In this article
Why lubrication is worth looking into
Lubrication can do much more than just keep moving parts running smoothly. Used correctly, it can not only improve plant efficiency and reliability but also save energy. The key is to assess how lubricants are currently being used in your plant. Are they the right ones for the application? Are there more appropriate formulations? Or are there ways to use lubricants more effectively, to enhance sustainability and reduce costs? Together, Moove and ERIKS can help you find the answers.
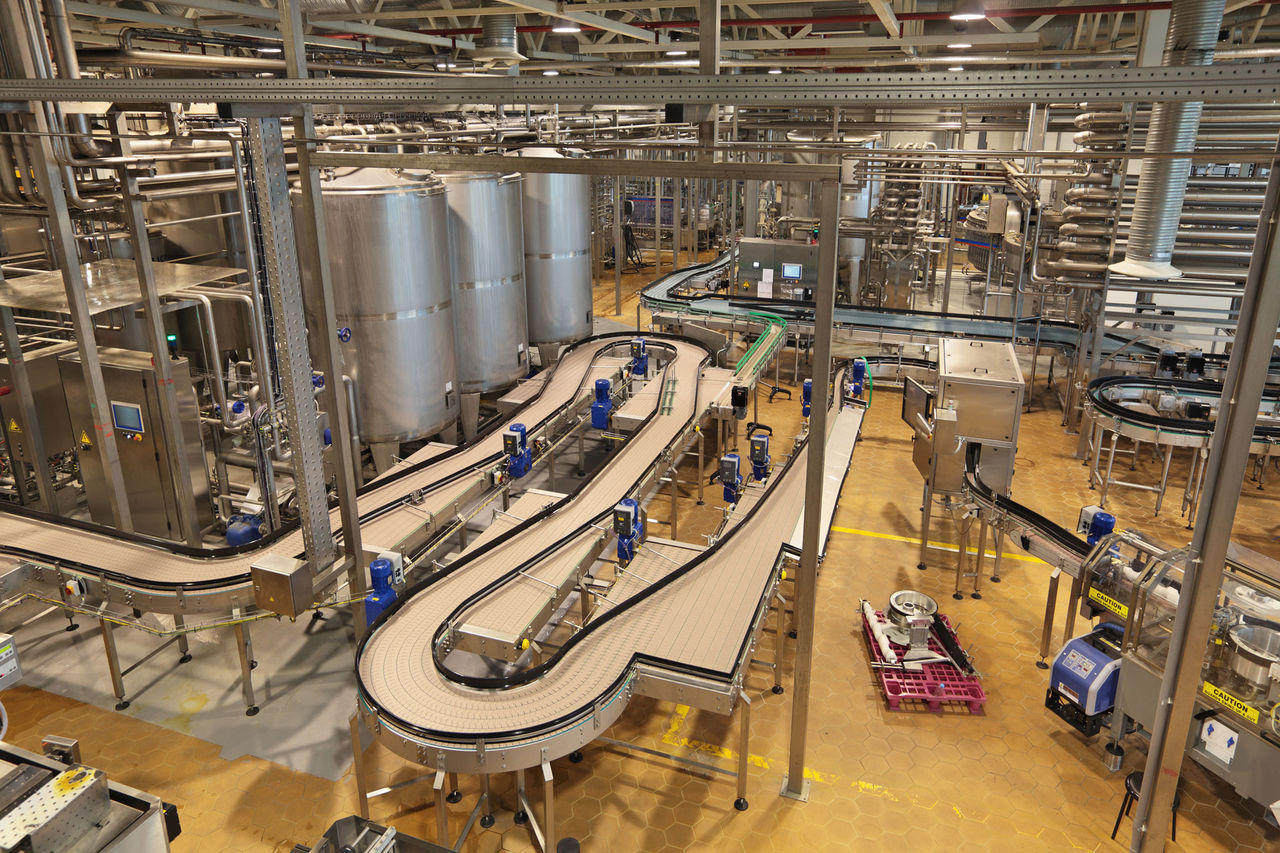
A lubricants survey conducted by Moove and ERIKS is a comprehensive review of lubricants and lubrication practices, to identify what is being done right, and what could be done better. The survey considers a whole range of categories: from lubricant storage and handling to health and safety, and from lubricant selection, analysis and usage to contamination control and training.
Once the results have been gathered and assessed, the survey will identify the steps needed to implement a lubrication programme which will optimise reliability, and deliver increased sustainability and reduced energy use wherever possible.
Storing-up trouble
A recent site evaluation for a manufacturer of cereal-based products delivered an initial site rating of ‘Poor’, due to a number of issues with oil storage, oil handling, and asset lubrication. The survey not only identified the issues, but also proposed solutions which would help the customer to realise lubrication efficiencies and savings in the short- and long-term.
Beginning with the oil stores and waste oil area, the survey revealed that poor signage on the waste oil bin posed a small risk of waste oil being mistakenly used again, with the associated risk of asset contamination and premature failure.
Meanwhile, in the storage area, First In First Out best practice was not being followed. Older stocks of grease and oils were being left to go out of date. Lubricants which are out-of-date will not perform at the level for which they are formulated, and asset efficiency and reliability will suffer as a result.
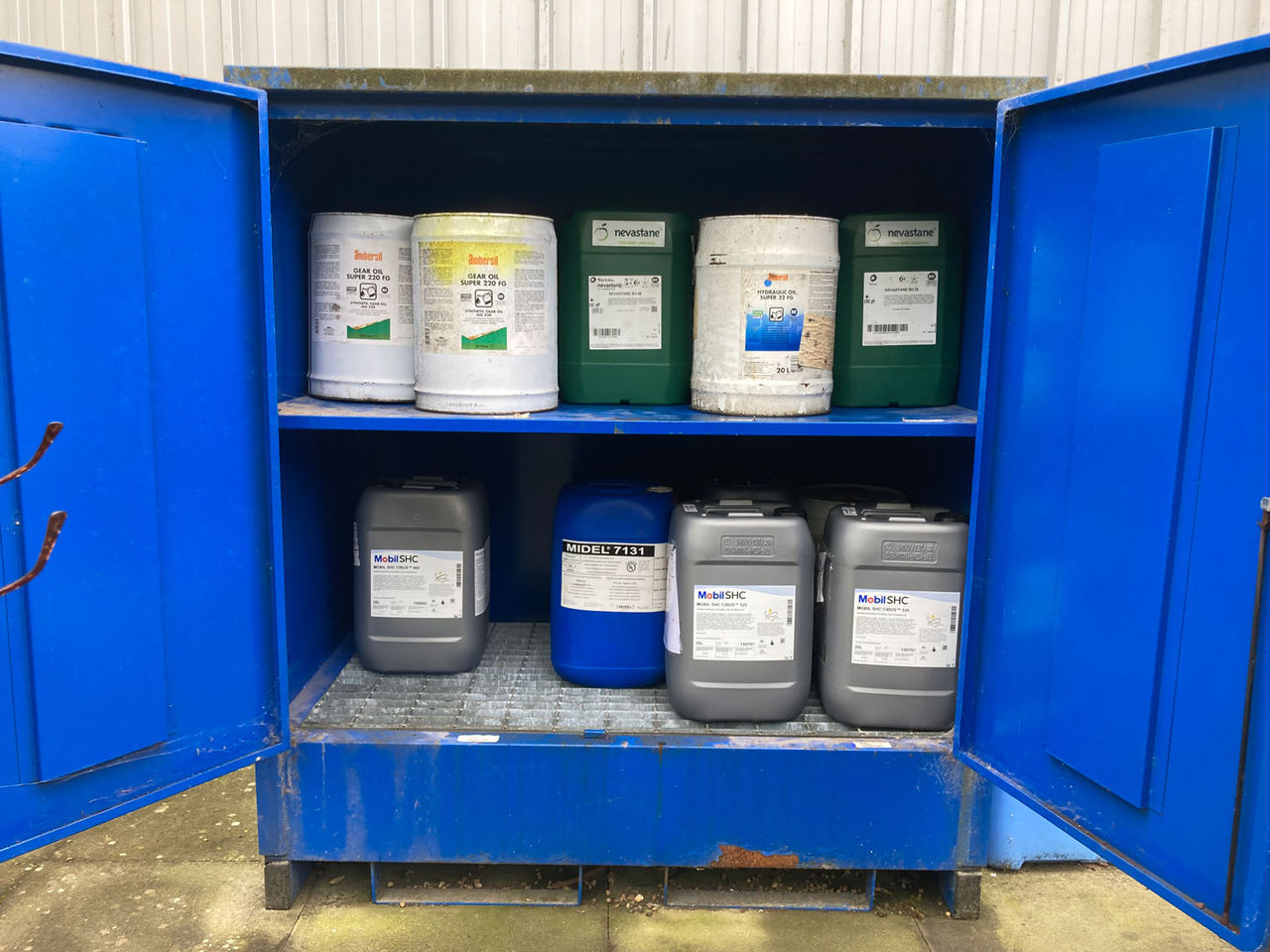
Moving onto the shopfloor, the lubrication experts from Moove noted that many of the gearboxes were located behind guards and screens. Before lubricant levels could be checked, the asset had to be isolated and the screen or guard opened for access. This meant excessive machine downtime, lost production, and increased labour costs for maintenance.
It was also discovered that the drive chains from the gearboxes were being manually lubricated with a grease not specifically formulated as a chain lubricant – reducing the effectiveness of the lubrication of the chains’ pins and linkages.
What’s in a name?
Inspection of several assets on the site revealed that their lubricant labelling was out of date or simply wrong.
For example, some labels specified discontinued products, while others failed to provide enough information – making it too easy to mistakenly use the wrong product. If, for example, non-food safe lubrication was used where food-safe was required, this would obviously breach Health & Safety protocols.
And even if the correct type of grease is used, mixing greases with different characteristics can lead to performance drops and premature bearing failure.
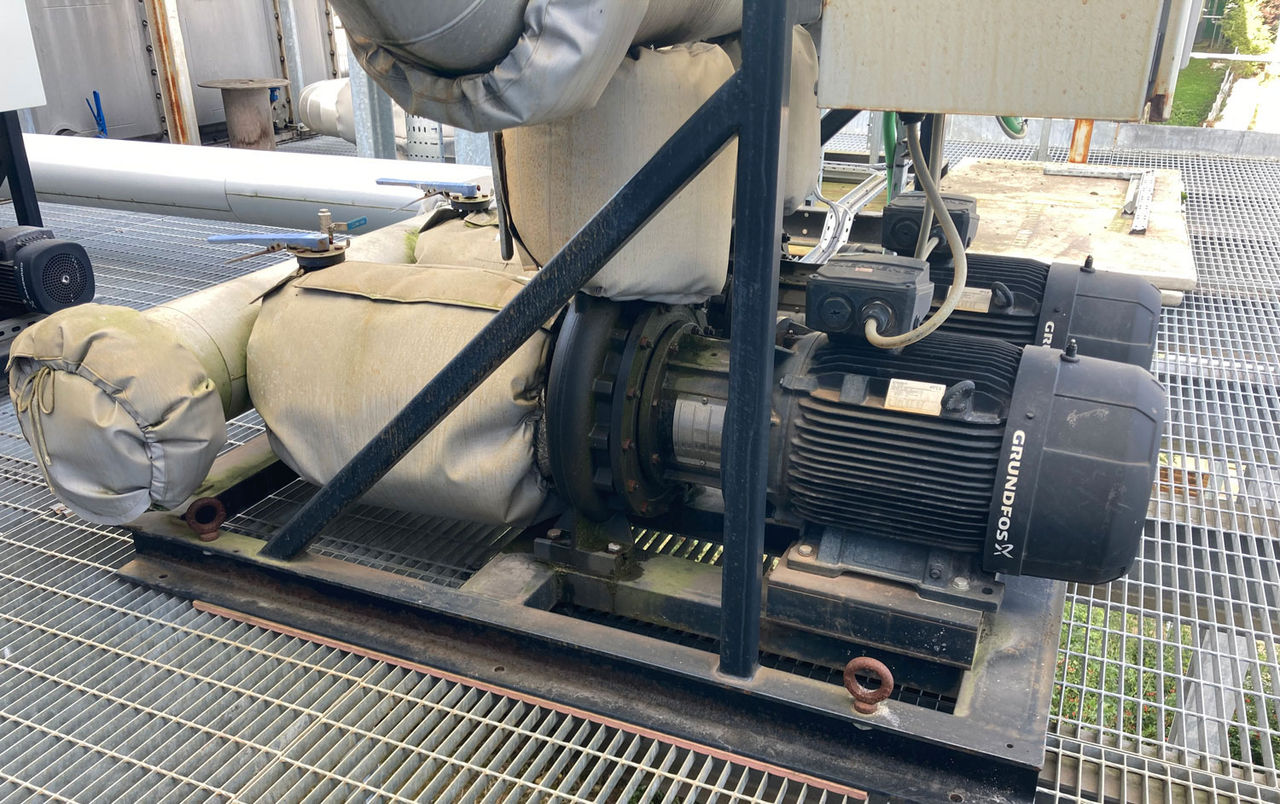
Gone missing
Some other assets inspected – such as Glycol pumps and mixer sets – required lubrication of their bearings or gearboxes. Yet there was no suitable motor grease or gearbox oil identified on site. Was there no lubrication being carried out – definitely leading to premature asset failure? Or was the wrong type of lubricant being used – meaning less effective lubrication, and a shortened asset life?
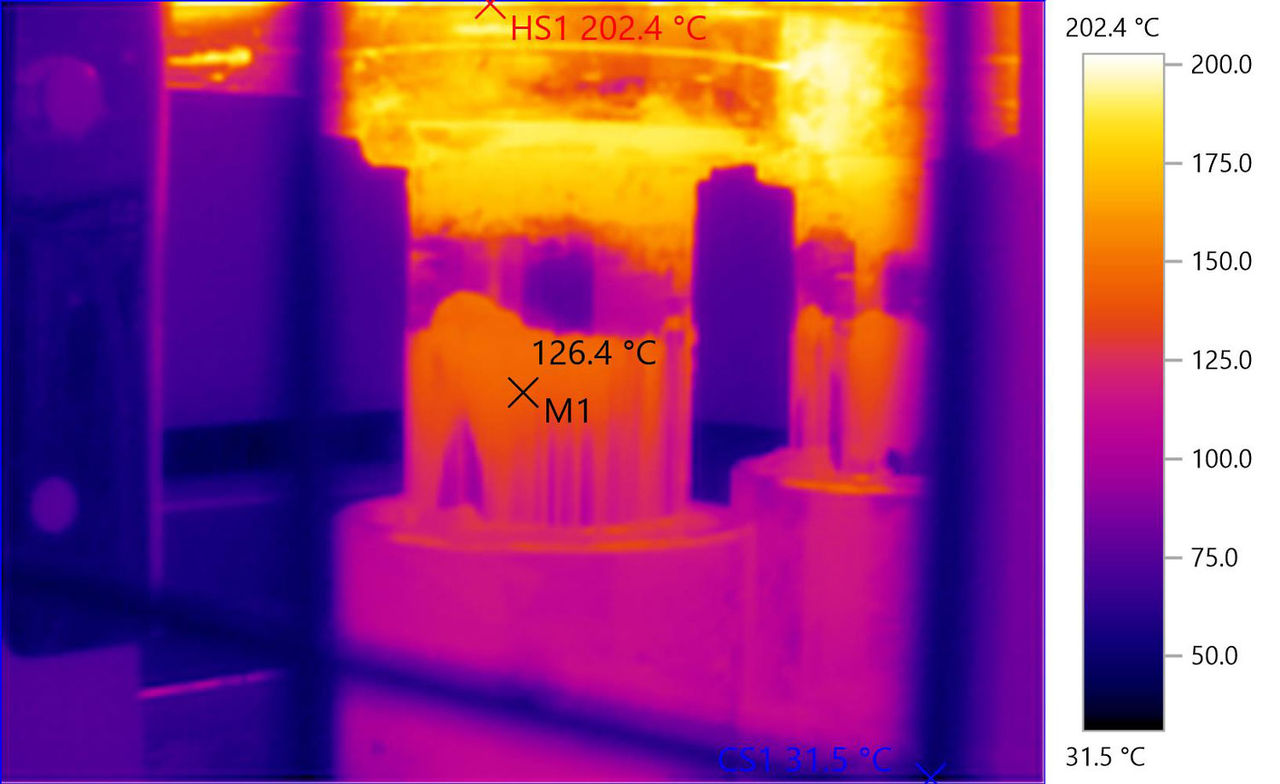
The last aspect of the survey was a thermal imaging report. This identified the hottest-running lubricated components, and enabled the recommendation of suitable high-performance greases capable of coping with the temperatures.
Moove-ing on
Having identified the problems Moove proposed a number of solutions, including: redesigning the stores; colour-coding lubrication points; installing sightglasses for critical assets in enclosed operating environments; conducting regular oil analysis to verify whether the best oil for the application is being used.
In some gear applications, simply changing from a mineral to a synthetic oil can deliver energy savings of up to 3.6% in gearboxes, and 6% in hydraulic pumps, through overall efficiency improvements. Which proves that when your assets and their lubricants work as well together as Moove and ERIKS do, there are real rewards to be had.
For more information on Lubrication solutions and to get in touch with one of our ERIKS Specialists, please contact your local ERIKS Service Centre, who will be happy to discuss your options.
#MooveLubricants #ERIKS #LetsMakeIndustryWorkBetter #Lubrication #Sustainability #CostSavings