In this article
Bearings grease: know your rights
If you want to improve the performance and reliability of your assets, while reducing maintenance and lowering energy costs, you need to know your rights. Right lubricant, right place, right amount and right time. Get all of these right for each of your bearings, and you’ll soon see the benefits.
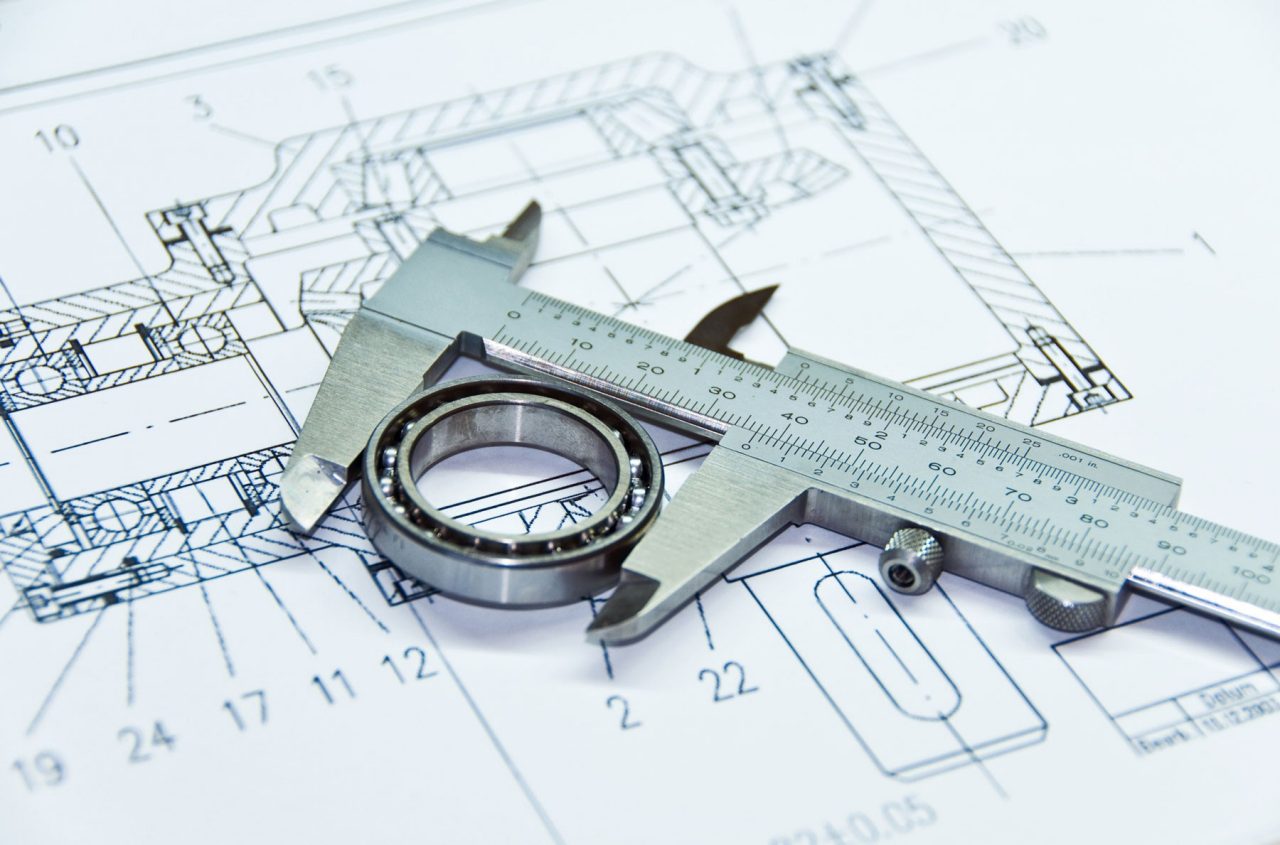
It’s not unusual for a customer to ask for bearing grease
Just that. What they’re forgetting is that, although there are not quite as many different greases as there are bearing applications, a speciality lubricants manufacturer like OKS can still offer as many as 50-60 different formulations to choose from.
And since the grease can make all the difference to asset performance, service life and Total Cost of Ownership, it’s essential to make the right choice. So here are the six key parameters to guide you to the grease you need.
1. Operating temperature
Greases can be affected by both high and low temperatures. A low temperature can make a grease highly viscous and unable to flow sufficiently. A high temperature can make the grease too liquid, so it fails to provide sufficient protection against friction.
Technical information for most greases does include a temperature figure. However this is usually the peak temperature at which the grease can operate – perhaps for only a few minutes. To choose an effective grease, you need to know it will work for its entire life at the service (usual operating) temperature of your bearing. The tech spec for all OKS greases includes this essential information.
2. Bearing type
Different bearings place different stresses on a lubricant. So a grease suitable for a radial ball bearing may not be the best choice for a cylindrical roller bearing, or a thrust and roller bearing. A cylindrical roller bearing, for example, creates higher mechanical stresses to the structure of the grease than other types of bearing.
3. Running speed
A bearing’s running speed (RPM) is a major influence on the choice of grease. Taking the running speed, the bearing type and the middle bearing diameter together, an expert lubrication adviser can calculate the DN Value, which – used together with a grease specification – enables identification of a grease with correct viscosity for the application.
4. Load
There are two bearing load considerations to take into account: amount and type.
The amount of load can be calculated from the basic dynamic load rating and the effective equivalent dynamic load. The first is based on a constant load in the appropriate direction for the type of bearing (e.g. radial for radial bearings). The second allows for external forces such as from power transmission, gravity and inertia.
The type of load then needs to be assessed. Is it continual, steady, changeable, rotating, oscillating, or even a shock load?
5. Environmental influences
Depending where the bearing is operating, and its application, there may be important environmental influences to consider. For example, does it need to be protected against rain, humidity, solvents or vibration radiation? Are there any vibrations?
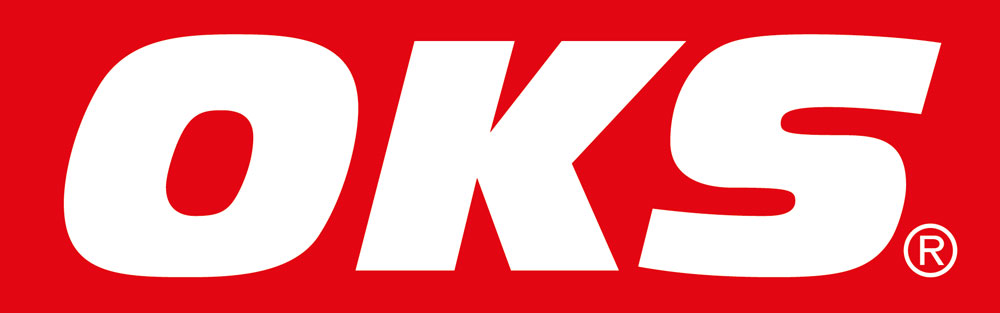
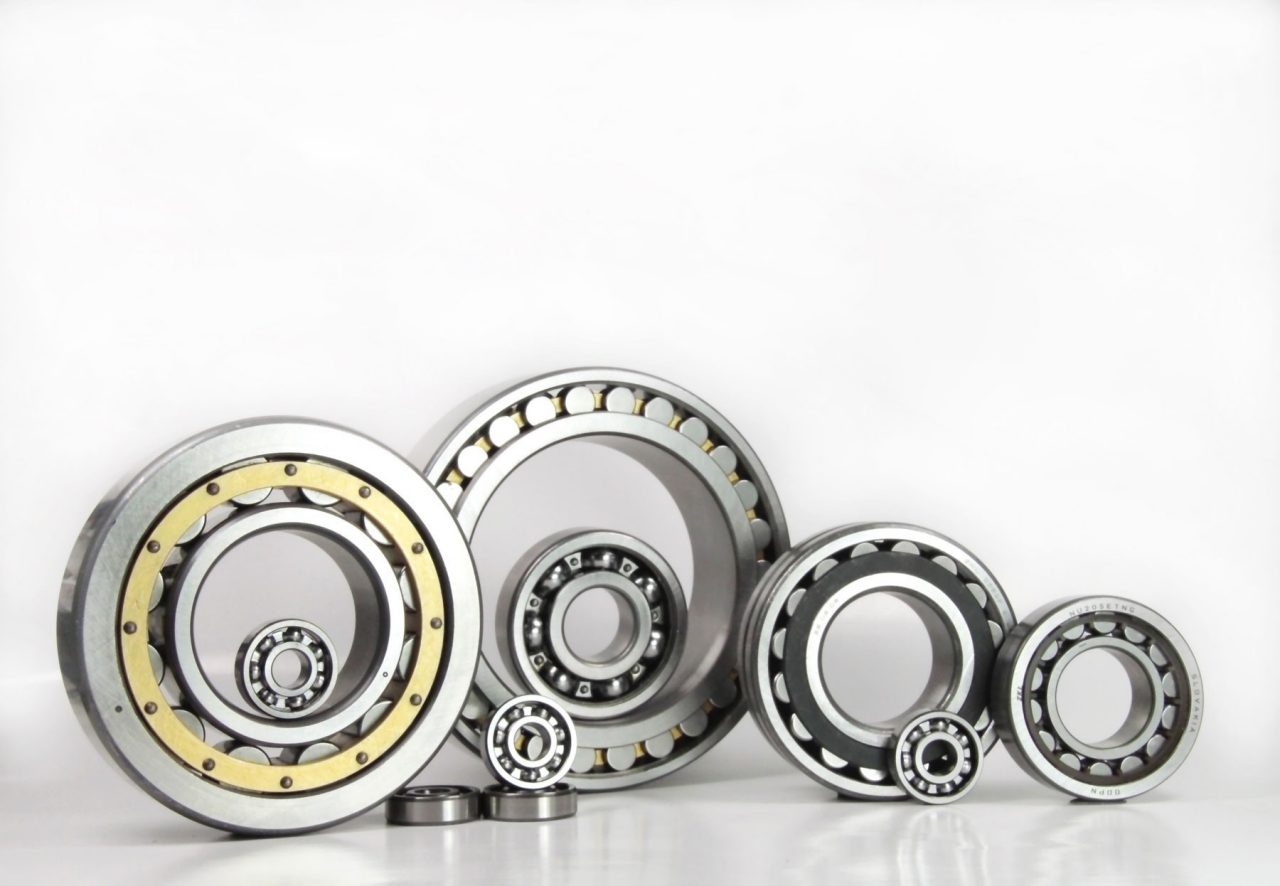
6. Regulatory requirements
Again depending on the bearing’s operating environment, there may be regulatory requirements and standards which the grease must meet. In a food production area, for example, the grease will have to be food safe, with NSF H1 approval. In other environments, such as maritime, it may need to be an Environmentally Acceptable Lubricant (EAL). There are also regulations applicable to greases for use in the manufacture of toys, cosmetics, pharmaceuticals and many other areas.
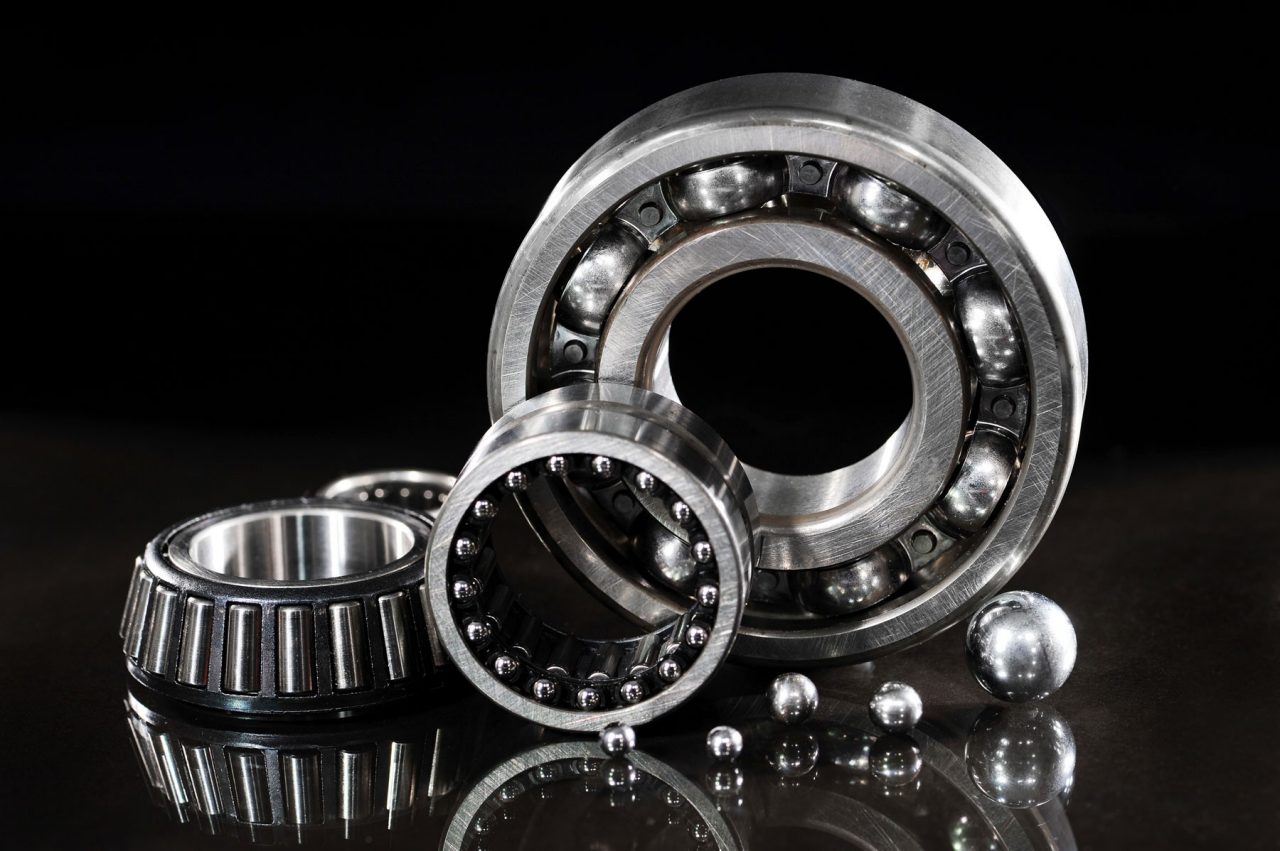
The right result
When you provide all the necessary information, an OKS lubrication expert will be able to help you find the right grease, and can also advise you on the right place to apply it, the right time to do so, and the right amount to use. (It’s often not appreciated that too much lubricant can do as much harm to a bearing as too little.)
Finding the information and getting the advice is well worth the effort. Because when you use the right grease in the right way, you can expect improved asset performance, increased reliability, reduced maintenance and downtime, lower energy costs, and higher productivity.
In other words: know your bearing lubricant rights and you can’t go wrong.
For more information on Bearings and Lubricant solutions and to get in touch with one of our ERIKS Bearings Specialists or Lubrication Engineers, please contact your local ERIKS Service Centre, who will be happy to discuss your options.
#ERIKS #LetsMakeIndustryWorkBetter #OKS #Bearings