In this article
NSK show us life under the hygiene regime
Hygiene is the key ingredient in food and beverage manufacturing. Complying with stringent hygiene standards demands frequent thorough washdowns to remove dirt and unwanted grease, often at high pressure with chemical cleaning agents. This can often damage sealing systems – allowing water and cleaning solutions into the bearing cavity, and leading to grease washout, corrosion, and – ultimately – reduced bearing life.
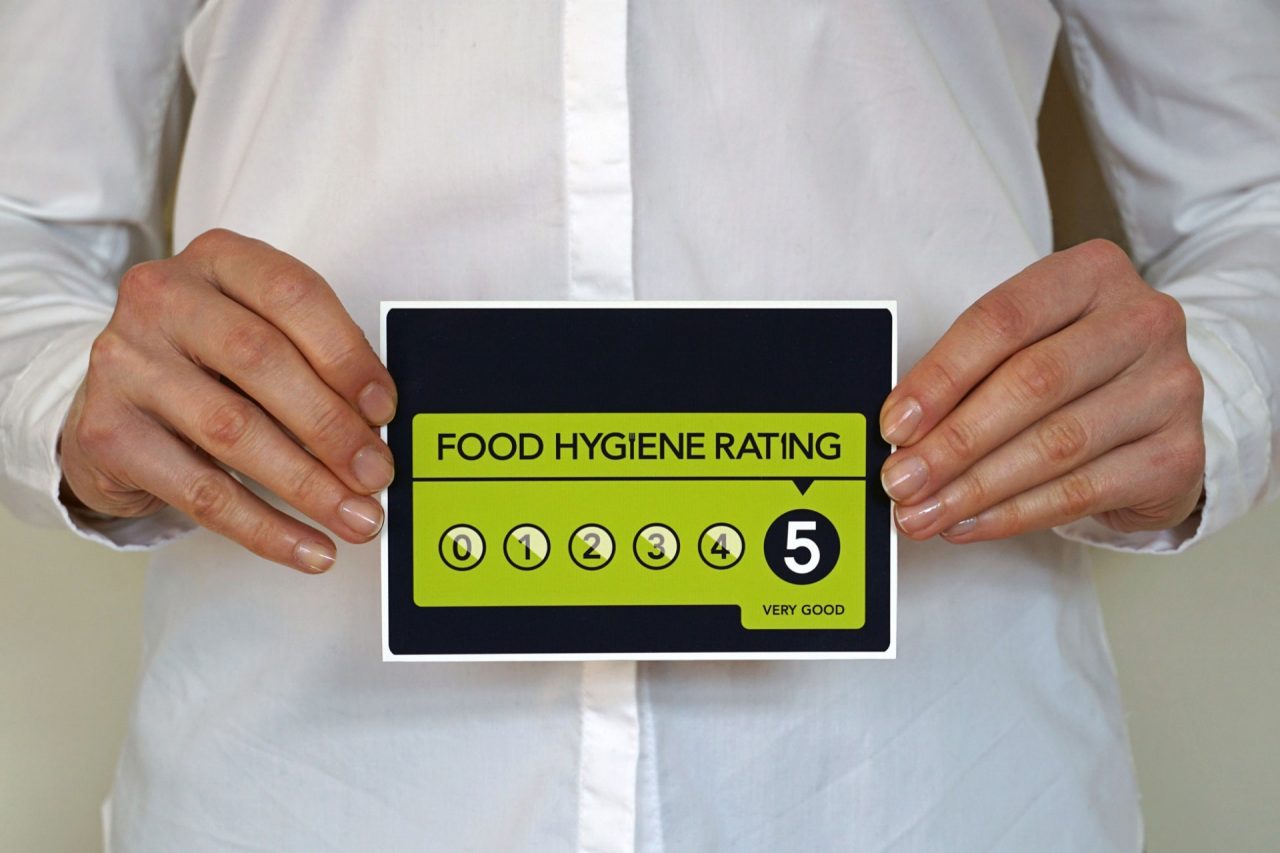
As if life wasn’t tough enough for bearings in those conditions, many primary food preparation stages – washing, peeling, grading, cutting and mixing – require large amounts of water and process fluids. Combine those with routine cleaning cycles and you have one of the worst operating environments for rotating assets. Tests have shown that just 1% by volume water ingress can reduce bearing life to less than 1/10th. The result is frequent bearing failures, unpredictable machine reliability, costly downtime and environmental risks.
A new lease of life
To survive – and thrive – in this kind of operating environment, a bearing needs to function reliably with minimal maintenance. So NSK has developed the RHP Life-Lube® bearing series to do just that.
Life-Lube® housings are made from PBT thermoplastic polyester resin – which is both corrosion-risk free, and resistant to detergents and a wide range of chemicals. The housings’ smooth surface, free from paint and coatings, also helps to make wash-downs more effective, and eliminates any threat of flaking or chipping.
Even the specially moulded-in stainless steel bolt hole reinforcements are designed to minimise the number of places where bacteria may grow.
The bearing insert’s rings, balls, two-piece riveted high-strength metal cage, set screws and flingers are all made from high grade stainless steel, providing superior corrosion resistance.
A high-performance single lip seal in Nitrile rubber is standard, combined with a flinger to deflect water used in cleaning processes, and to protect the seal from damage. Most important of all, the inserts are charged with NSK’s innovative Molded-Oil™ lubrication technology.
Molded-Oil™ is a solid lubricant produced from a proprietary oil-impregnated polymer, which completely fills the bearing cavity. In operation, the carrier matrix slowly releases oil to lubricate the bearing running surfaces, while at the same time acting as a barrier to prevent ingress of contamination such as water and particulates.
The lubricant cannot be washed away to enter other areas of the machine, where it could potentially come into contact with foodstuffs. So the operating environment remains clean.
With no re-lubrication required, Molded-Oil™ inserts are also maintenance free.
Life-Lube® bearings are available in pillow block, two-bolt flange, four-bolt flange and take-up units, giving system designers flexibility, and making it easy to find the optimum solution for any application.
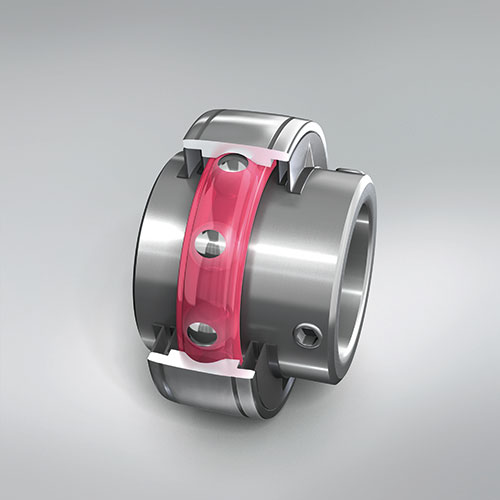
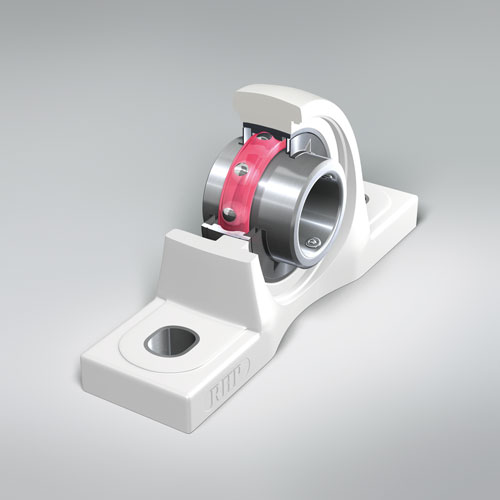
More to life than lubricant
Life-Lube® units have even more to offer than corrosion resistance and long-life lubricant.
For example, the seating’s spherical fit allows for initial misalignment on mounting. While set screw locking enables close-fit shaft mounting. In addition, super-finished raceways provide quiet and efficient running.
The recommended operating range for a Molded-Oil™ insert is -15°C to +80°C (maximum continuous operating temperature: 60°C).
It also has a high maximum allowable speed. Both these qualities make the inserts highly suitable for food industry applications and the high continuous speed of many food plant machines.
Hygiene is a way of life in the food and beverage manufacturing sector. Life-Lube® units from NSK more than live up to the challenge.
A cut above the rest
A major snack food producer was experiencing frequent bearing failures on its cutter line.
As part of its AIP Added Value Programme, NSK conducted a process map survey of the site, analysed the failed bearings and reviewed the application. This revealed extensive grease washout following production line washdowns. Planned six-weekly maintenance included bearing changes, but bearing failure often occurred before maintenance was carried out.
NSK engineers trialled replacing the bearings on one production line with NSK Life-Lube® housed units. After a year, the bearings were still performing well with no failures. This vastly improved bearing lifetime resulted in annual savings of €134,478, from reductions in the costs of maintenance labour, replacement bearings and production downtime. The plant is now installing Life-Lube® units on all its production lines.
For more information on Bearing Solutions and to get in touch with one of our ERIKS Specialists, please contact your local ERIKS Service Centre, who will be happy to discuss your options.
#NSK #ERIKS #LetsMakeIndustryWorkBetter #Bearings #Innovation #Optimisation #Solutions #Food