In this article
Trustworthy technology that delivers improvements... NSK’s AIP Added Value Programme
All mechanical components have a finite life, determined by factors like design, quality, operating conditions, and load cycles. In today’s high-volume and high-cost production environments, it is often the life of a single bearing that dictates the efficiency of an entire production line. Reliability, therefore, is essential.
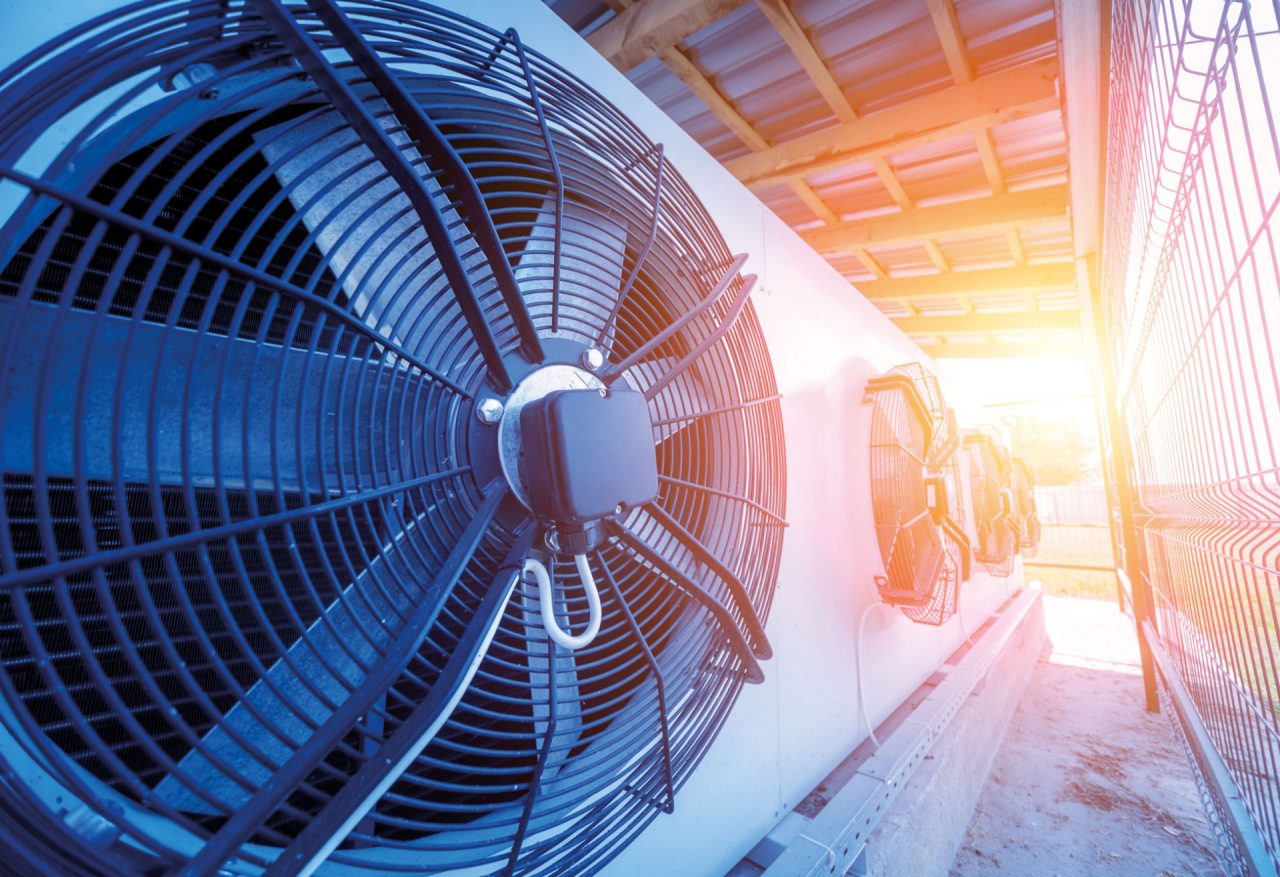
NSK’s AIP Added Value Programme is a proven continuous improvement philosophy that supports a future-proof business model and presents a real opportunity to unlock additional profitability through enhanced machine reliability, knowledge, skills development, and reduced working capital. This powerful and practical toolkit encompasses a full menu of NSK engineering and service solutions.
With AIP, it’s possible to make customer operations and maintenance processes far more efficient and, therefore, far more profitable. In fact, AIP can assist you in saving money at every stage of the programme, enabling end-users to secure, or even expand, a competitive edge by significantly improving processes and productivity.
Therefore, the engineering services of AIP aim to enhance machine reliability by finding better, more sustainable, and cost-effective solutions – adding real added-value to the supply chain. This is why NSK’s AIP carries the strapline ‘Improvement Pays.'
Identifying an efficient bearing solution is often a complex procedure that requires specialist knowledge and experience. It also calls for a carefully planned approach with a specific goal of increasing the productivity of machines and plant.
AIP, and its associated five-step value cycle is a standardised, tried and test process, as an increasing number of projects can now demonstrate:
- Evaluation
- Recommendation
- Implementation
- Validation
- Extension
Starting with Evaluation, the NSK team assesses the plant’s/workshop’s status quo and identifies areas of improvement, before moving onto the subsequent four steps of the cycle. Throughout the entire process, AIP experts work closely in conjunction with end-users to determine any possible issues, while working on an optimal solution and continually monitoring and assessing, until there is complete confidence in the results.
One of the most powerful elements of AIP is a process map, which focuses on creating a complete documented review of the production process from start to finish, placing particular emphasis on critical bearing applications. The AIP team then documents every bearing application and reference, the operating environment and, most importantly, how this environment can affect bearing life. Subsequently, the team will identify possible solutions using its experience and expertise. In essence, the end-user receives a clear roadmap to improving the life of their bearings, while reducing unplanned downtime and associated costs.
In addition to recommending optimised bearing solutions, NSK also provides information on machine component design, available part numbers and running conditions, while bespoke training is readily- available to support customer personnel. By strengthening their bearing knowledge, employees such as maintenance staff can help to improve machine reliability and overall profitability through reduced TCO (total cost of ownership).
The perfect fit
It goes without saying that correct bearing installation is a vital aspect in achieving machine reliability. Estimates suggest that poor assembly techniques are the cause of up to 20% of all bearing related problems, with installation damage ranging from raceway indentations, to seal deformation, or even cracked rings. When damage occurs, the bearing will not perform to its life expectancy, prompting premature failure and an increase in customer downtime and maintenance costs.
Fitting a bearing correctly requires the use of special tooling in order to apply the necessary force in the right place, or by heating components to achieve easy assembly. To assist customers in achieving the optimum result, time after time, NSK offers a range of maintenance tools as part of AIP+.
Application review
NSK’s comprehensive application review at the energy plant included a failed bearing examination from the drive and non-drive end bearings.
Observations included:
- Fretting corrosion on the external diameter of the outer ring.
- A wider and more pronounced running band, indicating that the raceway of both bearings had supported an axial load. This is unusual as the fan configuration had a fixed and free-end arrangement – to allow for shaft expansion from operating temperatures – thus the free end should only support a radial load.
- As the free-end bearing exhibited axial loading, NSK could attribute the root cause of the failures to incorrect bearing arrangement.
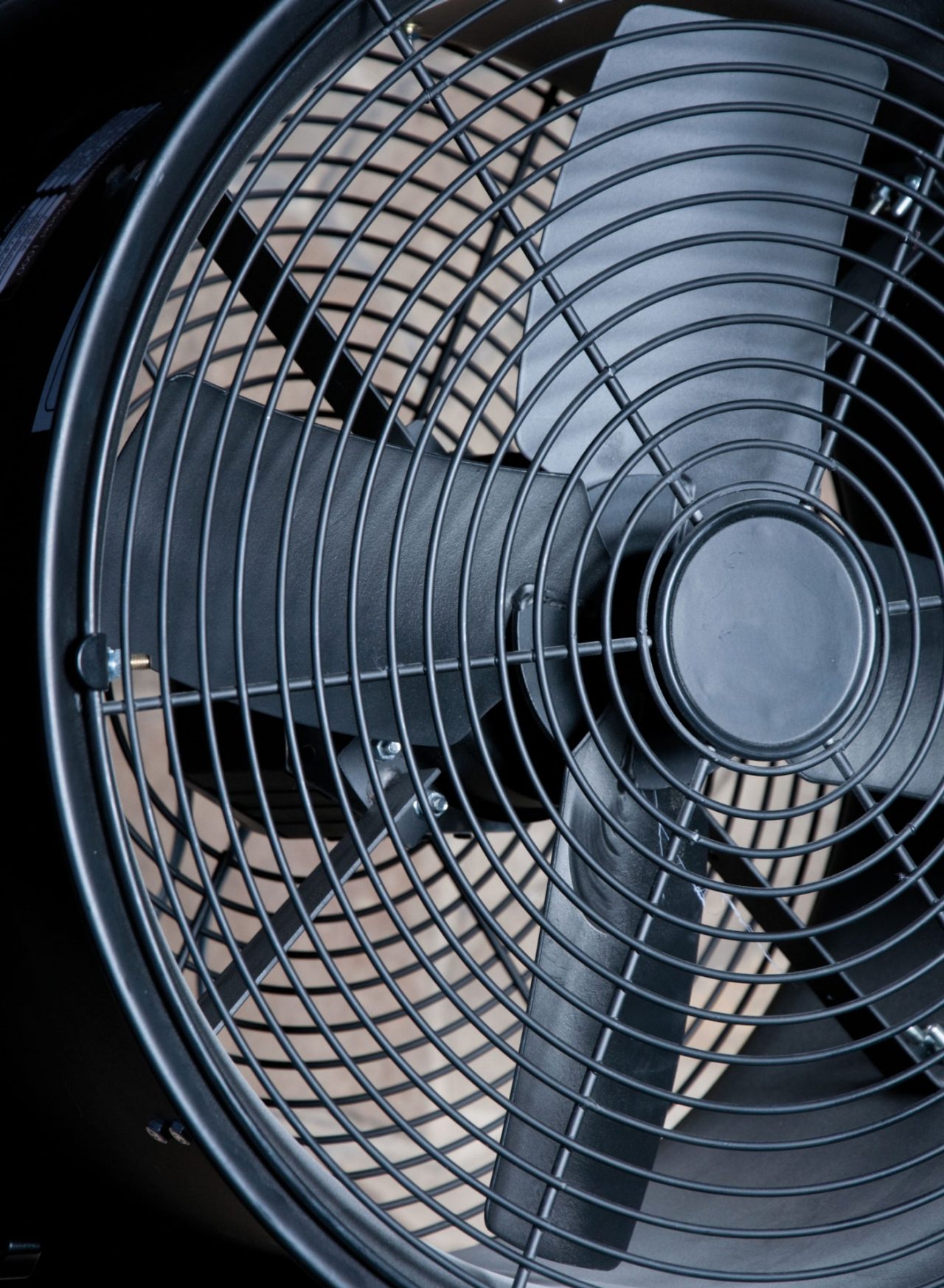
For example, the FTN333 kit for bearing installation contains a manual impact hammer with attachments that allow the safe fitting of bearings onto shafts and in housings. The wide high-impact head covers both the inner and outer rings simultaneously, thus avoiding striking a single component and causing internal damage.
Or for times when the mechanical process is too aggressive, NSK recommends the use of an induction heater that safely heats the bearing, expanding the inner ring so it can slide easily on to the shaft without damage. Once in place, performing an alignment process will help keep the bearing running square and for longer. For machines that employ pulleys and belts, NSK LAB-SET will snap into the grooves, so the dual lasers can quickly and easily identify any mounting errors.
NSK offers LAS-SET – a twin laser system that can accurately align couplings up to 2m apart, with an intuitive display guiding the user through the correction process, including soft foot checks and shimming. Again, NSK has the capacity to provide comprehensive training in this area, focusing specifically on the correct mounting and dismounting of your bearings. Improvement pays resulting in substantial savings Among the many plants and facilities benefiting from AIP in the UK, is a renowned electricity producer that was experiencing frequent and inconvenient breakdowns due to bearings failures in two industrial fan units. The bearings were, on average, failing every three months, a situation that was taking three engineers, 10 hours to remedy, each time, incurring extremely high costs per breakdown situation.
Following an application review
A high-capacity spherical roller bearings with SNN plummer block were recommended, in addition to correcting the fixing arrangement.
A trial of the spherical roller bearing units was conducted, with NSK’s engineering team overseeing the installation and implementation of the recommendations. The result was zero bearing failures over a 12-month period. Furthermore, the solution offered increased productivity with reduced maintenance and downtime costs, and four times greater bearing lifecycle. As can be seen in this particular example, operating with the wrong bearings or fitting them incorrectly can significantly reduce the output of machines, and even cause a whole plant to grind to a halt, incurring unimaginable costs.
Here, the change of bearing and fixing arrangement led to the delivery of €134,040 in annual cost savings.
In essence, NSK’s AIP makes operation and maintenance processes more reliable, efficient, and profitable by saving money at each value-added step. AIP also solidifies the relationship between OEM, distributor, and end user, helping successful businesses grow to a larger scale. Based on product quality and reliable customer support that helps nurture deeper understanding, NSK builds stable and strong long-term partnerships that deliver a more rewarding future for everyone.
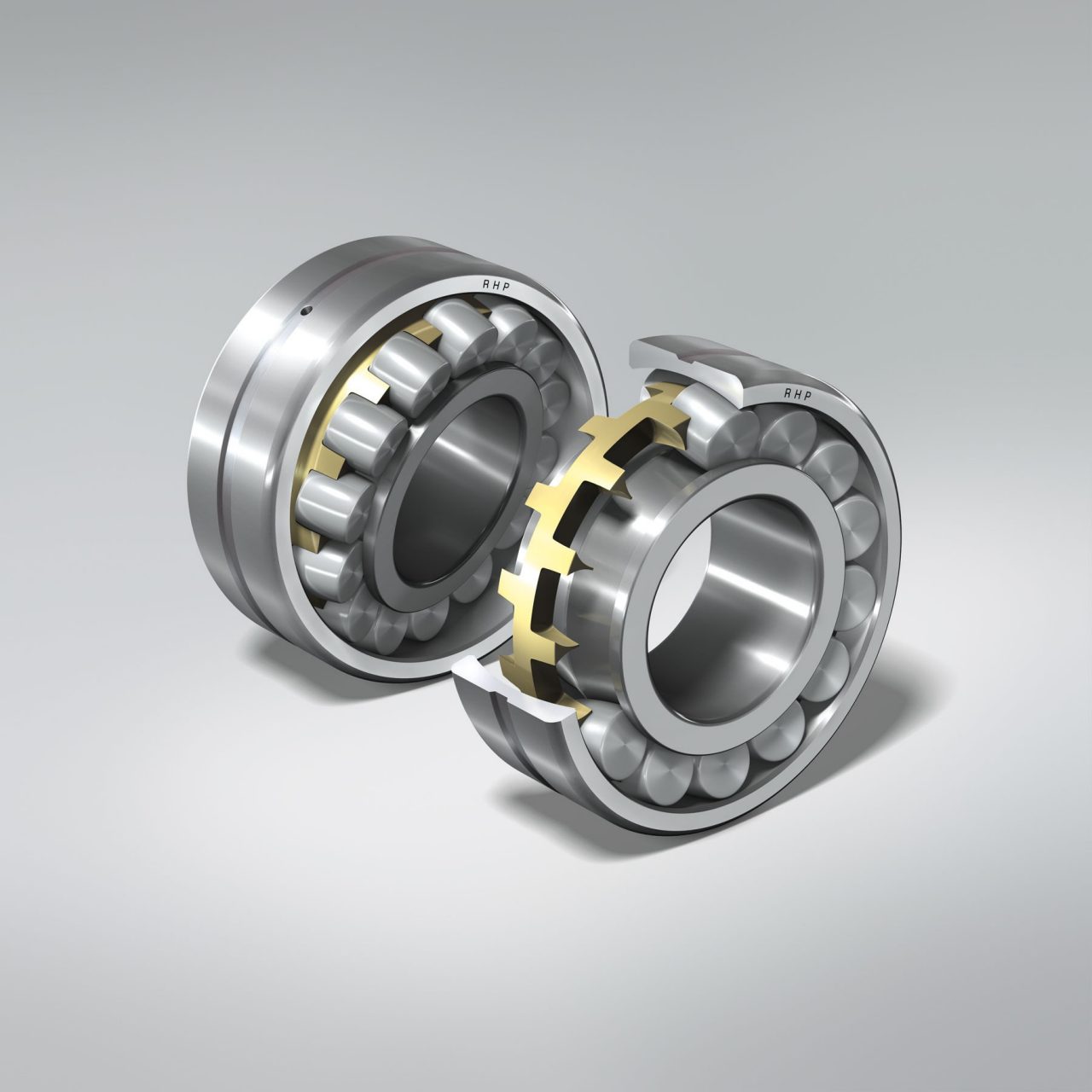
For more information on Bearing & Lubrication solutions and to get in touch with one of our ERIKS Bearings Specialists or Lubrication Engineers, please contact your local ERIKS Service Centre, who will be happy to discuss your options.
#NSK #AIP #Bearings #ERIKS #LetsMakeIndustryWorkBetter #Engineering #Training #CostSaving