In this article
Planning for Obsolescence
Every pump has a Best Efficiency Point (BEP). And finding it will not only mean the pump will use the least energy for the highest performance. But also by operating your pump at or near its Best Efficiency Point, it will also mean increased reliability, so it pumps better, for longer.
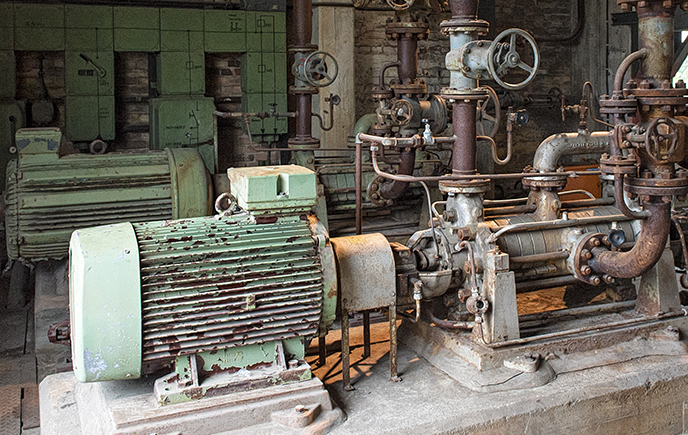
“Nothing lasts forever.” These three words may have become a staple of any brooding protagonist whenever a harsh reality check is due, but they’re also a fact of life. As manufacturers, buyers and engineers, we know this only too well. Even the most reliable and established products will eventually need to be replaced, whether that’s through wear, supersession or discontinuation.
Responding to obsolescence is a relatively accepted concept outside the world of manufacturing. Most of us would jump at the chance to upgrade our phone as soon as we had the freedom, and funds, to do so. Manufacturing, however, is more like the curmudgeon who prefers to stick to his rotary telephone, despite the fact that most of the numbers have peeled off, and the wires connected to the receiver are loose. We know what we like, and we stick to what we know.
What are the Consequences?
Many of us use legacy machinery, and there is nothing wrong with that. After all, replacing machinery wholesale is both expensive and disruptive. That is not to say, however, that its continued use will not pose problems.
The challenge many manufacturers face is sourcing the spare parts needed to maintain or repair legacy equipment. There are a number of approaches that have been explored in the past, but these come with downsides.
Stockpiling parts, for example, may seem like a sensible thing to do, but these stores will also need maintaining, rotating and reviewing on a regular basis. Spare parts do not have an unlimited shelf life. Elastomers and metals, for example, will start to degrade until they eventually become useless. When that happens, you might as well have thrown your money out of the window.
Furthermore, relying on legacy machinery also means relying on the staff that understand how to use it. Staff will not stay around forever – whether by retirement or a career change, you will eventually find yourself with a vital piece of machinery, and no-one who knows how to use it.
Without some kind of strategy in place, engineers can find themselves wasting valuable time while spare parts or know-how are sourced. In the most serious cases, production can be impacted – if not halted completely – if you are unable to find the parts needed to get your machine up and running again.
Time to Make a Plan
What, then, is the answer? Put simply, you need to identify the areas of your plant that are at the highest risks of obsolescence, and start mitigating these risks. This can be done in-house, but it’s better to use an asset management specialist.
The specialist will start by conducting a full obsolescence audit of your plant, during which they can identify any areas of concern and order them by “criticality”. This is particularly beneficial if budget is tight, as you can prioritise any further action accordingly. They should also conduct a processes and utilities audit, in which aspects such as reliability and energy efficiency can be examined and any areas for improvement identified.
What follows is known as an “asset consolidation”, wherein you can gain further insight into your stock, spares and storerooms. This will allow you to spot any purchasing trends that aren’t particularly cost effective, and organise your store to allow for the proper rotation of everyday items.
Once you’ve completed these steps, you can start implementing a set of KPIs to guide and focus your asset management activities. The final stage involves outlining and implementing a full asset management programme using “mean time between failures” (MTBF) and “mean time to repair” (MTTR) analyses. From here, you can start to build an effective preventative maintenance regime, which will reduce the likelihood of unexpected downtime as a result of part obsolescence or failure.
Knowledge is a powerful thing, particularly when it comes to planning for obsolescence. By being aware of the parts you use, the parts you’ll need, and the parts that may soon cease to exist, you can build an idea of what you will need to upgrade, replace or gradually phase out over the next few years, and factor these into a wider preventative maintenance schedule.
What’s more, by partnering with a specialist, you can be confident that no stone (or stock) will be left unturned.
You can contact your local ERIKS Service Centre, who will be happy to dicuss your options with you.
#ERIKS #LetsMakeIndustryWorkBetter #Replace #Upgrade
The Challenge of Obsolescence
NEW WHITEPAPER: Strategies for Managing and Maintaining an Ageing Asset Base
ERIKS has once again teamed up with the IET to create a new whitepaper exploring UK industry's exposure to obsolescence.
Discover current attitudes towards obsolecence, including policies and how it is being managed on the ground.