In this article
Can you mix water with oil? ROCOL has the answer.
It wasn’t the waters that were troubled at a UK water business. It was the maintenance engineers. But pouring the right oil onto the problem could still help. The engineers were watching millions of pounds being spent annually on energy, to power motor and gearbox drives at their water treatment plants. What they wanted was a lifebelt to save the money from going down the drain. And they got one, in the form of a unique Rocol service to help them find the solution.
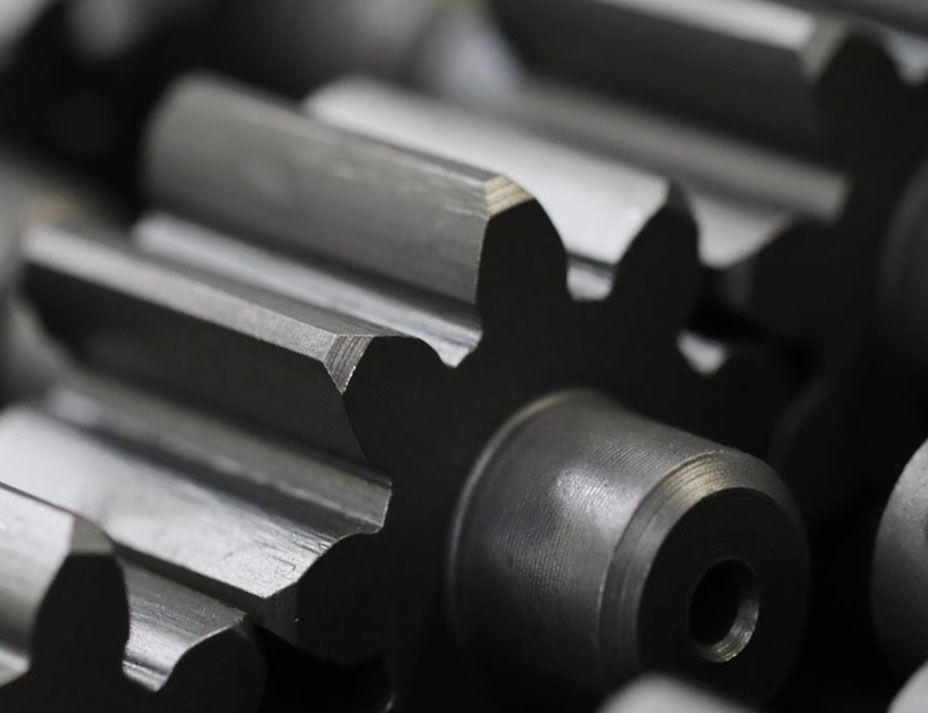
The engineers were watching millions of pounds being spent annually on energy, to power motor and gearbox drives at their water treatment plants. What they wanted was a lifebelt to save the money from going down the drain. And they got one, in the form of a unique Rocol service to help them find the solution.
As a leading supplier of specialist lubricants for industry, Rocol has decades of experience in matching the lubricant to the application. And a comprehensive range of technically advanced specialist industrial lubricants to choose from, to ensure customers get the performance they want, and can rely on, whatever their lubrication requirement.
What the water business wanted was an energy-saving solution which could help to reduce their six figure annual electricity bill, without compromising asset reliability.
Finding the solution began with Rocol’s unique six-month comparative trial.
Trial and aeration
The customer’s main area of energy consumption was the drives for motors and gearboxes for the waste water aeration tanks. So when Rocol proposed a comparative trial of lubricants from four different companies, these were the ideal assets to put the oils to the test.
Firstly, the energy consumption of each gearbox was monitored and recorded for a set period, to provide baseline data. Then each lubricant manufacturer involved was provided with six identical aeration tank drive gearboxes, for the six-month lubricant trial.
These trials are frequently offered by Rocol, as a way of proving to potential customers that it’s not always the figure on the lubricant price tag that’s the most important. A lubricant that looks cheaper in the short-term may prove to be more expensive in the longer-term, if it reduces efficiency, increases energy consumption, or even increases maintenance costs and shortens asset service life.
Talking the torque
The lubricant proposed for the trial by Rocol was SAPPHIRE Hi-Torque. This range of high-performance, semi-synthetic gearbox fluids is formulated to minimise wear, reduce the risk of breakdown and significantly extend gearbox life.
Among the benefits of SAPPHIRE Hi-Torque is its wide temperature resistance, from -20°C to +120°C. It also has outstanding EP performance (with a 560kg weld load), and provides excellent thermal stability.
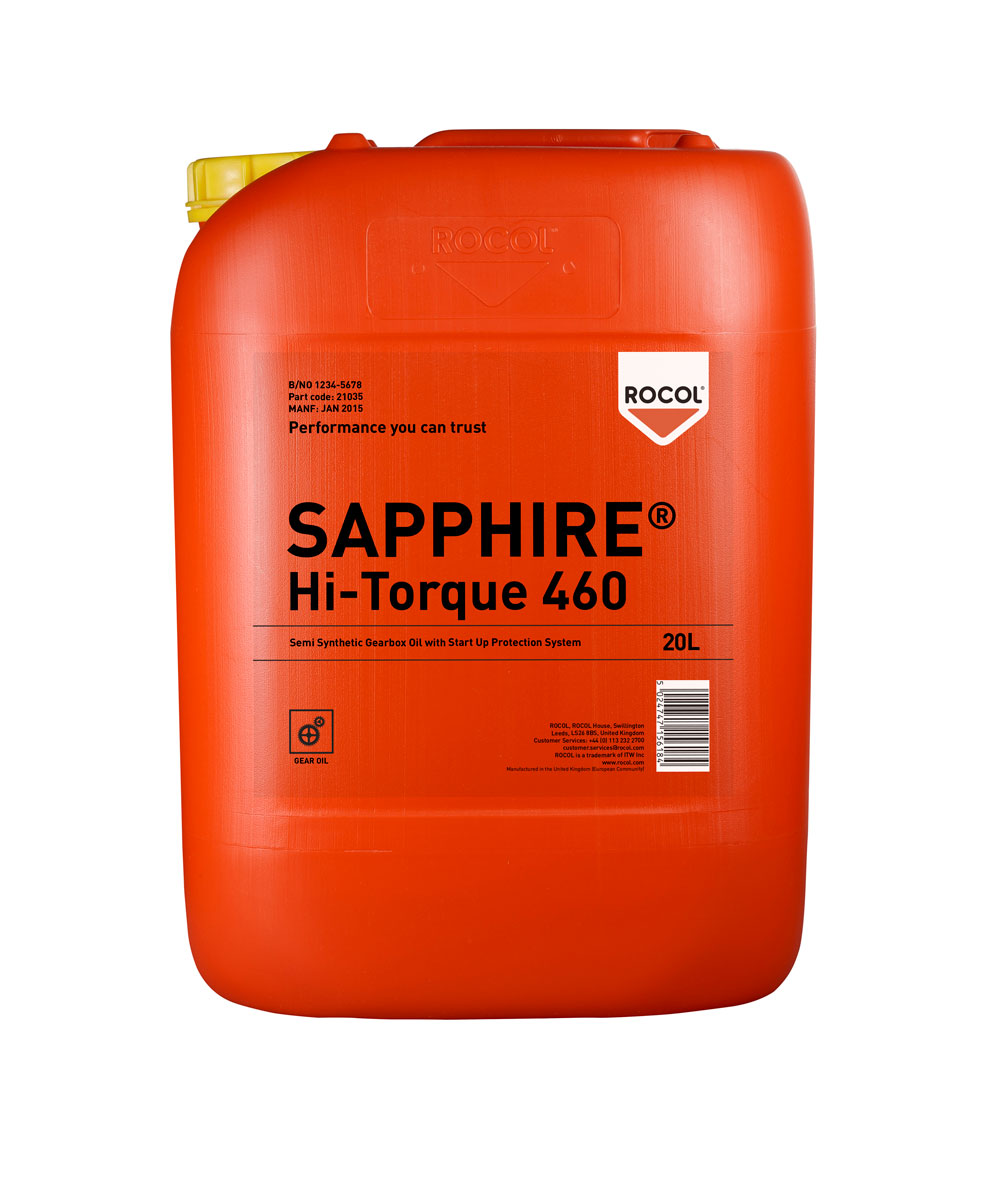
SAPPHIRE Hi-Torque also incorporates the Start Up Protection System unique to Rocol lubricants, which offers maximum protection. Creating a tenacious and low-foaming film – with excellent resistance to water wash-off – and protecting against corrosion, Rocol SAPPHIRE Hi-Torque’s semi-synthetic formulation makes it compatible with most types of mineral and synthetic oils. Dyed blue for visibility, and with a high level of stability, it is effective throughout extended relubrication intervals – helping to noticeably reduce lubricant use.
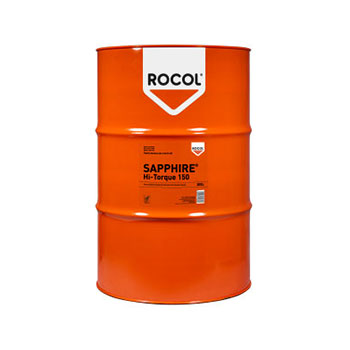
Oil in all
The results of the trial proved so successful that the customer decided to roll-out the chosen oil not just for use in the aeration tank drive gearboxes, but in all gearboxes across all their eight sites.
And the oil they chose? Rocol SAPPHIRE Hi-Torque, of course. The trial showed that after six months, SAPPHIRE Hi-Torque saved over 4% of energy consumption, compared with the oil previously used by the customer.
Across the customer’s eight sites and previous total energy cost of £477,800, that equates to a cost saving of £19,140.
Although the savings were realised through the premium quality of Rocol SAPPHIRE Hi-Torque, the experience of Rocol’s service engineers also played a part.
By carrying out the installation of the oil for the customer, they ensured that exactly the right amount was used for each application. This avoided both under-lubrication and possible asset wear, and over-lubrication and oil wastage. And it provided the most efficient lubrication for optimum asset performance and maximum energy cost saving.
Saving money like water
Rocol SAPPHIRE Hi-Torque gearbox oil helped the water business to realise significant energy cost-savings across their eight sites.
Site
Total Energy Cost
Saving (4%)
1
£14,200
£570
2
£32,300
£1,300
3
£41,400
£1,700
4
£186,300
£7,500
5
£110,600
£4,400
6
£16,800
£670
7
£55,400
£2,200
8
£20,800
£800
£477,800
£19,140
For more information on Bearing Solutions and to get in touch with one of our ERIKS Specialists, please contact your local ERIKS Service Centre, who will be happy to discuss your options.
#Rocol #ERIKS #LetsMakeIndustryWorkBetter #Bearings #Innovation #Water #Oil #Solutions #Sapphire #Hi-Torque #Ultra