In this article
When the going gets tough, the bearings get going
It’s okay for us humans. When working conditions get too challenging – if the aircon breaks down, for example – we can insist on working from home. Bearings don’t have that luxury. Extreme temperatures, vibrations, shock loads and contaminants can all be part of their ordinary working day. In conditions like these, you need more than an ordinary bearing.
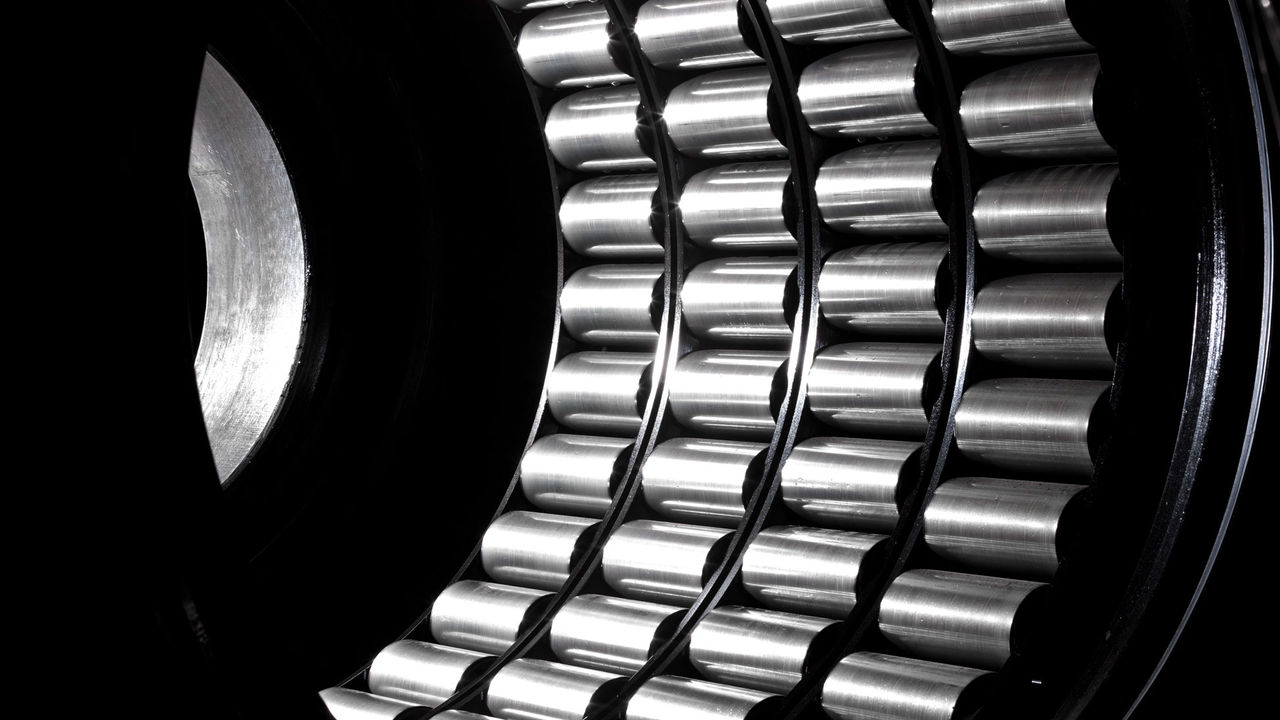
Even in regular industrial settings, bearing failures often lead to lengthy downtime. But some of the toughest environments – such as quarries and mines – where operating conditions for bearings are harshest, also tend to be remote and hard to access. This means sourcing and receiving replacement parts can take longer, and downtime becomes even more of an issue.
Rather than replacing failed bearings over and over again, the solution can lie in making relatively simple changes, that often lead to major improvements.
Cementing success
Conditions in the cement industry are highly challenging for machine components. One customer was seeing bearing failures every two to three months on a blade support for a concrete pipe slotting machine, with each failure leading to around eight hours of downtime.
The failures were mostly due to concrete dust contaminating the grease. When NSK engineers examined the application, they identified that the existing shielded Deep Groove Ball Bearings weren’t suitable for the environment. Their recommendation was to switch to NSK’s Molded Oil bearings, which come with a DDU seal.
Available as ball, spherical roller and tapered roller bearing types, NSK’s Molded-Oil bearings contain a resin holding a supply of lubricant. This is distributed in small, continuous quantities on to the raceway.
The result is bearings which are well adapted for corrosive, watery and dustfilled environments. Their inbuilt continuous supply of lubricant also means they don’t need refilling, so their maintenance-free performance is extended.
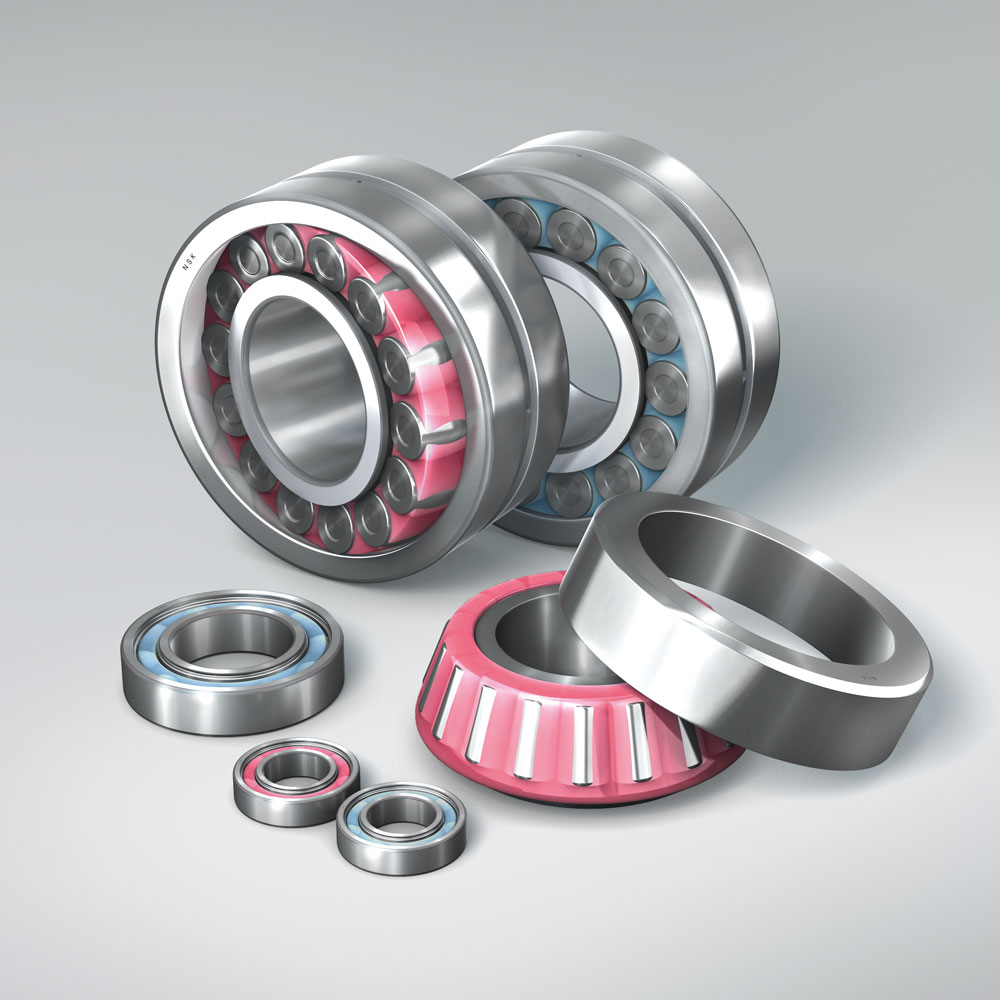
For this customer, the change to Molded Oil more than quadrupled the life expectancy of the bearings – from two to three months to more than a year. Cost-savings for the company were in the region of £33,000 per annum.
Good vibrations
Quarrying and mining environments are tough for workers and even tougher for bearings. While employers naturally take good care of their employees, taking care of their bearings – and making the right bearing choices – is important too. In fact, the impact on productivity and profitability can be huge.
The vibrating screens in one particular quarry were failing every six months, due to bearing faults caused by issues with load, lubrication and contamination. Every failure resulted in 24 hours of production downtime.
Specialist NSK engineers evaluated the situation and recommended a switch to NSK VS Series bearings, made from High-Tough Steel (HTF) which is specifically designed to hold up even under the most severe operating conditions. HTF can be utilised for cylindrical, tapered and spherical roller bearings, and offers up to seven times the service life of conventional bearings when dealing with contaminated lubrication.
Thanks to their superior resistance to wear, seizure and heat, the new bearings had triple the lifetime of their predecessors. This ultimately saved the company around £47,000 per annum, through reductions in both downtime and maintenance costs.
Keep on rolling
Steelmaking is another industry where bearings routinely take a beating. After repeated unexpected bearing failures at a cold rolling mill, a steelmaker contacted NSK for help.
The highly-contaminated operating conditions within the mill were causing costly unplanned shutdowns with a catastrophic effect on production. After analysing the problem, NSK experts recommended adoption of the STF range of spherical roller bearings, made from long-life Super-Tough Steel. These bearings have been specifically developed to combat debris contamination in the lubricant.
Compared to conventional bearings, the NSK STF range offers longer life, and increased resistance to wear, seizure and heat. Service life when dealing with contaminated lubrication can be up to 10 times longer, up to four times longer even at 160°C, and with a 40% improvement in seizure resistance.
Before the switch, the company’s bearings were failing every three or four months. Now they are now being changed out just once a year as part of regularly scheduled maintenance – representing a cost-saving of around £14,000 per annum. Clearly, if you take care of your bearings, your bearings will take care of you.
For more information on Bearing Solutions and to get in touch with one of our ERIKS Specialists, please contact your local ERIKS Service Centre, who will be happy to discuss your options.
#NSK #ERIKS #LetsMakeIndustryWorkBetter #Bearings #Mining #Quarrying