In this article
8 out of 10 bearings can’t be wrong... Getting the right lubrication with ROCOL
Most industry experts agree: 8 out of 10 bearing failures are not the result of bearing faults. They’re caused by poor lubrication management and contamination issues. Or to put it another way: it’s not the bearings that are wrong, but how they are maintained. An effective, regular maintenance routine using carefully selected high-quality grease is the solution to reduce bearing failure, increase bearing life, and minimise costly downtime.
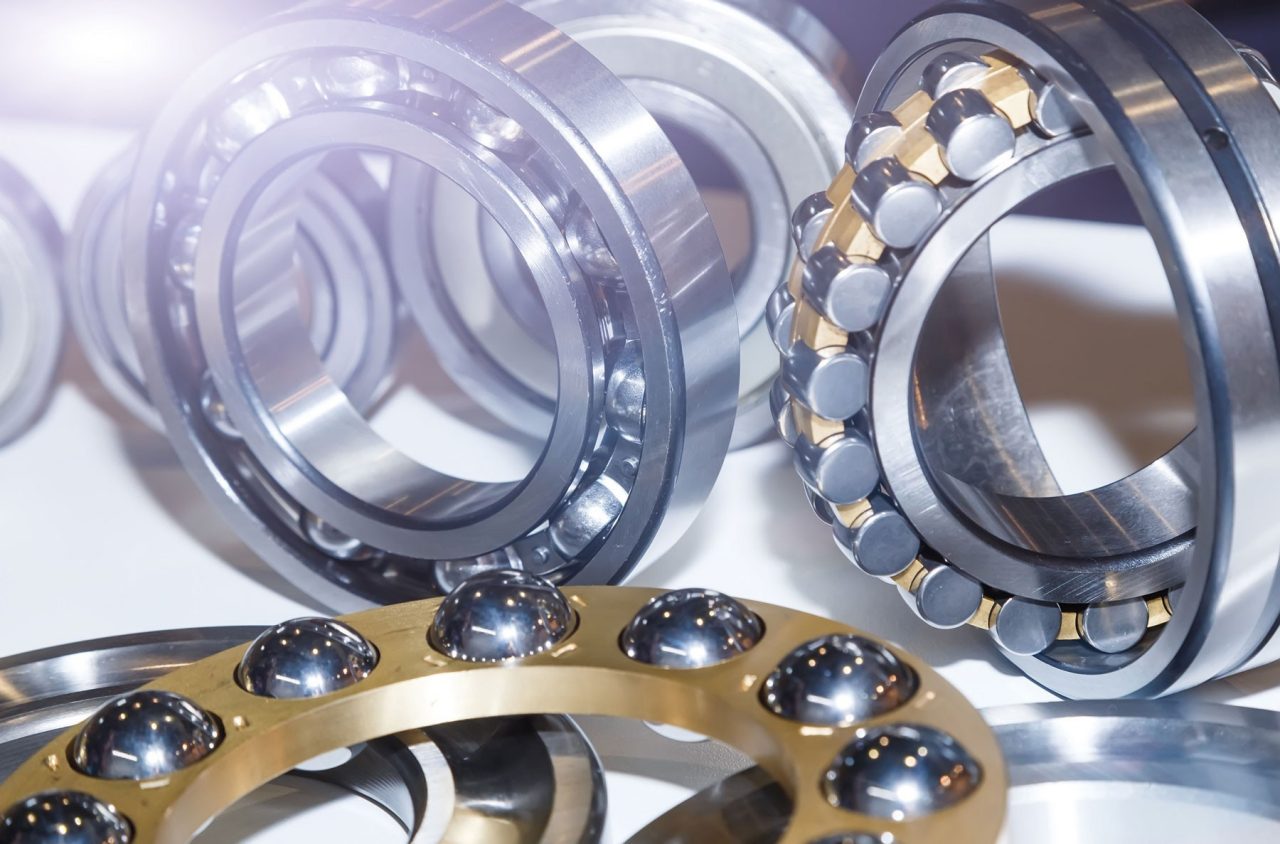
Unlubricated bearings will commonly overheat as a result of friction, wear excessively, and corrode. And when those things happen, at best you can expect less efficiency and poorer performance. At worst, machinery could seize, or bearings could fail prematurely, with all the associated effects and costs of downtime, lost production and bearing and shaft replacement.
So how does a bearing grease help, and which one should you choose for your lubrication regime?
The power behind the oil
Strictly speaking, it’s not the grease which does the important job of keeping bearings lubricated. It’s the oil within the grease. But that oil is a more effective lubricant because of the way grease helps it to work.
While oil flows, grease clings. So, when it’s placed on a bearing it stays in place for longer, allowing the oil it contains to lubricate for longer in the right place. Grease is also easier to apply than oil, and as well as being a lubricant ‘carrier’, it can act as a seal protecting the bearing against ingress of contaminants. Putting all these properties together means the right grease in the right place at the right time can help to increase bearing life, prevent premature bearing failure, extend relubrication intervals and reduce downtime. Which means less lubricant is required, maintenance costs are reduced, costly unplanned downtime is avoided, and productivity is increased.
How to choose your grease...
There are almost as many bearing greases as there are bearings. Choosing the correct grease for your application and operating conditions will make all the difference to bearing wear, operation, and bearing life.
- The first consideration is the operating conditions. Is the bearing operating:
- in a food/clean environment
- under extremes of temperature or condition
- at high speed (faster than 3,000rpm) in wet or humid conditions
- under high load?
Next, what type of bearing is being lubricated? There are basically two categories: plain (such as phosphor bronze bushes) or ball, roller, needle and so on.
Lastly, what is the bearing operating temperature range: low, medium or high? (The parameters will vary depending on whether the bearing is operating in a normal, food or wet environment.) There are greases in the ROCOL® Sapphire® family to match all these variables. And all the greases in the range typically last three times longer than conventional grease. That means longer periods between relubrication, lower grease consumption, and lower lubricant costs.
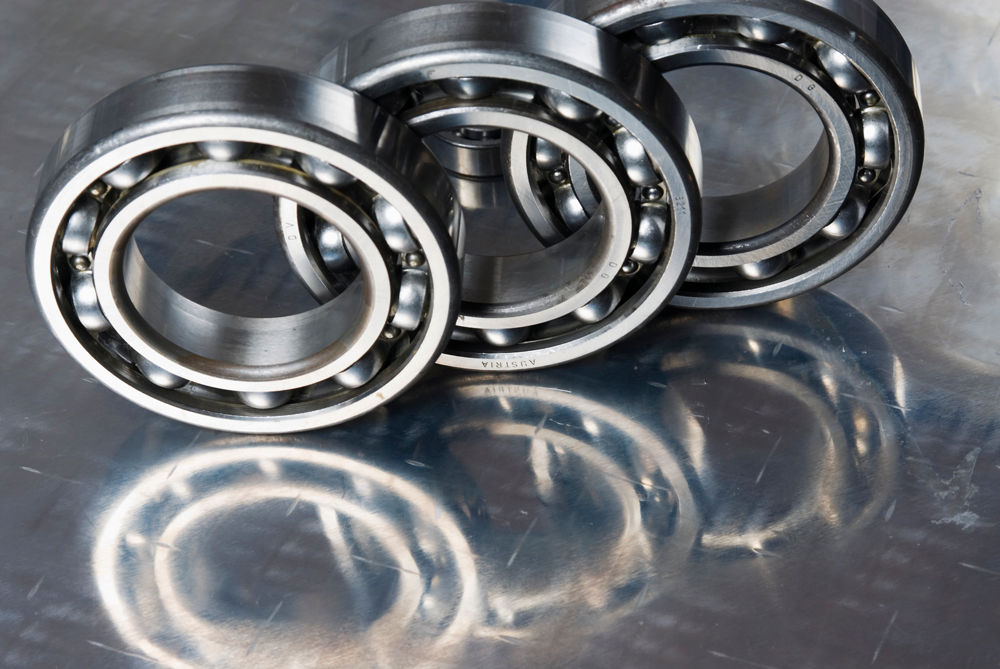
ROCOL Sapphire bearing greases are also noted for their outstanding performance under extreme pressure, compared with conventional lubricants. This means bearings last longer, need fewer unplanned repairs, and break down less often.
Lastly, ROCOL Sapphire greases are highly resistant to oxidation. This helps to extend relubrication intervals, which in turn means less grease is required overall, and lubricant costs are reduced.
You can find full details to help you choose your ROCOL Sapphire grease in the ROCOL Bearing Grease Guide. Or speak to your usual ERIKS representative for expert lubrication advice that gets 10 out of 10 every time.
Frying tonight – and the next 63 nights
- A large fryer at a major food manufacturer’s site contains 15 bearings. These were failing after three weeks, at a replacement cost and labour time of £82.56 and two hours each. The total annual cost of bearing replacement was £63,158.40
- ROCOL recommended SAPPHIRE Endure grease, which is ideal for aggressive environments subjected to extreme heat. The high-performance characteristics of the grease also enabled the customer to change to less costly bearings.
- The combination of SAPPHIRE Endure and more cost-effective bearings means each bearing now lasts for a minimum of nine weeks, with a replacement cost of just
- £16.12 each – saving £66.44 per bearing. Labour hours have also been reduced, from 34 to 12 hours per year. Total bearing cost savings are estimated at approximately
- £20,367 per year.
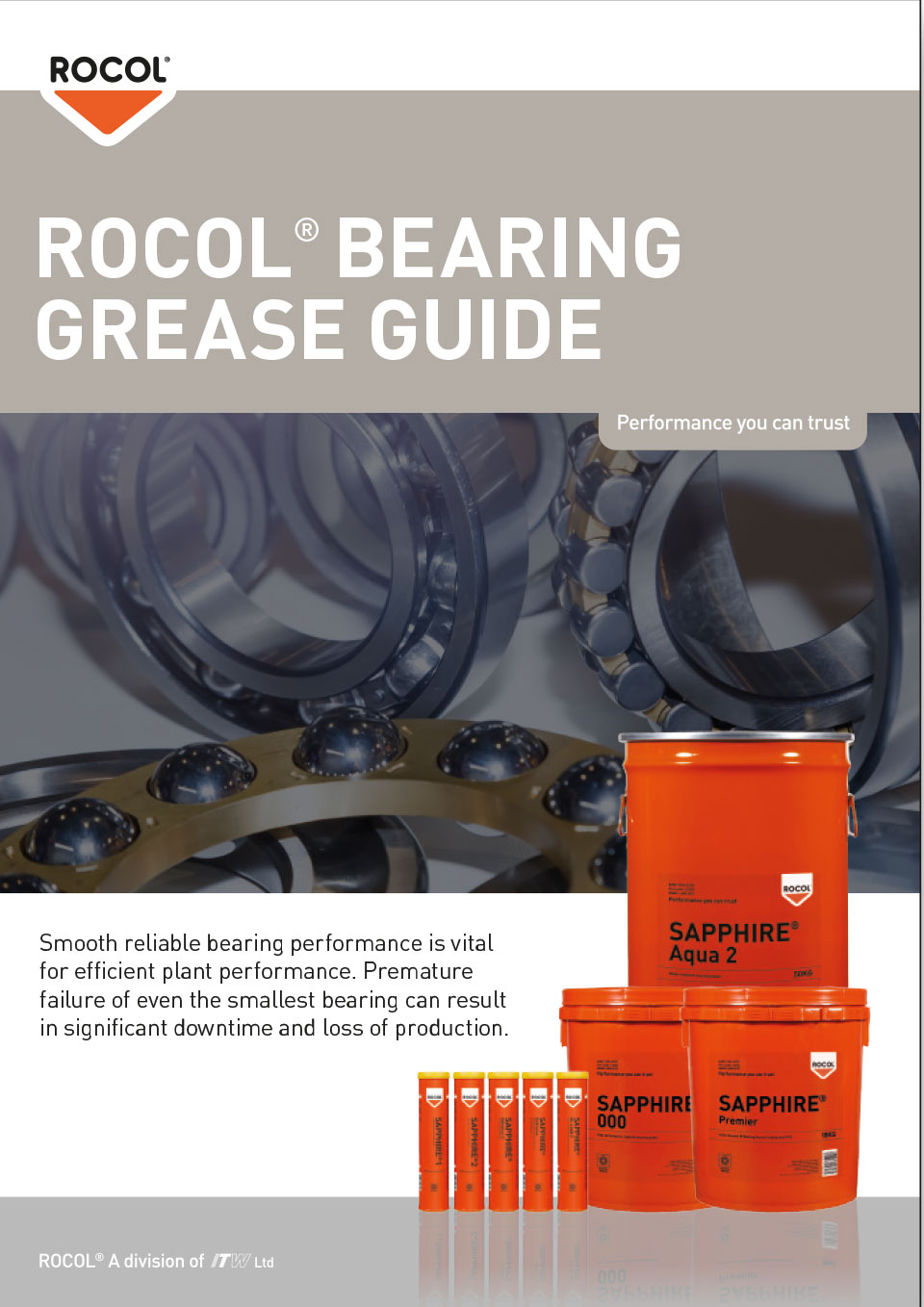
For more information on Bearing & Lubrication solutions and to get in touch with one of our ERIKS Bearings Specialists or Lubrication Engineers, please contact your local ERIKS Service Centre, who will be happy to discuss your options.
#ROCOL #ERIKS #LetsMakeIndustryWorkBetter #BearingsGrease #Lubrication