In this article
How to manage stock management
Stock management takes time, space and money. Done inefficiently, it takes too much time, takes up too much space, and costs too much money. So a Tier 1 automotive manufacturing facility – needing to accelerate access, maximise accuracy and optimise space – turned to ERIKS for a money-saving automated solution.
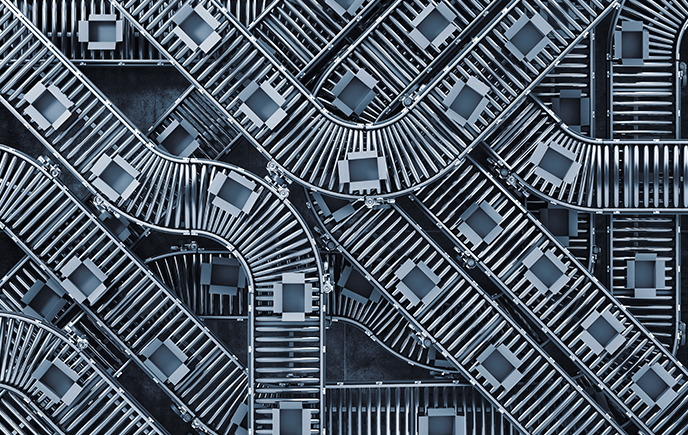
Traditional stock management forces skilled engineers to spend their valuable time waiting at storeroom counters when they could be getting on with their job. And even after a walk and a wait, there’s no guarantee the part they need will be available.
Most stock management systems rely on manual booking-out. So they’re at the mercy of forgetfulness or even dishonesty, as items removed go under- or unrecorded. At best, the result is empty shelves and engineers left empty-handed. At worst, a critical MRO item that’s unavailable can mean extended downtime and lost production.
With ERIKS’ help, by automating stock management and retrieval, the Tier 1 automotive customer was able to save time and space, and increase efficiency – recouping the cost of the project in just 30 months.
Stock up, and up, and up
For MRO parts storage, space is the first frontier. Valuable floorspace that could be put to more productive use has to be dedicated to storing parts where they are readily accessible by Stores staff.
In partnership with Agilon, ERIKS provided the customer with a storage system which utilises otherwise unused vertical space. The shelving racks are only 1.6m deep but up to 6m high, accessible only to stock-picking robots.
Now the customer can store 3,000 SKUs in two parallel racking runs only 14m long – releasing factory floorspace for other uses.
The stock is secure behind the racks’ metal-cladding, and anyone wanting to retrieve an item has it delivered automatically to an access point, with no need to physically enter the stores.
There’s also no need to wait for the item to be found. It can be ordered by digital input (via portable tablet or PC) from anywhere on site, and while the ‘customer’ makes their way to the access point, the robot will be quickly finding and retrieving the item. A touchscreen is also provided at the access point for on-the-spot retrieval.
Who, what, when?
Digital inputting ensures all transactions are monitored and recorded in real time, enabling full accountability and traceability, as well as 100% stock accuracy. The system can even be integrated with a customer’s SAP and TPM systems if required.
By knowing what items have been removed from stock, re-stocking will always be timely and accurate. Designated personnel can be automatically alerted when critical parts are removed from stock. And consumption reports will help to spot trends, identify spikes, and inform engineering analysis of potential issues with specific assets.
The digital input also makes it possible to place automated controls on stock access.
For example, a limit could be placed on how many items of PPE can be withdrawn from stock by any one person in any one shift.
In effect, this turns the stockroom into a giant automated vending machine for more effective management and reduced consumption of consumables. Access to high-value items (such as power tools) can also be restricted.
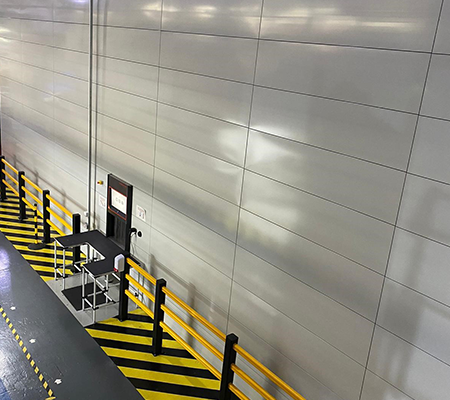
Right place, right time
Just as important as fast and accurate stock access is fast and accurate stock replenishment. Unless every single item is replaced in the correct place on the correct shelf every time, the whole system – whether manual or automated – slows down and ultimately breaks down.
The Agilon system maintains the stores in order at all times, through a carefully co-ordinated replenishment process.
When a replacement item is brought to the access point, the operator simply calls up the part on the touchscreen, and the robot arrives with the appropriate empty storage box. The part is placed in the box, and the robot returns the now replenished box to its proper position in the store, ready for easy access in minimum time, when required.
Critical items, crucial savings
The benefits of automated stock management and retrieval are clear.
A time and motion study identified 25,000 manual stockroom transactions per annum on average, each of which takes – on average – 235 seconds. Using the automated Agilon system, the time taken is reduced to just 40 seconds each: saving 1,300 man-hours per annum.
A subsequent cost/value analysis revealed savings of £100,000 over three years, against a system cost of £85,000.
The customer installed the original Agilon system for storage, management and retrieval of fast-moving, critical and high-value MRO items. Analysis of the savings achieved, after only one year, has encouraged them to consider doubling the number of SKUs managed by the system, and expanding them beyond MRO parts only.
But whatever they decide to stock within the automated system, one thing is certain. There will be sizeable savings in store.
Click here for more information on Asset Management, or contact your local ERIKS Service Centre, who will be happy to discuss your options with you.
#ERIKS #LetsMakeIndustryWorkBetter #AssetManagement