In this article
Protecting your bearing investment
Large industrial bearings are a significant capital investment. So it’s essential to maximise their performance. These five Best Practice tips from Timken will help you do just that – while increasing your plant’s uptime, and without breaking the bank.
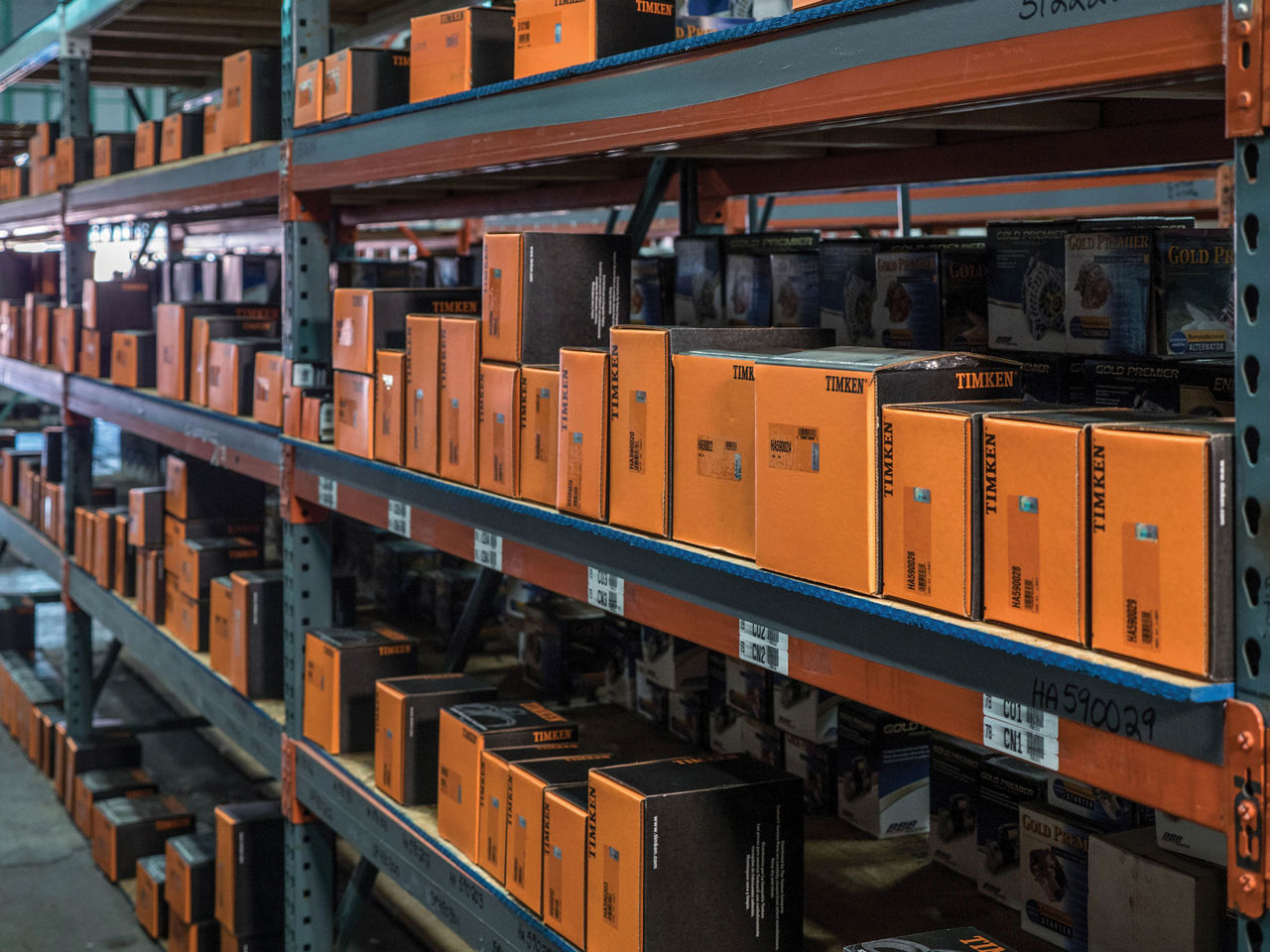
1 – Select the right bearings
Bearing selection depends on the application, and mechanical and environmental factors.
Each roller element type (ball, needle, cylindrical, spherical or tapered), has design-specific characteristics for load, speed, stiffness or allowable deflection, lubrication requirements, static and dynamic misalignment, and desired service life or durability.
Bearings cope with a broad range of speeds and many combinations of radial and axial loads, but environmental operating conditions (temperature, dust, dirt, moisture, unusual mounting conditions) can affect performance.
Bearing envelope size constraints – such as minimum shaft diameter, maximum housing bore and available width in the bearing application – will also affect the bearing choice.
Several bearings with different load-carrying capacities may fit in the envelope. However, which of these will deliver the desired predicted service life can be identified through a bearing-system-life analysis carried out by the bearing manufacturer.
The final step is to define the bearing design options and select the most appropriate. The options are cage type, bearing flange configurations (for cylindrical and tapered roller bearings), radial internal clearance (RIC) or setting, precision level and lubrication.
Selected based on the application’s speed, temperature, mounting and loading conditions, correct choices will help optimise bearing performance and life.
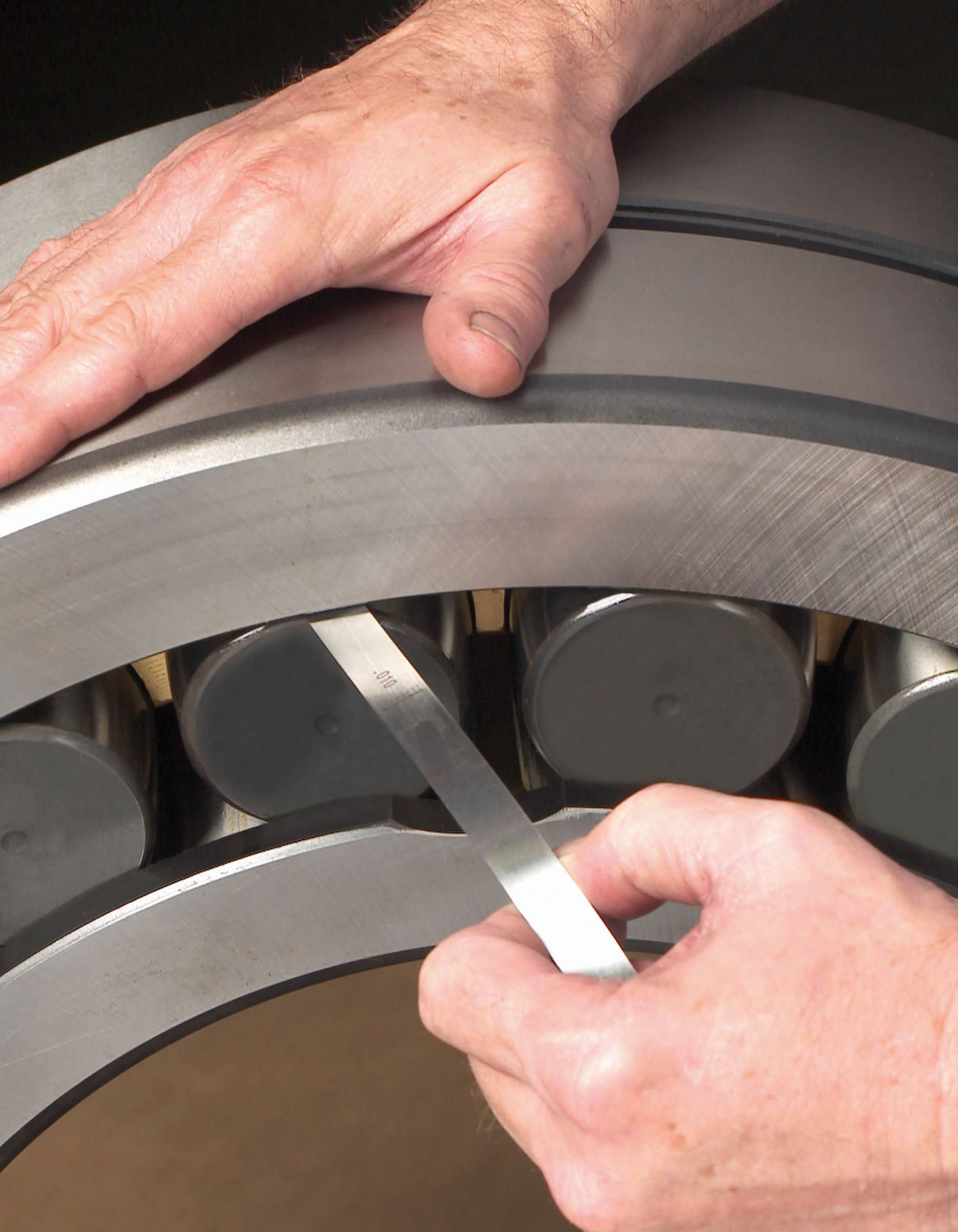
2 – Follow proper handling practices
How bearings are stored, removed, cleaned, inspected and installed will vary by bearing type. However, general good practice includes:
- Storage: In original packaging on a pallet or shelf until ready for use. Even small amounts of moisture can initiate bearing fatigue, so avoid high humidity or widely variable temperature environments where condensation may form.
- Handling: Avoid bearing damage during removal and installation, through use of the correct tools. Pullers and installation tools are available for smaller bearings, while larger bearings require slings, hooks, chains and mechanical devices. The right tools will also help prevent costly or irreparable bearing deformation.
- Cleaning: After removal and before inspection, bearings (including all internal rolling elements) should be thoroughly cleaned to remove water, lubricant, debris and other contaminants. Always follow the manufacturer’s cleaning recommendations.
- Inspection: Damage and wear inspection should also include measuring the bearing, to ensure it is within the application’s tolerance specifications. In some applications, expected bearing life may be the limiting factor in the equipment maintenance schedule. Routine inspection and measurement will reveal problems and enable correction before they lead to equipment downtime.
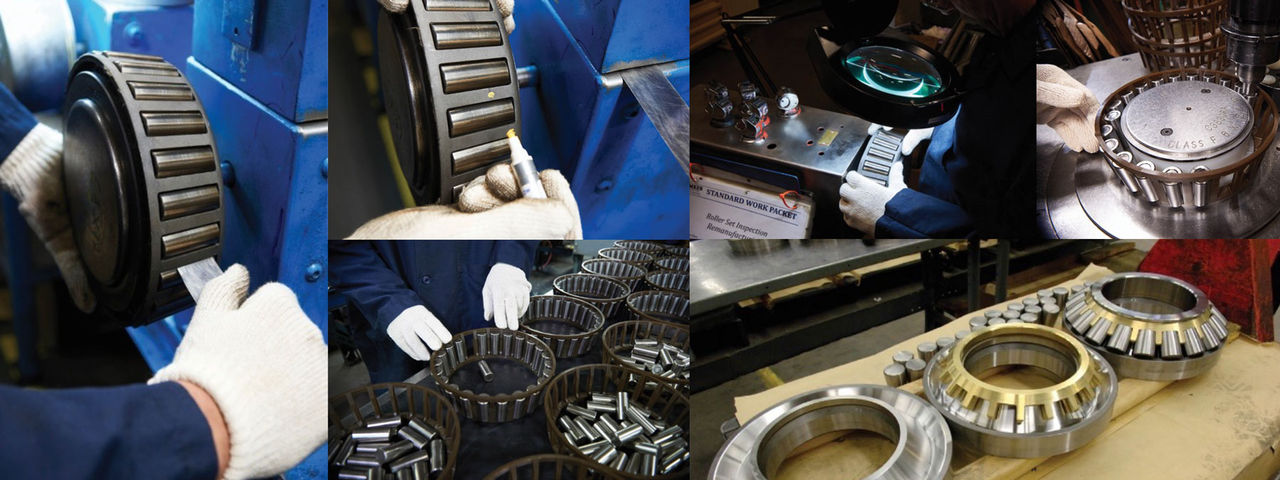
Proper handling practices for storage, removal, cleaning, inspection and installation can all optimise bearing service life.
3 – Optimise your predictive maintenance program
Predictive maintenance can improve uptime by warning of potential problems while the equipment is in operation. Condition monitoring systems can – for example – detect and monitor excessive equipment temperature or vibration, and report them in real-time. Remote Monitoring Services provide continuous predictive monitoring by collecting data, which can be analysed to identify process improvements.
4 – Use proper lubrication practices
Incorrect lubrication is a common reason for shortened bearing life. In a properly lubricated bearing, component mating surfaces create a lubricant film that prevents metal-to-metal contact. The lubricant can also trap debris and carry it away from contact surfaces.
The correct lubricant for each application depends on the bearing design and operating conditions. In general, lubricants are classified as oil or grease, with different benefits.
Lubrication Selection Benefits
Oil
Grease
Carries heat away from the bearings
Simplifies seal design and acts as a sealant
Carries away moisture
Permits prelubrication of sealed or shielded bearings
Easily controlled lubrication
Generally requires frequent lubrication
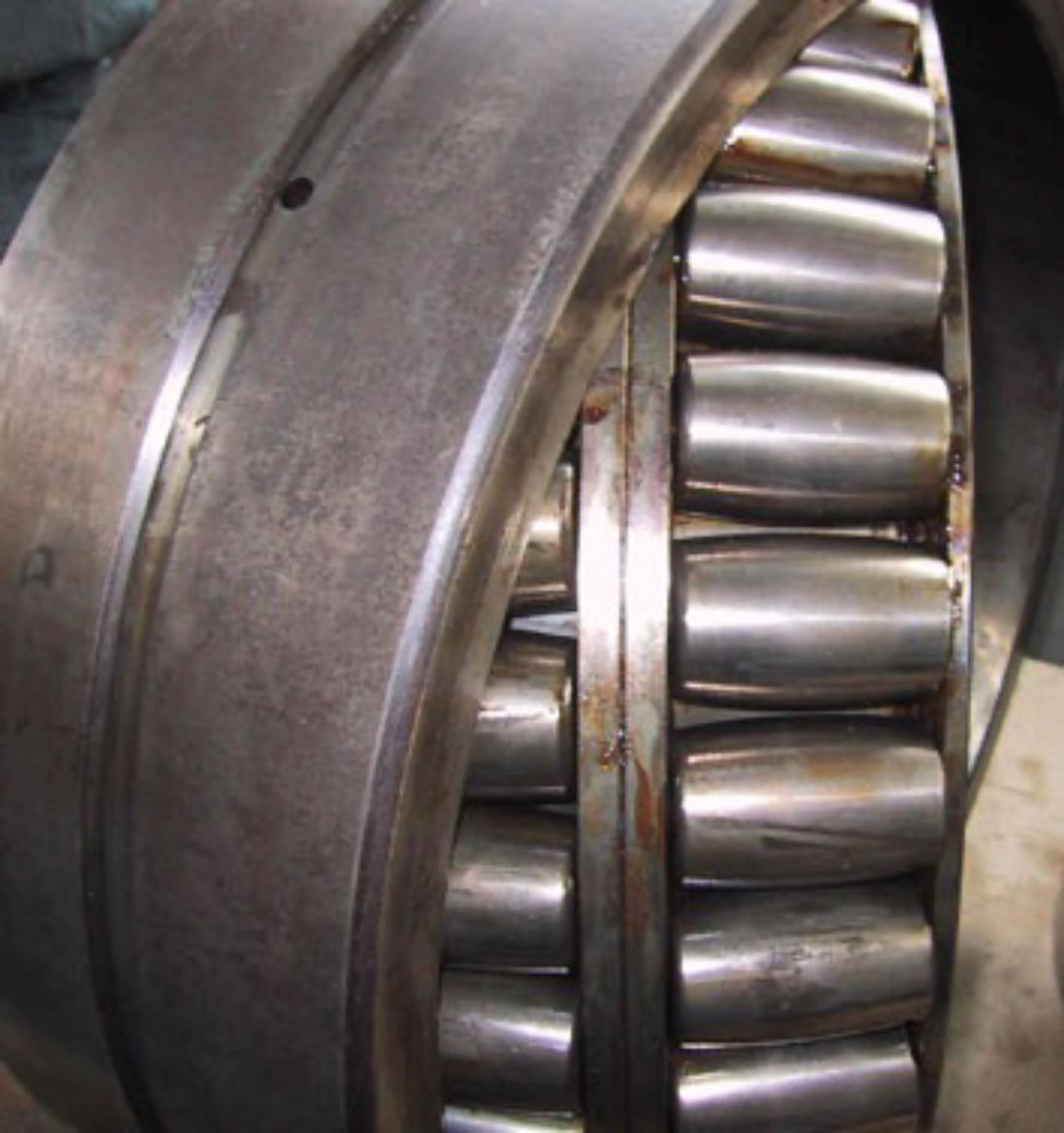
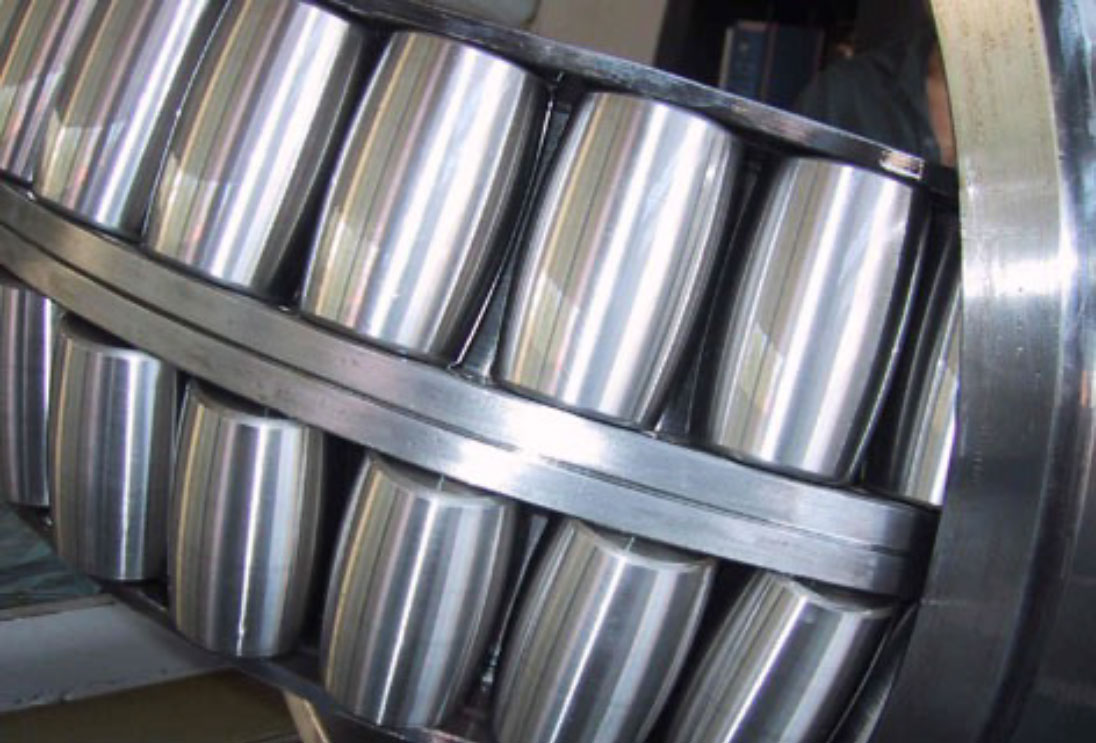
Spherical roller bearing before and after bearing remanufacture.
5 – Repair bearings to extend service life
Damaged or out-of-specification bearings may be returned to service after repair or refurbishment. Some can be refurbished more than once.
Analysis can help identify possible causes of damage, and solutions to help ensure longer life for the replacement bearing. Minor damage can often be repaired on site by maintenance engineers, though remanufacturing services from bearing specialists will be required in cases of more serious damage.
Repair services can save 20-80% of the cost of buying a new replacement bearing, and may take just weeks, compared with a leadtime of months or years for a new bearing. Repair is also more environmentally-friendly – getting many more service hours from the bearing before it needs to be repaired again or finally discarded.
For more information on Bearing Solutions and to get in touch with one of our ERIKS Specialists, please contact your local ERIKS Service Centre, who will be happy to discuss your options.
#Timken #ERIKS #LetsMakeIndustryWorkBetter #Bearings #Lubrication #BestPractice