In this article
When a Component Fails: Fast Fix or Future-Proof
Industry’s productivity, profitability and reputation depend on the correct functioning of its equipment. But, when equipment fails, is a quick fix or a detailed investigation the best course of action, and what role can Total Cost of Ownership calculations play in the final decision?
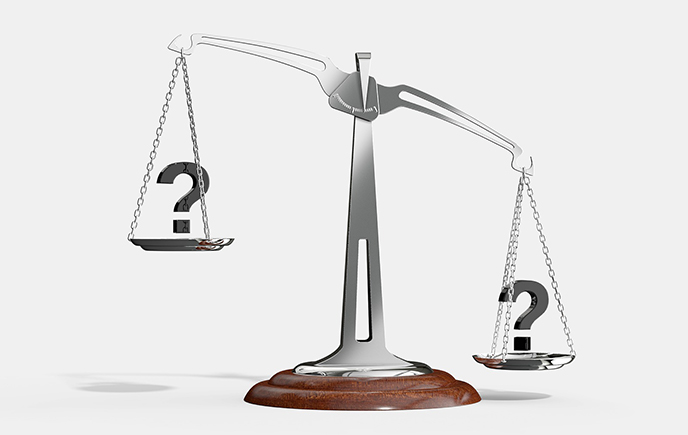
Most industrial sites, and their equipment, are made up of a variety of components, from pumps, bearings and connections, through to valves and motors, all of which must function properly in order to maintain optimum output.
When one of these components fails, those responsible for them are faced with an immediate question: repair or replace? What key factors should be taken into account with any repair or replace decision? Should the equipment be given a quick fix, or should it be future-proofed to prevent further failure?
Factoring in the Cost
The first key factor is cost. With a pump that is out-of-action due to a damaged shaft, for example, the decision to repair or replace will depend largely on the cost of the pump, and the ease of sourcing and installing a replacement.
A single stage pump, perhaps with a drive of up to 15 kW used in light industrial applications, may be easier to replace rather than repair, because the cost of replacing failed components is uneconomic for the pump user. “Engineered” pumps used in industrial process applications are a different case altogether. These pumps are designed to withstand more arduous duties, which is reflected in both the construction and purchase price. At this point, repair makes much more sense.
Getting to the Root of the Issue
The second big issue is production disruption. It is not uncommon for facilities to run on the basis that key equipment or components will regularly fail, so a ‘spare’ is always kept on hand to keep things going. Those with ultimate responsibility need to weigh up whether this is a sustainable strategy, or whether a more detailed analysis is required.
A root cause analysis will get to the bottom of why a specific component keeps on failing by taking into account start-up procedures, workload, and speed, in order to identify whether the component is properly suited to the machinery and the application. The downside, of course, is that root cause analysis takes time and can often only be completed during planned downtime. Inevitably, production schedules may dictate the need for a quicker solution.
Got a Spare
The third key factor is spares availability. Ready access to spares is a key criterion in assessing whether a fast fix or a future-proof solution is the best course. To use the pumps example again, a water pump in a light industrial application all-too-often comes out on the side of replacement, once the costs of labour, the part itself and downtime are all calculated. Process and wastewater pumps are a different case, with manufacturers often making ‘repair kits’ available for a variety of components that are prone to wear.
No Support for Obsolescence
A final factor I would highlight is obsolescence. There are plenty of machinery and components in the field that are more than 30 years old. They may no longer be supported by the original OEM, or the cost of spare parts may be increasing year-on-year. The key issue is to assess whether continuing to use this equipment poses a risk to operations. If spares and repair kits are readily available, then it is a viable option to keep going. If not, then the risk and costs of downtime, parts and labour will make repair uneconomic.
This is where total cost of ownership calculations can help the decision-making process. They require industry to consider a wider scope of variables across both the short and long terms. The upfront cost of equipment can often be lower over the longer term when variables such as downtime, spares, maintenance time, and even running costs are taken into account, but the calculation and ultimate decision can look very different.
Getting outside assistance can be key in this process. While the OEM will be an expert in the equipment, they will not necessarily be an expert in the couplings, pumps or motors that make up the conveyor, machine tool or pump. Investing time in sourcing and installing the optimum component for the equipment will improve total cost of ownership calculations over the long-term, and also increase equipment longevity, productivity and efficiency.
For manufacturers with high-value, high-cost equipment – particularly those installed in remote locations – implementing a condition monitoring strategy will further help to improve total cost of ownership, by identifying trends in machine performance and reducing time lost to unnecessary call-outs for maintenance and repair.
For more information please contact your local ERIKS Service Centre, who will be happy to offer assistance.