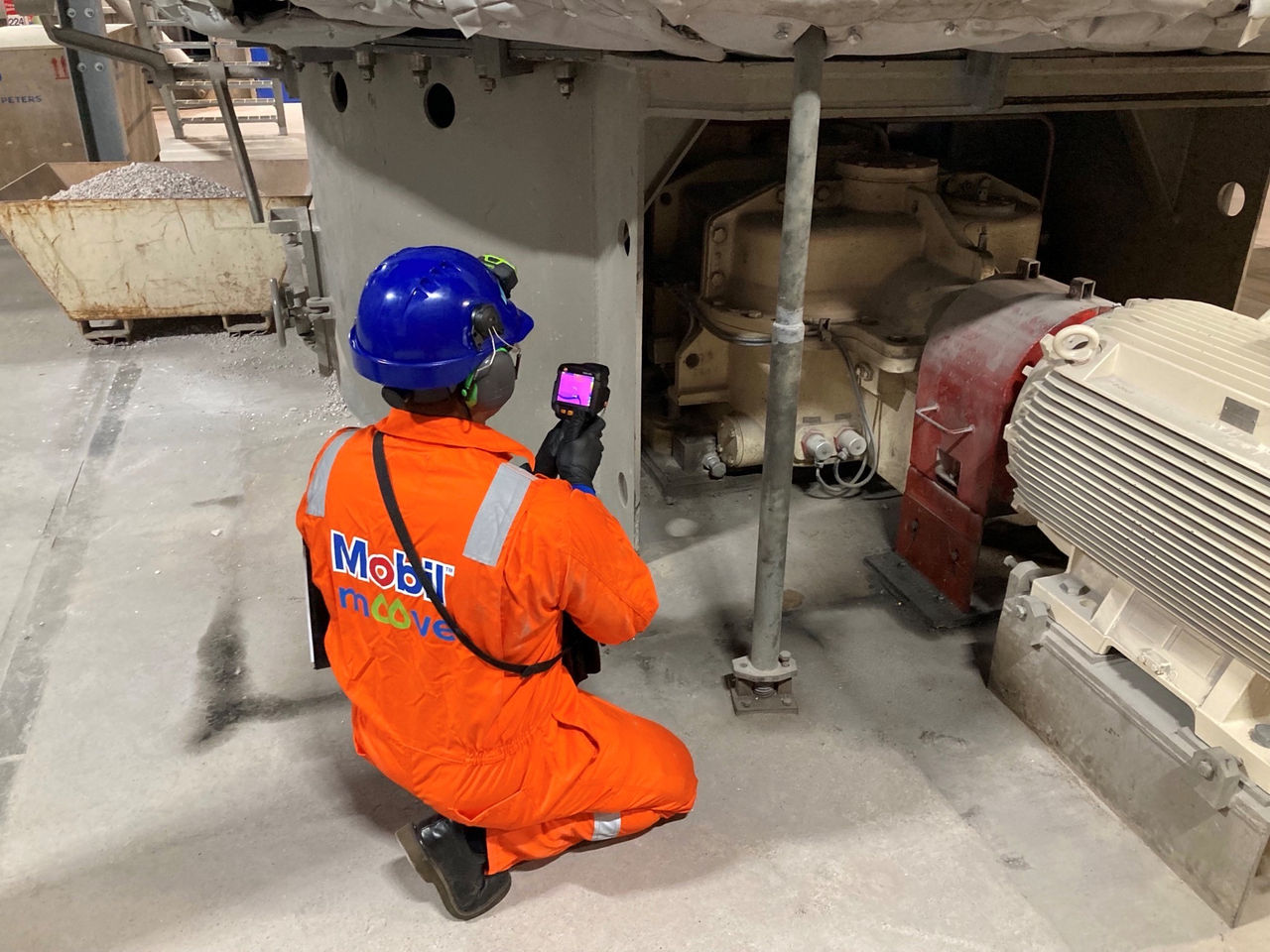
Theory into practice
For experienced lubricant specialists, identifying lubrication issues is relatively simple. Proposing cost-effective solutions is more challenging but can be an integral part of the service from Moove.
Depending on the size of the customer’s plant and other factors, Moove’s support can extend from the Site Baseline Survey which usually brings about a Site Evaluation Report, to their unique Engineering Benefit Proposal and, ultimately, the Implementation Plan, which are the final stages that follow the full site survey.
The Implementation Plan covers not only the identification of individual asset failure modes – and the selection of the most effective lubricants to help prevent them – but also optimum storage practices and handling techniques, and the most efficient lubrication schedule for maximum reliability, efficiency and productivity
Building on expertise
For the manufacturer of building products, the Moove Lubricants’ survey identified the customer’s Table Mill gearbox as the asset with the potential for the greatest improvement in cost savings and carbon reduction. The survey highlighted a range of potential benefits which could be realised by a change of lubricants:
- Productivity - Changing to Mobil energy-efficiency lubricants would improve revenue by an estimated £8927 per annum.
- Energy - Resulting savings in energy efficiency would amount to £2,185 over the same period
- Safety - By reducing the amount of unscheduled downtime and consequent repairs and maintenance, there would be a reduction of 5.1 hours per annum in engineers’ exposure to safety risks
- Environmental - The reduction in oil consumption as a result of upgrading the lubricants would result in a parallel reduction in waste oil requiring disposal, of 800 litres per annum
- Carbon footprint - Lower lubricant consumption would lead to an annual reduction in carbon dioxide emissions of 10.9 tonnes.
As most synthetic oils have a service life of five years, the customer was also shown the potential cumulative 5-year savings of adhering to Moove’s recommendations. These would be a direct result of longer oil drain intervals, lower traction coefficients, and improved wear protection leading to enhanced reliability. The headline savings included:
- Productivity - £44,635
- CO2 – 54.5 tonnes
- Waste oil – 4,000 litres
If this kind of survey – and these kind of savings – could benefit your site, a call to your usual ERIKS contact will start the wheels moving. Just like a well-chosen lubricant.
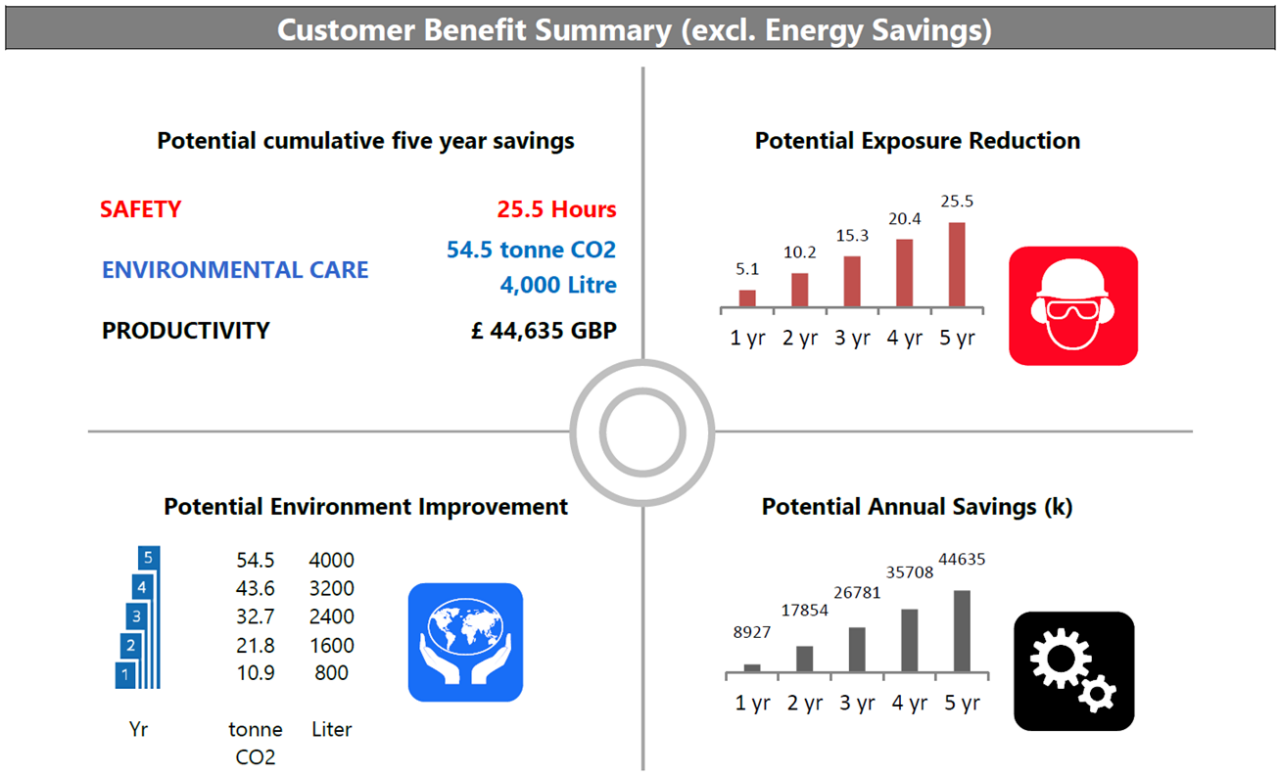
For more information on Lubrication solutions and to get in touch with one of our ERIKS Specialists, please contact your local ERIKS Service Centre, who will be happy to discuss your options.
#MooveLubricants #ERIKS #LetsMakeIndustryWorkBetter #Lubrication #Specialism #SiteSurvey